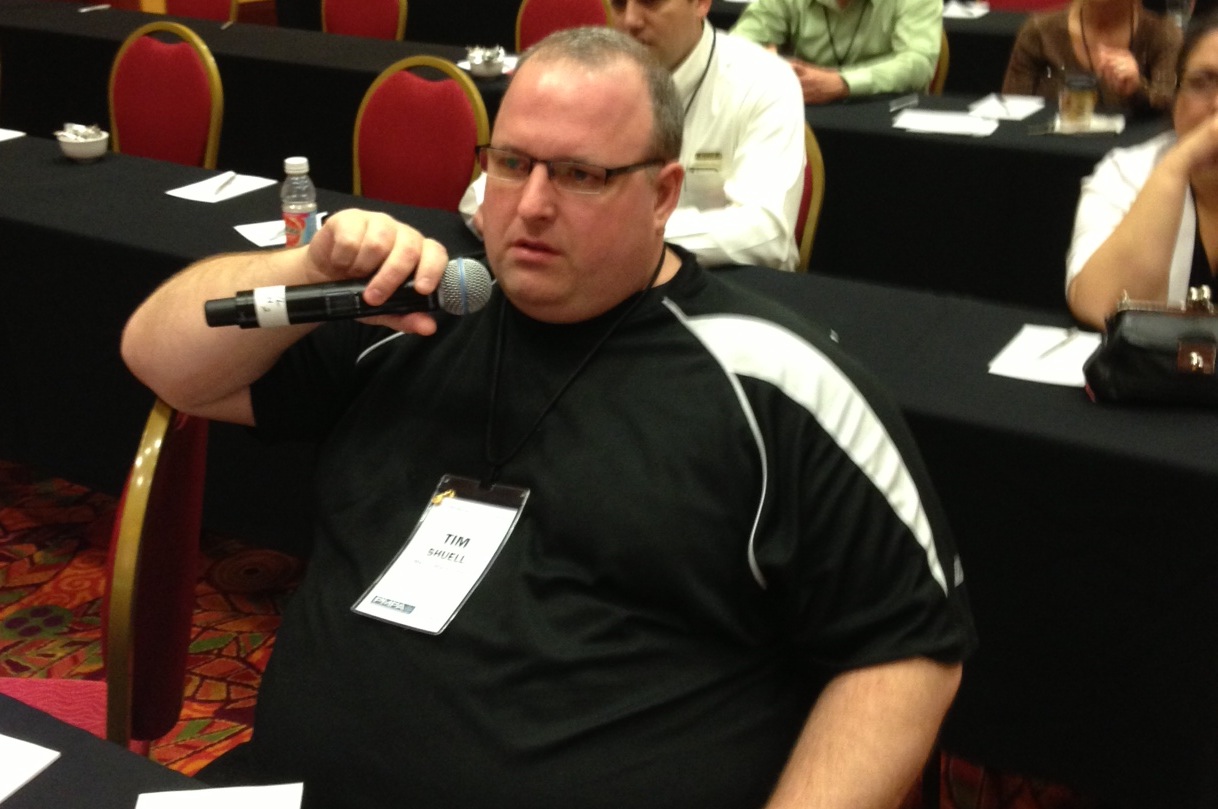
Two weeks ago, I attended the Precision Machined Products Association (PMPA) Management Update, a three day annual conference where around 200 representatives from manufacturing companies in the association gathered in Arizona to network and go to lectures on the economy and business management. It was a great place to bond with my machining industry peers, find some leads and get a scoop for a blog.
I almost always come away from PMPA events with a warm feeling from seeing how much the members genuinely care about their industry and each other. As usual, one of the main issues on the minds of attendees was the challenge of finding young people to sustain the U.S. manufacturing industry, both on the factory floor and on a management level as well.
At dinner on the first night of the conference, Jerry Eighmy, owner of American Turned Products and a former PMPA president in his 60s, told me I should write about the need for more young people in the manufacturing industry. People tell me this all the time, Today’s Machining World has discussed the topic for years. But it’s a huge issue and very worth discussing again, so I will.
The vast majority of people at the Management Update were were mid-40s and up. That seems logical as the conference is for managers and owners, who naturally have had to pay their dues over time. But still, I’m willing to bet that the same 50- or 60-year-olds on the 2013 PMPA board were attending PMPA meetings 20 years ago.
Walking to the hotel bar the first evening of the conference, I ran into Tim Shuell of Metric Machining (Ontario, California), a very sharp outspoken 39-year-old manager/engineer. He almost immediately began our conversation by confronting me about a feature article I had written for Today’s Machining World in 2011, in which I had interviewed him at the Management Update of that year. He complained that article contained some quotes from him taken out of context. I apologized about the article, and then he told me that I should start blogging more, rather than my father Lloyd writing so much, because we needed to relate better to the younger generation in the machining industry. Although he’s a fan of my father’s writing, Tim said my dad’s blogs were sometimes “too 1950s for him.” Whether I agreed with that or not, I appreciated his confidence in me and his passion for the machining industry. I quickly whipped out my iPhone to record him as he continued to speak his mind. “We (manufacturers) do [stuff] that people can’t do,” he proclaimed. “We make stuff people can’t make. This is the core of everything people hold in their pockets, that they drive on the road, that they put in their house. We make this stuff … there’s something visceral about making these parts. You can’t deny that.”
