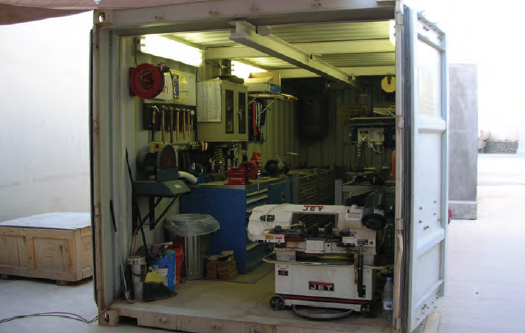
Let’s face it, once you’ve drilled a hole, it’s pretty much the same, no matter what the finished product is,” says 42-year-old Kevin Green, who counts his years operating all manner of machine tools by noting the age of his eldest daughter, who’s now 22. “It’s the working environment that I never imagined in my wildest dreams.
At Camp Arifjan in Kuwait, outside his windowless, “aggressively air conditioned” Mobile Parts Hospital workspace, the temperature one day reached 150 degrees Fahrenheit. Sandstorms often blocked out the sun. It rained once during his fi rst three-month stay, during which he lived in a “tent city” with the soldiers. In Afghanistan, a later generation of MPH offered a small window, but more restrictions outside. Green didn’t dare stretch his legs with a bit of a walk around Bagram Air Force Base. Sited on a former Russian encampment, the base remains rife with active mines. He had little time for relaxation, anyway. In Afghanistan Green worked seven days a week – four months without a day off. But if the work environments were harsh, his long hours could not have been more rewarding.
“I’m very passionate about this project,” he said recently, back at his desk in Detroit, where he’s a production support engineer at Focus: Hope Manufacturing, which provides stateside backup for the Army’s current trio of overseas Mobile Parts Hospitals. Green helped prototype the MPH module and eagerly signed on to help see the concept become reality, becoming the first hands-on operator in October 2003 of the maiden unit deployed in Kuwait. He returned to Kuwait in May 2004 for a second three-month stint, this time as site coordinator, overseeing the machining work instead of manning its versatile Mazak multi-tasking turning center.
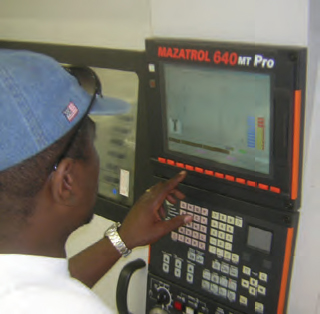
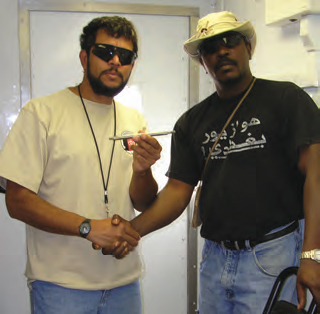
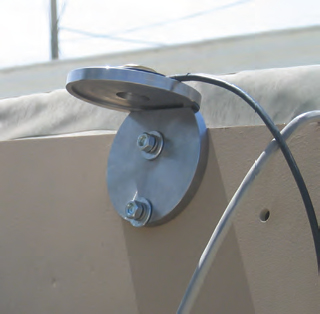
While most of the jobs soon settled into the MPH’s intended bread and butter workload – manufacturing replacement parts for military vehicles – Green soon found himself undertaking or supervising two other kinds of tasks. The first: creating special tooling, for instance, a wrench to remove a special kind of nut. The second: addressing the less specific but no less urgent requirements of the soldiers who knocked on the door of the Mobile Parts Hospital. One such sergeant’s request, for an improved mounting system to attach his Squad Assault Weapon to his Humvee (which opened our original story in the January 2004 issue of TMW), was designed and manufactured within five hours and attached to the sergeant’s vehicle before he returned to duty in Iraq the following day. The mount, Green proudly announces today, worked so well that the Army named it one of its top 10 inventions of the year.
