By Lloyd Graff
Today’s Machining World January 2007 Volume 1 Number 1
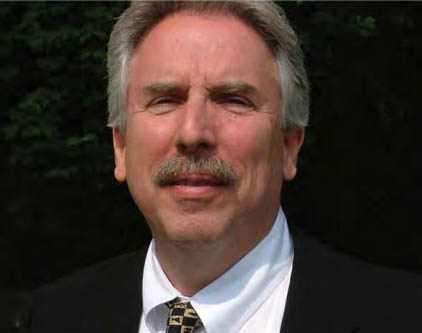
LG: I am with Miles Free of the PMPA, and we are talking about the unleaded world of materials. Is lead to steel as trans fat is to food?
MF: It seems to be; although I don’t know what benefit trans fat gives to food. We can certainly document the energy savings that lead gives to steel for machining, let alone brass and aluminum. The state religion seems to be “lead is bad.”
Where did this come from?
It comes from the European Union’s belief in the precautionary principle on lead. It’s kind of disturbing. The EU says when an activity raises threat to human health or the environment, precautionary measures should be taken even if some of the cause and effect relationships are not fully established scientifically. To me this is really a state of faith that any suspicion of any threat to the environment really trumps the lack of scientific evidence that the threat really exists. They’ve turned the burden of proof upside down and said, “Prove absolutely that your product is harmless.”
It sounds like global warming.
Very much so.
So what is the underlying scientific hunch about lead?
I don’t know in terms of what its proposed mechanism for environmental or personal harm is in machined parts. Lead was a real problem from tail pipe emissions, but that lead was reduced 96 percent with unleaded gas. Lead got its face on a reward poster that it’s a bad actor. I don’t know how many children in Europe are expected to ingest screw machine parts. I don’t know how many cars have to end up in an acid bog to raise the net level of lead. I don’t get it.
But we’re living in the real world where a bureaucratic decision in Brussels affects almost everybody in the machined parts world.
It does because it affects our industry. It affects our costs, our choice of materials and processes, and it can affect the life of service that our parts are going to have.
Let’s say you have a shop in Detroit and you’re making a part that goes into both American, European and Japanese cars, some of which are sold in Spain, and your client mandates that the parts must be made from materials with no lead. What do you do?
Well this is round one of Don Quixote’s adventure because the European regulations don’t actually say, “No lead.” There’s a couple of regulations that apply. The “End of Life Vehicles” directive would apply to your example. End of Life Vehicles specifically exempts lead up to 0.35 maximum weight as a percent for steel. It doesn’t ban lead.
So does a fellow at the end of the food chain in Detroit have any recourse if he is making a component that goes into a transmission that may be sold in Spain, and the buyer tells him “no lead”?
What’s really going to happen is the automaker is going to send a document demanding that the part maker certify that his part is compliant. The irony of that is the automaker, the OEM, says, “Make this part out of Grade A,” and now they’re demanding that the part manufacturer certify that Grade A actually meets the requirement. In many cases the customer has no idea what the heck he specified. So the shop owner in Detroit literally has to be more of an expert about this than his customer. That’s what we’ve helped do at PMPA. We’ve outlined the requirements and the exemptions and prepared some suggested wording so that when one of these “thou shall comply” letters come in you can answer it with diligence that protects your ability to still make the part.
In the real world, what does it mean?
In the real world, if it’s a 12L14 part, the machining guy says, “It’s exempt by the End of Life Vehicle standard in the annex per Article 4.2” and he continues to make it out of 12L14. Despite the fact that they banned lead, they’ve made a big exemption for leaded steel.
So you’re saying that the EU directive has a big hole in it as far as steel is concerned. What about aluminum?
It’s the same thing. For the “End of Life” Vehicle standard the original wording exempted aluminum for machining purposes allowing lead content up to 2 percent by weight. That expired in July of 2005; then it had an aluminum for machining purposes exemption with lead content up to 1 percent by weight that is supposed to expire July 1, 2008. I just received a brochure from Alcoa Global, and they’re saying that the requirement for the exemption is 1.5 percent until 2008. So aluminum with lead is okay too.
But there are some companies taking the no transfat approach and getting more aggressive on the elimination of lead.
