by Douglas Graham
Today’s Machining World Archives October 2010 Volume 06 Issue 08
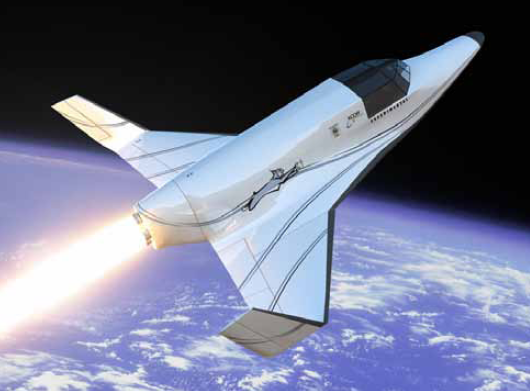
Space is no place for life as we know it, but it may be the ideal manufacturing environment. In near zero gravity, materials with incompatible properties can be mixed to create alloys nonexistent on Earth. The sterility of space also makes it perfectly suitable for semiconductor, nonlinear optic and photonic production.
The Space Race
Any American alive mid-century remembers the Space Race—that parenthesis in time between the broken postwar world and a new far better one most believed was just around the corner. U.S. popular culture of the late 1950s and early 1960s was so space-oriented, a person magically transported to that time from an earlier one might have thought people were already living and working among the stars. In our imaginations we were doing just that, we brave pioneers were homesteading the Great Beyond.
Television was Space Age iconic (“Lost in Space,” “Space Ghost,” “The Jetsons”). Then there was “Googie,” a futurist architectural style that celebrated the soon-to-dawn, “Rocket Summer.” Christened after an eccentrically designed Southern California coffee shop, the Googie style flaunted up-swept roofs, weird angles, shiny metal surfaces, and saucer shapes reminiscent of UFOs. It survives in a thousand abandoned restaurants and gas stations rotting along the Route 66’s of America.
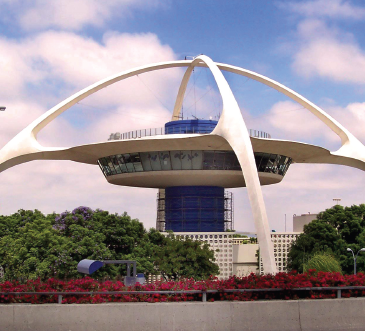
“A real Space Age couldn’t have happened in the Cold War era,” says Jeff Greason, CEO, XCOR Aerospace Inc., a California-based developer of reusable rocket vehicles and the systems that go into them. “The period was mired in propaganda. We had to show the Russians that we could beat them to the Moon, and the Russians had the same objective where we were concerned. Not considered to any great extent was the question of what might be done with the Moon once humans were tramping around on its surface.”
Turning Practical
Today we’re thinking out of the rocket about space and are looking for practical uses for it. Off-world manufacturing ranks high on the roster, as it could possibly solve problems related to material availability and workability, and the negative impact of industrialism on the earth’s environment.
Environmental factors were non-issues early in the Space Age. While there were some murmurings about the long-term effects of unbridled industrial development on the Earth’s ecosystems, they were largely dismissed as gibberish from fringe-dwelling eggheads. “There was no resource supply problem back then. As the Free World’s leading player, the U.S. easily extended its influence to mineral and oil-rich regions throughout the world, except for those controlled by the Soviet Union and China.” In fact, it could be argued that the Soviet problem was the only problem vexing happy America in those days—at least the only problem many Americans seemed willing to acknowledge.
Everything changed when Mother Russia launched Sputnik 1 in 1957, rising in the collective U.S. awareness of the frightening threat of a Russian nuclear strike from above the stratosphere. It was Nikita Khrushchev, not Dwight D. Eisenhower, who launched the Space Race, and it took America several years to catch up. That period waned after the Apollo 10 astronauts left their footprints on the moon. Googie succumbed not long after.
Troubleshooting
Now we’re headed back to the Cosmos—this time for more practical reasons than the real or imaginary threat of Soviet military adventurism in space. The Moon, in particular, offers an almost limitless cache of natural assets—including minerals, ores and other natural assets amenable to manufacturing. Moon dust can even be used to make silicon chips. A space-based, solar array could potentially provide a lot of our planet’s energy needs.