On the plane home from the conference I got to know David Knuepfer Jr. and his younger brother Bill from Dupage Machine Products, a large shop near Chicago with New Britains, INDEX multi-spindles and Euroturns, among other equipment. Dave Jr. and Bill, ages 30 and 24 respectively, are fourth generation at the company and came to the update without their father, the company owner, David Sr., a past PMPA president. I’m pretty sure they were the only two people at the conference younger than me, which was refreshing — I think. Dave Jr. told me about his experiences working at INDEX in Germany for two months, giving me some interesting insight into the way the Germans approach engineering and business. I had a particular interest in the topic because Graff-Pinkert sold two INDEX MS machines in the past two months. The INDEX MS machines seem to have emerged as the crème de la crème of CNC Multi-spindles worldwide. Dave Jr.’s younger brother Bill talked with me about Dupage’s experiences looking for new employees. He told me about the company’s use of careerbuilder.com and lamented that a great number of applicants “juiced” their resumés. The company’s longest tenured employee brought in from careerbuilder.com lasted nine months.
I was impressed with both brothers’ grasp of their company’s business. It sounds to me like they will successfully carry on their company’s legacy. They represent the future generation of leaders in the U.S. manufacturing business. But what about the children of the other 100 or so owners who came to the conference? Who will succeed them?
Questions: Would you be able to work well with a sibling in a business?
Would you able to work well with your spouse?
8 Comments
Good day Noah,
I bought several Index SM from you and some from other places and remember my Dad had Brown & Sharps but I liked the Index. After I bought one of the first CNC B&S, I really wanted a CNC Index…but was really expensive. The 8 holes and single point threading was fantastic and the consistent Index ultra-precison was always appreciated. I can certainly understand now and then “crem-de-la-crem”.
Younger machinists are tough to get because all the US “academia” wants to do is teach college. Mechanical skills are dwindling to almost nothing except from foreign born people. Too bad…and another reason I left the machine shop business but loved the people from all over the world in the association-with the Management Update my favorite!!!
I own Grovtec US, Inc. and we have Davenports, Acmes, Brown & Sharps, CNC machines, Rotory transfers, and multiple Secondary Operation machines. I have been in business since 2006 and have the following family members as part of my team. My wife is the Operations Manager, one son is my Quality Manager, another son is my Davenport Manager, my Nephew is our Machine Shop Supervisor, my daughter in-law is my work ticket planner, another nephew is our Material Handler. Though not easy we have developed a great working relationship and try to leave work at work and not focus on it during family functions. We have 70 total employees and I am developing my family members to take over the business in the future!
My family is extremely dedicated to our success and want the company to continue to grow and be a part in the process. I have heard that this much family in a company can be a distraction and cause issues but our relationship continues to prosper.
Bob
I can answer both your questions… Working with your wife takes a great amount of Patience and understanding. It’s even better if that is not just one sided. I’m not going to say it’s been all roses, but I also don’t have to worry about a stranger robbing me blind. As long as both of you can keep your work arguments at work, it’s not so bad.
Now, working with a sibling is an entirely different set of problems. I have a dear sister I have fired several times. I could write a book!!! No one can aggravate you faster than a sibling.
Everybody has there preference. There is not a chance in (you know what) that my wife and I could work together.
I currently work with 2 of my 5 siblings in a second generation business. Interestingly enough we all run different divisions and we respect each others strengths along with, know each others weakness(s). We were taught at a very young age, don’t kill the golden goose. Always reinvest in your business.
Lastly, no matter where you are in this great country, Good help is hard to find.
We’ve hosted a series of Dream It! Do It! events sponsored by the folks at NAM. Their Manufacturing Institute is pushing the cause to find young people, and we’re trying to do our part, even though the vast number of students who see our shop will probably never work here. The exposure is important, as most youth who start the day saying they’re going to grow up to be a [service industry job here], end up leaving saying they will consider a job in manufacturing.
Our most recent event was held simultaneously with National Engineer’s Week and is called Introduce a Girl to Engineering Day. The group (mostly girls) designed a product together and saw the challenges required to manufacture it. Overall, the results of the exit interviews were about the same. Many saw the satisfaction of manufacturing a product, although more girls didn’t see themselves in manufacturing in the future.
I was fortunate to grow up and have a father and grandfathers and schools who taught me about the joys of work and manufacturing, I hope others can find time to do the same. Most of my day making rotary broaches isn’t a ‘joy’, but I’ve looked back on my career with a lot of satisfaction. I don’t think the next generation will want to run these companies without exposure to the joys of manufacturing when they are young.
I would avoid nepotism in my company at all cost. When you hire relatives, especially into management positions, the best employees will avoid your company. Smart people know that they cannot compete with relatives no matter what skills they have.
You can’t pick your relatives but you should be able to pick your business partners.
I was co-owner to be of a business being sold to we three siblings by Dad. I worked great with the one with opposite strengths….could NOT work with the one “just like me”. I left, they carried on ,and the second generation business of 40 years keeps going with out me…..no one is indispensable. The sister “just like me”…now my biggest ally. Go figure.
I’m the third generation in the industry. My wife has worked with me for most of the last 35 years (with some time off for kids). My thirty year old daughter joined us a year ago, and our youngest son has worked in the business part time for 4 years. We have cousins, sisters, and their kids in the industry. It is a delicate balance but, it can work as long as everyone has the same goal.