Absolutely. It makes them feel good to do that. But they aren’t helping their company in terms of competitive pricing, and there’s really no science that says they’ve done the environment any good. Show me the benefit of that approach other than making you feel good. It’s kind of like the minimum wage. You can vote the minimum wage up all you want but at some point an employer
decides whether or not you’re worth it. So these guys are ignoring the benefit that the lead in the material gives them in terms of part quality and part price.
I agree with that, but do you think the use of unleaded materials or extremely low lead materials appears to be spreading?
Yes. There are aluminum grades that have had to be modified in order to meet the EU requirements, and there are certainly a lot of people using 1215 instead of 12L14. Laurel Steel has a tin additive steel. They’ve had success with their product in some applications.
In aluminum, what other substitutes are there for lead?
The standard grades allowed up to 0.6 percent lead content, and the EU requirements of 0.4 percent (in RoHS and WEEE) made those grades not suitable for application, so some of them have been modified to reduce the lead content. 2011-T3 now has a low lead variety with .20 to .40 lead and .20 to .60 bismuth, so they’ve brought that maximum lead range down in order to comply with the European application. Alcoa has a C06N, and they’ve got .40 max lead on that.
Is there any material other than lead they’re putting into aluminum bar now?
Bismuth isn’t spelled out in the European regulations, so on a couple of the grades bismuth is in there as an adjunct to the lead.
What does the bismuth do?
It has very similar mechanical properties and physical properties to lead, so it acts much the same way in the material during machining as the lead would. Bismuth had been added to leaded steels in the past. U.S. Steel had a product called Mach 5 with a lead and bismuth combination, and Inland had their INCUT ™ series that featured bismuth instead of lead. Aluminum is showing
this bismuth addition as well.
Does brass have lead in it?
In their wisdom, the people in Europe have said that brass can have up to 4 percent lead and be exempt from the “End of Life Vehicle” requirement, but aluminum can have no more than 0.4 percent. So apparently little children in Europe can safely ingest lead out of brass at a level ten times that of aluminum.
Can you make brass without lead?
You can make brass without lead. Chase Brass has a leadfree brass called Eco Brass™. They substitute some other elements for lead to get machinability. But like every new technology there’s an implementation ramp up. You cannot mix the non-leaded brass with the leaded brass scrap, so you need to maintain a separate system for handling nonleaded brass. The elements that make it free machining in that incarnation actually work against it if it gets into the traditional leaded scrap stream – and that’s where the bulk of the market is.
Let’s talk about approaches to cutting unleaded materials. I have been told by clients that it is messier– much more difficult to machine.
Well, if you were to change from leaded steel, 12L14, to unleaded – say 1215, we’d really want to look at what’s going on. First off, your readers are all going to have a different definition of what machinability is.
What is your definition?
My definition is the ability of material to travel through theshop starting as bars, ending as parts and causing the least amount of aggravation and trouble for the machine and the machine operator.
Now, the shop’s purchasing agent doesn’t really care – he just wants the lowest price. Meet the spec and those guys in the shop can worry about it. We’re going to work on the machinist definition. But first, we need to say one thing about hardness. A lot of people are careless in the way they use the term hardness. They’ll say, “Unleaded is harder to machine” or “This is hard to cut.” As a technical person, my definition of hardness is “resistance to indentation.” It’s resistance to penetration. Hardness is not a synonym for difficult. Hardness is not the difference between the machinability. The hardness of grade 1215 is 167 Brinell.
The hardness of 12L14 is 163 Brinell. Trivial difference. What we need to look at is what the lead actually does, which is to allow the material to be run at higher speeds. I’ve got an old Monarch manual Feeds and Speeds for Better Turning and here’s a quote from it: “Cutting speeds can normally be increased from 15 percent to 25 percent above those employed for turning a non-leaded grade.”
Lead boosts machinability about 25 percent at low cost. So if we take out the lead what does that do to the material? To eliminate lead means we need to change our setup to reduce the speed since the lead is acting as a lubricant, allowing the material to be cut at a faster surface footage. Taking that out means we’re no longer cutting up forgiving material. So if we’re going to go to a non-leaded 1215 material or a non-leaded equivalent, we’re going to reduce the speed. Make up the volume removal by increasing the feed.