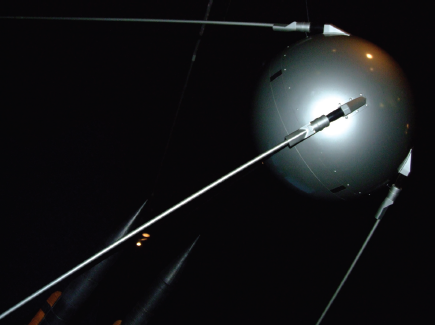
The list of compelling reasons to go to the moon and stay is long. It’s a mineral repository with an abundance of calcium, titanium, iron and magnesium. It’s also a source of oxygen, and possibly hydrogen and helium-3 (He-3). Processing will be required to extract such elements from the compounds in which they are imprisoned, but once accomplished it could lead the construction of an off world mining or mineral processing facility. Moon-based processing could benefit the earth’s ecosystems, but pollution of the lunar surface would be a real problem. The release of processing gasses would compromise the moon’s most attractive industrial asset—its perfect vacuum. For this reason, the majority of processing/industrial activity based on the Moon would need to be done in enclosed facilities.
A pertinent issue never seriously addressed by the decision-makers of the Space Race is how to economically transport the materials required constructing and supporting space-based manufacturing centers. “At the moment, getting people and objects off-planet is preposterously expensive,” says Dr. Lee Valentine, executive vice president, Space Studies Institute, an organization that develops technology for space exploration and economic development, in Mojave, Calif. “Transport cost is the real reason we’re still earthbound. It’s been the single biggest roadblock to arriving at the future that preteen-Baby Boomers read about in comic books. Once we push that stone out of the way, you’ll see a transition much bigger than the one that followed the invention of the Internet—a sea change with the power to permanently and positively affect the way we live.”
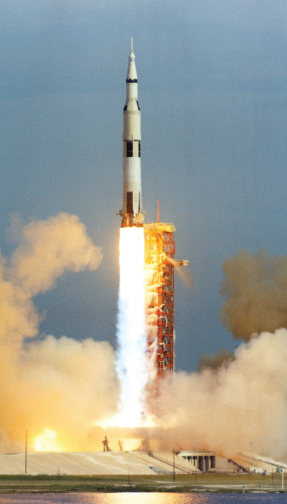
Right now it costs roughly $20,000 per pound to get stuff into space, a sum not solely attributable to the weight of materials transported. Spacecraft are not reused, nor are missions deployed often enough to be cost effective. In fact, the throwaway nature of space vehicles is probably the single biggest cost-builder in transport. Materials launched into space at the moment include everything currently hauled by truck, jet, car or train, including water, oxygen, electronics, metal, plastics and people.
While the high price tag is largely attributable to the current state of aerospace technology, it’s also an effect of ownership. With the exception of the Boeing Delta IV and the Boeing-Lockheed Martin joint venture, United Launch Alliance Atlas V (both traditional Apollo-style, expendable launch vehicles), most American spacecraft are federal property. The lack of private competition, coupled with notorious government management problems have helped keep the price of off-world material transport uneconomic.
Then there’s the matter of scheduling. The Space Shuttle has run launches about seven times annually, a reality embarrassingly short of the weekly goal originally set by NASA. The agency also hopes at some future time to push down the per-pound price of material transport off-world to a mere hundred bucks, an objective that seems out of reach at the moment.
Real Possibilities
Despite the obstacles, baby steps in the direction of off-world manufacturing were recently achieved. Back in the 1990s, a U.S. space shuttle placed a 2,000-pound disk on a 12-foot diameter platform that robotically produced thin, film crystalline semiconductors in low orbit around the Earth. This Wake Shield facility produced chips that were beyond top quality because they had been created in the airless vault of space.
“Space is hundreds of times better for creating semiconductors, solar cells, coatings and thin films because there are far fewer impurities up there than in the best clean rooms on Earth,” says Dr. Alex Ignatiev, director, Center for Advanced Materials, University of Houston. Although the Wakeshield facility was launched as an eight or nine year program only three flights were put into orbit, all funded to the tune of about $35 million by the Space Vacuum-Epitaxy Center (SVEC), a NASA commercial space center hosted by the University of Houston, as well as private investors.
