Today’s Machining World Archive: November 2007, Vol. 3, Issue 11
Robots can perform many tasks that are done by humans, and they can keep on performing these tasks, shift after shift, without getting tired or taking a break. The type of robot commonly used for shop floor applications is the familiar “articulated robot,” which has jointed arms.
What a robot can do for you
Robots are really good at repetitive tasks. Loading and unloading parts from a machine, for instance, or deburring or polishing the same type of part over and over again. They don’t get bored or tired. They don’t get repetitive strain injuries. And, once programmed properly, they don’t make mistakes. They can take over routine tasks, and allow your skilled staff to do more demanding work.
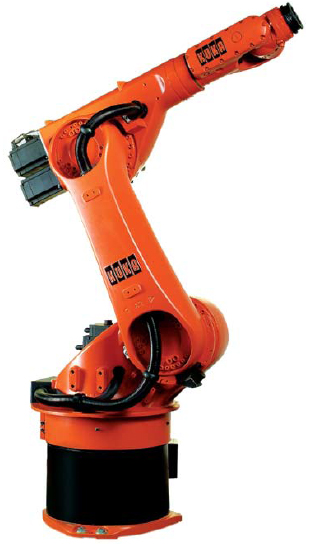
How to get started
A common first use for a robot in a machine shop is machine tending – loading and unloading parts. Where employees have to handle heavy parts, you may want to provide a robot to do the job and help prevent workers from injuring themselves.
“Typically where robots are coming into use is in material handling applications,” said Tom Rohlwing, vice president of sales, Dane Systems LLC, Stevensville, Mich., an automation systems integrator. “The most justifiable payback is on repetitive runs of like parts.”
A shop’s first robot might be something like the FANUC LR Mate. It’s about the size of a human arm and handles a payload of up to 5 kg (11 lb), said Mike Cicco, account manager, FANUC Robotics America Inc., Rochester Hills, Mich. The robot is lightweight and portable. It can be mounted on a stand with wheels or forklift pockets for easily transport.
Families of similar parts are ideal for robot load/unload. You can simply change the end-of-arm tool on the robot for each part number. Operators who can change the jaws on a chuck can also easily change the jaws on a robot’s gripper.
The pieces to be machined can be arranged in a plastic, machined pallet or tray, so they are located and oriented properly. The trays can hold different numbers of parts, 10 or 100. When you program the robot, you teach it where the first part is, and it can figure out where the rest are from the grid layout you enter. The parts don’t have to be very precisely located, only within about a quarter of an inch, said Cicco, since the robot’s gripper will automatically center the part when it grasps the part.
You’ll probably want to work with a system integrator to design and install your robot system, especially your first one. An integrator will understand and evaluate your needs, and design and build a complete robot cell for you, including robot, mounting, controller, guarding and any additional functionality you want, and then train you and members of your staff to program and operate the robot. In a job shop, you’ll want to be able to use the robot for different parts, so be sure the integrator knows the heaviest part the robot needs to handle. A number of manufacturers offer product lines of robots rated for payloads of up to 700 kg (1540 lb) and more.
Once the owner and staff understand how to use and program a robot, they can figure out how to redeploy it for another application. “It’s a pretty simple concept, and once you’ve got the concept down it’s pretty easy to apply it to something else,” said Cicco.
“As an integrator, we give them the recipe, the instructions. We can do it for them or they can do it themselves,” said Rohlwing.
Accepting automation
How do employees respond to robots coming in and taking over some of their work? “What we’ve heard people tell their employees,” said Cicco, “is it’s a growth opportunity for them; they can get trained on a new product.” Many employees respond well. And “most employees realize if the company is not profitable, everybody is out of a job,” said Cicco. To be competitive, the idea is to take the labor out of the product. The reality of the situation is that a shop may end up reducing head count by people who are not open to the new technology.
Safety
Most industrial robots don’t know when they collide with something and they can potentially do damage. For safe robot operation, workers and passersby should be protected from robots by guards, fences and interlocking doors or gates. Your system integrator should be knowledgeable about safety requirements and can provide you with the necessary guarding. Also, careful programming, and perhaps computer simulation of the robot’s path, can prevent the robot from crashing into the machining center or other obstacles.