“We took something the military didn’t have enough of in its system, made it better, and have since manufactured hundreds of something the Army deemed was saving American lives,” says Green, explaining the distinct satisfaction of creating parts on demand with the MPH. “Let’s put it this way. I’ve been a manufacturing professional for a long time. I’ve made a lot of different stuff. But to actually build something and deliver it to the person who’s going to use it, and knowing sometimes that your part may very well save that person’s life, is a whole different matter than turning out fl ywheels for some diesel engine.”
“A lot of the problems we solve create a kind of domino effect,” Green adds, explaining how key fixes can often trigger sweeping improvements. With a growing backlog of trucks to repair, the maintenance facility at Camp Arifjan needed to work round the clock, but couldn’t, because too many of its telescoping lights were broken. “How many more vehicles were they able to fi x because of the nine pulleys we made for the lights?”
Early in 2005, Green was asked to head a training program aimed at easing the transition to an early goal of the Mobile Parts Hospital initiative, staffi ng the units with military and government personnel. Two soldiers and two Department of Defense civilians spent eight weeks with Green at Focus: Hope. The two soldiers accompanied Green to Afghanistan in late June to man the MPH unit that had just arrived at Bagram Air Force Base, four months after a second MPH module set up shop in Iraq. Though both machinists, the soldiers faced a steep learning curve. “The Army doesn’t have the equivalent of the technology in the MPH,” Green explains. “We equate it to one guy knows how to fl y a kite and the other guy knows how to fly the Space Shuttle. We’re calling them both pilots because they both can fly.”
This helps explain Green’s 12-hour days and 7-day workweeks in Afghanistan. But only in part. “Once the soldiers and receiving units see the capabilities of the MPH system, we’re busy all the time,” he says. “That’s been true of all three locations.” To date, even with two of the units powering up only last year, Green estimates total production “approaching 20,00 parts delivered to soldiers, probably 250 to 300 different parts, ranging in size from an eraser to a basketball.
“The mission hasn’t changed,” Green continues. “Design a mobile manufacturing center that could make replacement parts for military vehicles at or near the point of need.” That’s been accomplished, if not yet with military personnel manning the units. Now a secondary calling has arisen: trouble-shooting parts that don’t yet exist, like creating a Humvee weapons mounting system.
Many jobs start with an outstretched hand, as did one last summer in Afghanistan. “We have to get these antennas mounted on that truck,” announced a sergeant one morning, pointing over his shoulder. “Let’s take a look,” said Green, reaching for the antennas and conducting an on the spot “manufacturing review meeting” with one of his military trainees. “We’ll have you something after lunch,” promised Green. And they did, producing in a matter of hours, a single bracket that fit three different antennas, effectively rescuing otherwise inoperative new communications equipment that arrived minus a means of attaching them to a military Humvee. Some 1,200 have by now been manufactured and pressed into service. About six-dozen of them were made in Afghanistan; the rest in the Agile Manufacturing Cell at Focus: Hope in Detroit.
Though Green says there are currently no additional MPH units under construction, he expects more will be brought into service – and not just in support of our troops. “It’s a successful program for the military,” he says, “but I also think the technology will expand into other fields. The same type of technology that we use to reverse engineer a vehicle part could be used to make prosthetic devices, hip replacements, things like that in the basement of a hospital. I could envision an MPH unit at a Nascar track making parts for racecars on site and on demand. I could envision NASA having a Mobile Parts Hospital, maybe even on the Space Station. I could see taking a unit to some third world country and doing some nation building.”
Like the parts it so rapidly manufactures, the potential uses for the MPH may be almost limitless.
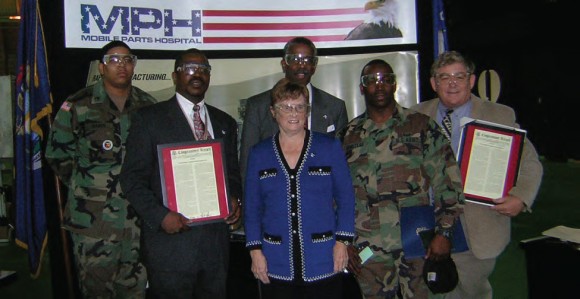