The major obstacle encountered in the project was cleanliness, as vacuum contamination would neutralize the whole project. The Shield had to be transported from Houston to Cape Canaveral, and along the way it was at constant risk of contamination. The cleanliness issue was not resolved in space. The Shuttle was dirty, so the Shield had to be distanced from it in order for its manufacturing vacuum to not be compromised.
The long-term goal was to produce 1,000 semiconductors per month, but the 2003 Space Shuttle Columbia disaster put the brakes on the project. The Wake Shield project did achieve its objective by producing the highest quality aluminum gallium arsenide semiconducting thin films created to that date.
The project is still running but in a different configuration. SVEC is now working with the Russian Academy of Sciences on a project currently known as “The Shield Program.” The goal is to place the Shield on permanent duty on the International Space Station. The Russians have fully-funded the program. NASA funds have yet to materialize.
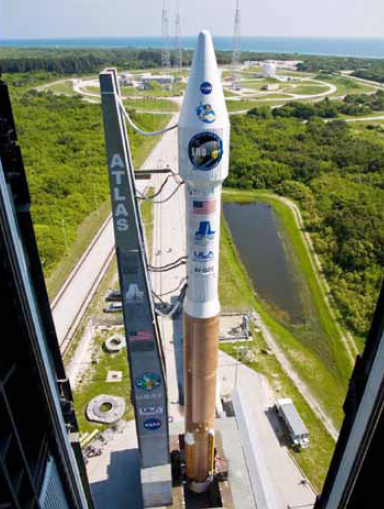
More Possibilities
The advantages of manufacturing and machining in space could far outweigh the challenges. You could, for example, build up parts by vapor deposition. Such a process might begin by heating an aluminum ingot in a solar furnace to the point of vaporization. Condensing the vapor on a mold will make it possible to form complex parts and/or very large structures such as mirrors or girders with highly uniform metallurgical properties. Lunar microgravity facilitates the build-up of super-sized constructions, and because the moon’s oxygen-free environment comes with no threat of oxidation, they could be silvered with high-reflectivity aluminum.
The lunar surface itself presents a range of manufacturing opportunities. Fibrous glass can be drawn from moon dust with heat, and used to make glass or ceramic reinforcing fibers. The material would prove exceptionally high grade since there is no water on the moon to dilute its properties. Welding too would work well in space, especially on materials like titanium, which in a conventional shop scenario quickly develop surface oxide. Welding in space is not only feasible. It’s fact. Experiments using electron beam welding were successfully conducted on Skylab, and when manufacturing in space is a reality it will likely be the preferred method.
What other manufacturing applications might be done “up there”? According to Ignatiev, space offers the opportunity to create defect-free, high performance products using elements available off-world. Solar cells, for example, can be produced using moon dust collected and processed by a solar powered robotic vehicle. No vacuum chambers are required to pull this off. The lunar surface is the ultimate clean room. The materials required to build manufacturing centers can also be harvested right on the Moon, and because it has icecaps, the moon can provide the hydrogen and oxygen needed to support human habitation.
The two components needed to make solar cells are silicon and aluminum, and both can be extracted from lunar dust. Using solar heat, the dust can be melted into glass upon which thin film silicon cells can be “grown,” and aluminum can be formed into a wire mesh to tie them together. No vacuum environment would be required to create the cells, as the moon is a planet-sized vacuum chamber.
According to Ignatiev, lab experiments have demonstrated this technique using solar-powered robotic vehicles that function as mobile manufacturing centers. Once deployed on the moon, the robots would move over the lunar surface, melting moon dust into glass and aluminum and forming networks of solar cells as they go. With this self-perpetuating process, a solar network sufficient of supporting a lunar base could be built over five years at a total cost of $250 million. The staggering sum needed to transport the components of the same solar network from Earth falls somewhere on the plus side of $3 billion.

If the necessities for sustaining life were met, a manufacturing infrastructure could be constructed on the lunar surface or an artificial biosphere in orbit around Earth, upon which any machining task done down here could conceivably be duplicated.
