By Noah Graff
Today’s Machining World Archives January/February 2011 Volume 7 Issue 1
Ten minutes into my interview with Jens Bogehegn and Steve Weiss, the co-founders and owners of Zacuto USA, a filmmaking accessories manufacturer in downtown Chicago, they break off on a tangent, excitedly brainstorming and debating production decisions for the upcoming season of their Emmy Award winning Web video series, The Great Camera Shootout. On the show, Jens and Steve, veterans of the film and video production industry, scientifically review every current HDDSLR camera, pitting the quality of the video footage from those cameras against the images of traditional film cameras. Both individuals are intense, driven businessmen, who take great pride in the filmmaking accessory products they build. They like being in the manufacturing business, but they will be the first to tell you that their first love is filmmaking. “If you had talked to us seven years ago and said, ‘one day you guys will be manufacturers,’ we would have laughed at you,” Steve says.
Before the Machining Business
Jens met Steve in the mid-’80s while looking for a place to do video editing. Soon after, Jens worked as a freelance cameraman almost exclusively with Steve through two former businesses. In 2000, they started a production house together called Zacuto Films and in 2001 formed Zacuto Rentals, a camera rental division of the company. In 2005, they created Zacuto USA, the manufacturing branch of their company.
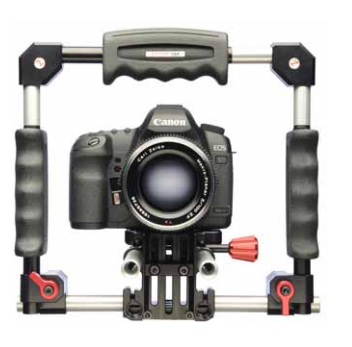
The High-def Revolution
Around 2001, High-Definition video cameras struck the professional video production world when Panasonic introduced the VariCam line. The VariCam revolutionized the filmmaking world because it could shoot in 24p (“p” stands for “frames per second”), the same frame rate as film cameras, rather than being limited to 30p, the speed which video has traditionally been shot on in the U.S. The VariCam’s images, when shot on the 24p setting, produced an image similar to that of film. This was a dream come true for filmmakers everywhere because the camera still had the ease of use and economic advantages of video cameras. Shooting film has always been extremely expensive, time consuming and labor intensive. The light sensitivity of film allows less leeway for shooting in natural light compared to some of the latest HD video cameras, so shooting it requires more extensive lighting equipment and often a crew. Also, a bargain on 35 mm film stock could be $30 for a minute of footage, while videotapes cost a tiny fraction of that. After shooting, the film has to be sent to a lab for processing, which creates more time and expense. Then, converting film footage to a digital format to edit it on a computer is a much more involved process than transferring digital footage into a computer.
If you can’t picture the difference between film and video footage, think about images from a Hollywood movie or TV show shot on film and compare them to the images from a newscast or sporting event shot on video. It’s not that 30p video looks bad, but the look of film is what many people consciously or unconsciously believe a beautiful, professional image should look like.
High-def for the Masses
Soon after the VariCams came out, Jens and Steve bought two or three of them for their rental business for about $100,000 each. The cameras were always checked out, because according to them, at the time there were only about 100 VariCams in existence worldwide. But in 2004, the video production world again was turned on its head when Panasonic came out with its prosumer High-definition camera, the HVX 200. Suddenly almost anyone could buy a video camera that shot 24p HD video for $5000, and its images looked pretty good. Although the quality of the images was not quite as good as that of the $100,000 cameras, it was good enough that footage shot on both cameras could be seamlessly intercut.
Steve and Jens were blindsided by this game-changing technology. They knew that the video camera rental business would never be the same. Until then, normal people didn’t buy professional video cameras, they rented them because quality cameras were far too expensive. Now, most professional and avid amateur video/filmmakers were going to buy their own relatively high quality video cameras.
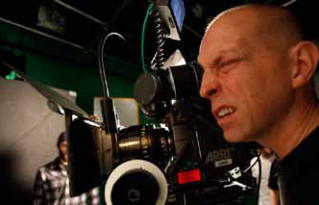
A New Opportunity
“We were quite upset, but that was the greatest thing that could have happened to us as a company,” Steve says. Steve and Jens knew that the only way they could stay in business was to find a way to serve the needs of video makers who would be using these new prosumer cameras. After trying out the new technology for themselves they realized that although the video from these cameras looked pretty good, the physical design of the cameras was poor for shooting in a professional manner. The cameras were small, and often not ergonomic, so they were awkward to hold steadily while a cameraman walked with them. The expensive old school cameras were much larger and heavier, but they had been well designed in many respects—they balanced naturally on the shoulder of the camera person and had an electronic viewfinder designed to fit conveniently against the camera person’s eye.
On walls throughout Zacuto’s headquarters, large ancient video cameras are mounted like animal trophies. During my visit, Steve pointed to one of the trophy cameras and with both conviction and sentimentality exclaimed, “That was a great design, ENG—Electronic News Gathering style.”