Speed equals heat, and heat is bad. Cycle times have been improved by lead because lead allows you to run at a higher speed. It lubricates. It melts at around 648 celsius. It has a low melting point, so during the cut it creates a liquid phase that can act as a lubricant in place. It reduces friction, pulls a little heat out by melting, and there is a theory that it helps to create the next chip by a process called liquid metal embrittlement. It really is doing a lot of work to make the material machinable by the machinist’s definition. Mostly it’s acting as an internal lubricant, reducing friction. The coping strategy to move from 12L14 to 1215 is to reduce the speed, so let’s increase the feeds. The result would be to have similar cubic inches of removal and less heat.
Can you also compensate with different coolants?
You can do that by applying high pressure/high volume coolants. There are a lot of strategies you can use to help make that change. But I’m limiting my comments to what I’m going to do without adding new technology. The tool wear is going to change. 12L14 would have a lower rate of tool wear than 1215 would. So if I’m a guy in the shop, I’m going to look at the way I’ve tooled my job up and say, “Well maybe I should use easier to replace tooling, maybe I need to get a higher grade of tool or a tool with improved coating to keep me even with where I was before.”
One of the unintended consequences of the move to unleaded steel is that people are going to switch tooling. It might actually be a boon for some of the cutting tool manufacturers who devise a better mousetrap.
It may require that. If somebody’s operating in the middle of the range on 12L14, maybe they won’t notice much of a difference. But if somebody’s a sharp operator they may need to upgrade tooling, coatings, maybe change geometry to increase the rate that they’re cutting. Screw machine parts are priced based on uptime per day as well as cycle time. Taking the lead out we’re saying, “We’re going to increase downtime per day.” The other consequence of taking the lead out is that the new work is going to be operating at a higher cutting temperature. This is where your point about improving the coolant or improving the coolant delivery comes into play.
Who do you think the winners are going to be in the move to unleaded steel?
I think the people who understand the true economics and understand the true requirements and are able to see through this “feel good, lead is bad” strategy are going to be able to run their equipment at their equipment’s best, using a grade that’s acceptable to the EU requirements. The guy who just slavishly obeys and says, “Okay, I’m going to try and make it out of 1215 because you don’t want lead,” won’t be competitive, and his compliance won’t gain him anything necessarily. So the buyer and the component maker need to have the dialogue. That’s why the PMPA prepared a Business Intelligence Report on the subject, so that people can say, “Look, is this a real need or is this just somebody’s interpretation?” when in fact the Annex to the directive says, “I’m allowed to use lead in these normally expected levels.”
So strategy one is to analyze the process and appeal the material.
I never say denial is a good first step, but in the case of saying that this job requires no lead, if it’s for a vehicle application, End of Life Vehicles clearly allows leaded steels, aluminums and brasses at conventionally acceptable levels. Same for RoHS (Restriction of Hazardous Substances) and WEEE (Waste Electrical and Electronic Equipment) directive. So to take somebody’s quick read that this means no lead is to really shoot yourself in your productivity because you’re not going to be as productive without lead as you will with the stuff. The EU directives allow leaded steels, aluminums and brasses at conventional or modified, but commercially available lead levels.
So some people may say, “Oh, I’m not even going to bid that job” and other people are going to say, “Uhhuh, there’s an opportunity here. Let’s delve into this a little deeper. We really want this job. Let’s figure out how we can get the competitive advantage by assessing the material issue.”
Absolutely – understanding the job. Contract review is key in everybody’s business. But to have the courage to say, “Well, Mr. Customer, you realize that this doesn’t really say that it forbids lead. It says, ‘I can use lead up 0.35 weight percent and here’s how I’m going to do it.’” That’s what the winners will say.
Thank you very much, Miles.
2 Comments
Do you have any thoughts on the California AB-1953 lead restriction? The regulation allows lead up to .25%, while 12L14 has an allowable range of up to .35% therefore not allowing use of the 12L14 unless there is selective use of heats containing under the .25% threshhold.
What is the coating adhesion difference and the heat treat difference leaded stock and unleaded bar stock?