“A machine shop on the Moon or in orbit would very likely be a short sleeve, pressurized environment reminiscent of a typical job shop,” Valentine explains. “Lunar dust is a nasty abrasive, so you’d need safeguards in place to keep it out. Artificial gravity would be an absolute necessity as well. But the advantages of manufacturing and machining in space could outweigh the challenges. You could, for example, heat a metal like aluminum in a solar furnace until it gets so hot it vaporizes. The vapor could then be condensed on a mold and used to form complex parts or very large structures with uniform metallurgical properties.”
A Glimpse at the Future
The journey that will end with space-based manufacturing is poised to take a giant step forward. New aerospace technologies and a philosophical approach to space travel more in tune with the attitude of the 21st Century will soon overcome the launch cost issue. Several private companies are hard at work designing and building winged reusable space vehicles that run on common liquid fuels. At least one, The XCOR Aerospace suborbital vehicle, Lynx, is scheduled to be airborne for commercial and engineering research applications within the next two years. Airplane-like vehicles are a practical alternative to a conventional spacecraft because they can take off from the ground, land on an airstrip, and be used over and over again. The Lynx’s ignition system also activates and deactivates as easily as any automobile—no big blast required.
A reusable spacecraft is a major departure from business as usual. Conventional space vehicles shed pieces of themselves in flight, and trash their engines via the use of solid or hybrid fuels that neutralize motor casings. Old school spacecraft are disposable, which from the perspective of cost-effectiveness is no different than dumping every Jumbo Jet that rolls off the assembly line upon completion of its maiden voyage. “Performance trumped everything in the first Space Age, and to a great extent, still does,” observes XCOR Aerospace Media Imaging and Graphics Director, Mike Massee. “It’s the sledgehammer approach, and it’s economically problematic. Solid fuels burn up engines, and the use of toxic propellants like hydrazine make everything even more expensive because of the costs associated with hazardous materials training, testing, handling and storage. Hydrazine is used today. That’s why a shuttle landing zone looks like a HAZMAT site.”
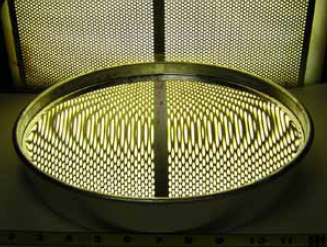
When sustainability is achieved, the real Space Age will begin. Launch prices will drop as off-world travel is privatized and more consumers opt for suborbital flight over old fashioned jet travel. Then the orbital market will open up, and the time and money investments made by people with a stake in the future will finally pay out. When will that golden age dawn? According to some aeronautic experts, the bright and shiny world foreshadowed by Googie could be fact much sooner than anticipated by even the most starry-eyed, Sixties optimist.
“Humans and industries will begin homesteading space in about 15 years,” Valentine predicts. “Off-world manufacturing and power generation will be routine a decade after that, just like the Internet is now. Ten years ago, most people were still thinking of the Web as a way to buy dog food without leaving the house. Now it’s a utility—that’s the way the future works. Every major scientific development through history was thought wildly improbable until it became a component of our daily lives. Space travel, space-living and space-based manufacturing will be the same, and for our grandchildren, a fact of life taken totally for granted.”
1 Comment
The key to economical development of space is capturing asteroids and putting them into orbit preferably around the earth and moon they can be used as housing, and a cargo vessels. A 20 year program could accomplish this by using a fleet of robtic drills to tehter themselves to asteroids and place fissionable material into the holes to heat the rock and create outgasing. The outgases could be capped. Using a variable angle nozzle the propellant could first stop the rotATIoN in three axeses and then to propel the asteroid on a desireable copurse. During the initial capturing process other projects could identify suitable materials to capture. We don’t need to lift factories into space if we use the resources we collect. One such astroid 1 1/2 km long and 1 km around contains 200,000 ton of gold and platinum (more than has been mined on earth and various rare minerals to last 250 years at current production levels. Once the astroid is captured the minerals can be sold as stock, like any mine on earth, and create a financial instrument worth 25 Trillion dollars in today’s market. Once again the idea is to keep it simple and be patient.