With Barbara Donohue
Today’s Machining World Archives April 2011 Volume 07 Issue 03
“Is it Good” investigates how new or unique products work by interviewing the people who developed them. In this interview, Pete Paulin, president of 300 Below Inc., describes why he believes that freezing metals at -300F can save you money, time and increase your bottom line.
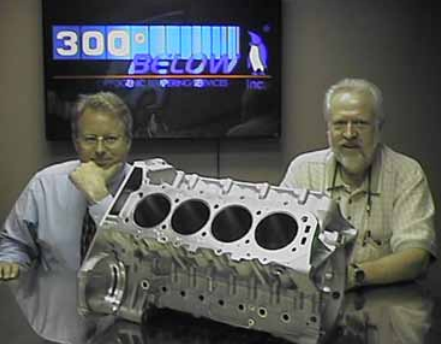
300 Below, Inc., in Decatur, Ill., cryogenically treats more than a million pounds per year of all different kinds and sizes of things—from tools to trombones to the optical bench for the $3 billion Cassini spacecraft. The company also sells cryogenic treatment systems.
Cryogenic processing’s claim is that it can improve material properties and performance for parts, tools or products made from metal and other materials. It gradually chills items from room temperature down to cryogenic temperatures, holds them at that temperature for a period of time, and then gradually warms them up again. There is science behind this process, even though it seems like black magic. When he was starting in the business back in the 1980s, 300 Below’s president Pete Paulin was told, “People will accuse you of being a snake-oil salesman.”
What happens in cryogenic processing?
We take the part and gradually transition the temperature into the cryogenic region, keeping the whole thing, surface and core, in equilibrium. We’re operating at 300 below zero, Fahrenheit. Then we gradually bring it back to room temperature. The net result is slow thermo-mechanical compression and expansion. This produces advantageous effects:
- With steel, any retained austenite is converted to martensite, a harder form.
- In many metals, micro-fine beta-carbides are created, which giving coherence to the material.
- Residual stresses are significantly relieved.
- The material is stabilized, so the part does not distort with changes in temperature.
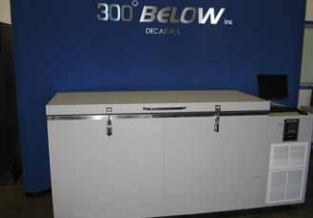
It’s not a miracle process to use instead of heat treating. It’s in addition to heat treating. The cooling part of heat treating does not stop at room temperature. If you look at the charts, steel with more than 0.4 percent carbon needs sub-ambient cooling to complete the change to martensitic structure.
Most metals respond well. We also treat other materials such as carbides, polymers, or crystals; many show improvements from the process, some do not. If they work, the results are very consistent.
We deal with both manufacturers and end users. Customers send in their parts and we turn them around in 72 hours. We have treated items as small as nanoparticles and as large as a 28,000-pound canopy die for the F-22 Raptor fighter from Boeing.
How was cryogenic processing developed?
The nearest thing we have been able to understand is that hundreds of years ago, caves were used for sub-ambient cooling. The Swiss and Swedish used sub-ambient cooling in early steel making and for making watch parts. Even before that, sub-ambient cooling was used for knife and sword blades. Today, castings are often left out in the weather to age before machining.
During WWII, cold processing at 110 degrees below zero was done with alcohol and dry ice.
The first commercial use of cryogenic treatment was developed by Ed Busch in 1966 in the Detroit area. He purchased air reliquifiers used in submarines to provide liquid air to produce very low temperatures, later using liquid nitrogen. He did the process by hand, sitting there with a clock and a thermometer. In the 1980s, I connected a microprocessor to control the process.
What can it do? Can it save money for the user?
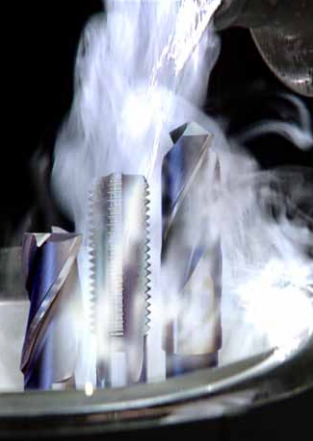
We often see longer life by 300 percent. Some applications improve by 50 percent, some by 700. Some materials don’t respond to cryogenic processing.
At a heavy equipment company, we treated their hobs at a cost of $7 each; the increased tool life saved over $200.
Suppose you use a particular type of twist drill that cuts 300 holes and can be reground four times. The same model drill after cryogenic treatment might cut 600 holes. That appears to be a 100 percent increase in life. However, because of the more refined grain structure of the treated drill, when you regrind it you need to remove only half as much material—you can do twice as many regrinds. So the treated drill cuts four times as many holes.
A screw machine company might have $5-10 million revenue per year. Of that, the tooling budget might be 5 percent. In a good year, the net operating income might be 5 percent. If you cryogenically treat your tools and double the tool life, the cost of tools goes from 5 percent to 2 1/2 percent, increasing the operating income by 50 percent—increased profit without doing anything else.
Since 1975, We’ve had a special process for brake rotors, which consistently gives three times the life. Cryogenically treated engine blocks for motor racing show increased life and higher horsepower.
Every year we process 4000 miles of guitar strings. It makes them sound brighter, prevents attack by acid from the fingers, and makes them last longer before breaking.
Sometimes it’s about product improvements, rather than saving money. We’ve stress-relieved musical instruments, knives, golf clubs, aluminum baseball bats, and 68,000 gun barrels.
Is it good?
Absolutely. It’s the coolest technology available today.
1 Comment
I actually use this process on broach bars for internal splines. It has increased the tool life of the broaches between sharpenings by 4 times. We tested untreated broaches to track wear on the teeth then did the same with the treated bars. We can run 4 times as many parts on the broach and have less wear than an untreated broach. With the cost per broach it is a major cost savings.