Return on investment and payback
As with most equipment in the machining business, robots don’t come cheap. A standard machine-loading cell can cost nearly $50,000, according to a robot manufacturer interviewed at the Robotics Show in Chicago last June.
Can robots really pay for themselves? Typical payback is less than two years, Cicco said, and often is just over a year.
Cicco told about one shop owner he worked with who had gotten to the point of sometimes needing a third shift, and sometimes not. After installing two robot load/unload cells, he could set up the cells with a supply of pieces at the end of the second shift, turn the lights out and leave it to run unattended. This way, he got four additional hours on one machine and two on another, without having to put on a third shift or pay overtime. Payback for these cells was less than a year, Cicco said.
Used robots are widely available, and you may be able to keep your costs down by buying used instead of new. Make sure it is rebuilt and certified by the rebuilder. You can also ask your system integrator to find you a used unit.
More advanced uses
Once you have installed and started using one robot, it’s likely you will come up with additional robot applications. More load/unload cells, or maybe a single robot mounted on rails to service several machines. Robots these days can be fitted with sophisticated vision systems so the robot can pick up randomly oriented parts from a conveyor or bin, eliminating the need for pallets or trays for pieces to be loaded.
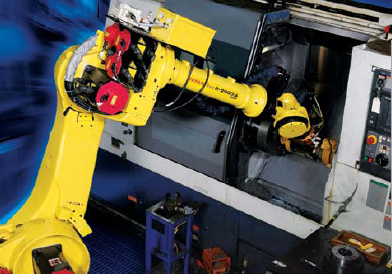
When you automate parts handling, you can add automatic inspection processes, said Rohlwing. Then, “every part you pass through the system can be a good part,” he said. While the robot is handling a part, sensors or a vision inspection unit can easily check inside and outside diameters and other dimensions, as well as the presence of features such as threads or holes. Robots can also deburr, grind and polish. Robots are also commonly used for drilling.
Robots can even do milling. Some robot, software and accessory manufacturers have formed partnerships to create systems that enable a robot to wield an end mill or other cutter. Specially designed cutting heads are available for mounting on the end of a robot arm. Software is available that translates a computer-aided manufacturing (CAM) program into robot motion to follow a contour and to do complex, 5-axis machining – without a machining center.
Most of the robot-milling systems available today are intended to cut soft materials, such as the foam or clay used for design models. Of course, a robot system lacks the rigidity and strength of a machining center, and, so far, most robot-milling systems are unable to generate the higher forces and accuracy required to cut metals to typical machining tolerances. As time goes on, however, robot manufacturers and their partners will likely develop robot mills that can take on more and more of the metal cutting tasks now performed on traditional machining centers.
Out of the shop and into the future
As robots become more capable and easier to “train,” they will be able to provide helping hands for many tasks in the shop. Check out the video on www.smerobot.com for a look at a futuristic robotic assistant.
As they increase in capabilities and ease of use, robots will move beyond the manufacturing environment and perform tasks in the service sector to improve productivity there, said professor Henrik Christensen, director of robotics and intelligent machines, Georgia Institute of Technology, Atlanta, Ga. A hospital nurse, for example, typically spends 10 to 15 percent of a shift running errands, walking up to five or six miles per day, he said. A robot could perform many of the errands, such as taking specimens to the lab. The nurse could then use that time and energy for patient care. This type of application could be available in three to five years, Christensen said.
As the large population of baby-boomers ages and needs assistance with everyday tasks, robots may be able to provide dignified, always-available assistance. Potentially robots could help a person get out of bed, get dressed and prepare a meal, Christensen said. A robot to provide this kind of in-home help might be available as soon as 10 years from now, he said.
It’s widely accepted that the only way to keep manufacturing in the U.S. is to remove the labor content of manufacturing processes. The same machine would cost about the same here as elsewhere, and energy cost may be about the same. If the only major difference is the hourly rate of the workers, and robots can cut the hours, there’s much less reason for work to go offshore.