Inventing the Rigs
As much as Jens and Steve loved the old cameras, they knew what they had to do for their business to survive. They had to make the new prosumer cameras practical for shooting video in a professional manner. So they dove into the manufacturing business, building kits of parts primarily made from aluminum and plastic, which connect with one another to form camera rigs. Steve refers to this concept as the “tinker toy” system. The majority of parts are secured to one another with rods that fit into holes. They are held in place with clamp mechanisms, as opposed to threaded screws. This system gives the pieces flexibility to slide and turn at different angles, so the camera person can customize the rig to their preference.
How It Works
The foundation of Zacuto’s rig system is the Universal Baseplate. They call it universal because it is designed so that any camera can be secured to it. When the camera is secured to the baseplate it has the ability to slide vertically, horizontally and be raised in height. The Universal Baseplate is used to secure the camera to a shoulder mount, tripod or other Zacuto designed devices to hold up the camera. The baseplate is mounted on 15 mm aluminum rods. The rods are made to connect to other components which clamp on as arms. The arms hold features such as handles, microphones, mat boxes, monitors and mechanisms that enable a camera person to smoothly focus or zoom.
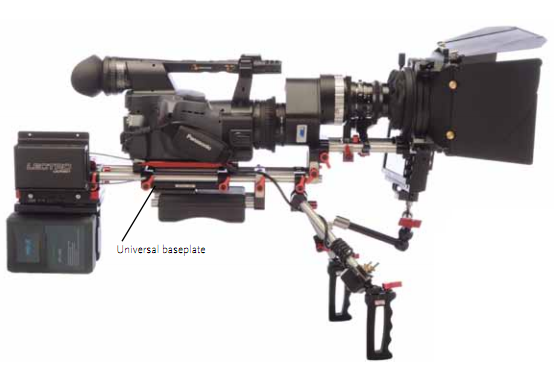
The DSLR Revolution
Today, Zacuto’s rigs are more valuable to filmmakers than ever because of the proliferation of DSLRs (digital single lense reflex cameras) which can shoot extremely high quality 24p 1080i High-definition video. Since HD video capability was introduced to DSLRs in 2008, millions of filmmakers worldwide have fallen in love with them for they same reason they loved the VariCam and its prosumer offspring, these cameras have the ability to deliver high quality images resembling those of film for a relatively cheap price. For readers unfamiliar with the terminology, DSLR cameras are the modern digital version of the large still photography cameras traditionally used by professional photographers (SLR cameras are the original analogue version). Photographers and filmmakers like these cameras because they have interchangeable lenses and large image sensors which allow similar depths of field and picture angles to film formats.
Prices of today’s DSLRs without lenses can range from as low as $500 up to $3000, which can sound wonderful to an indy filmmaker on a tight budget. However, despite the potential of these cameras to produce beautiful images, the reality is that they have not been engineered for shooting professional video.
DSLRs are awkward to hold steady for long periods of time, their viewfinders do not work when shooting video, their built-in microphones are lousy, and it is difficult to adjust the cameras’ focus or zoom smoothly on the fly while shooting. Zacuto makes products to solve these problems, costing as low as under $100 for small accessories to several thousand dollars for rig-building kits.
The Production Process
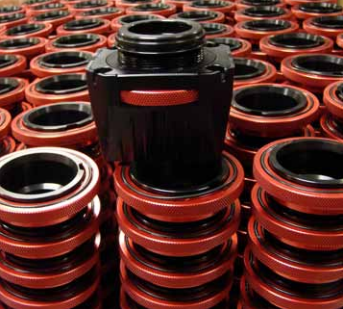
Steve and Jens decided from the start that they wanted to manufacture the parts for their Zacuto kits locally as opposed to overseas. One reason for this decision was their concern for quality control, but mainly they needed to have easy and fast communication with their engineers and contract manufacturers because almost every week they are coming up with new ideas for products. With their current workflow routine they can think up a new product and have it on the market in six weeks.
When Steve and Jens come up with a new product idea they first talk to their engineer Bob Zajeski of ZETA Engineering Company, Homer Glen, Ill. He creates an e-drawing and on the same day they analyze it, tweak it and send it back to him. A prototype is then made which gets sent back and fourth for further adjustments. When they come up with a prototype they are satisfied with they test it by using it to shoot a video. Zajeski, who has designed 280 products for Zacuto over the last five years, explained that with the introduction of the lightweight DSLRs, they have had to adapt the kits. Recently they have reduced the weight of the parts by using carbon fiber and thinning out the walls.
A huge advantage for Steve and Jens in developing new products is that they have over 50 years of filmmaking experience between them and they are constantly producing new videos. They use the video equipment they need to build accessories for, while their competitors just observe the technology from the sidelines. For example, one recent trend in video production that Zacuto has addressed is the growing popularity of shooting video with the iPhone. Jens and Steve have designed rigs specifically for the different models of iPhones, consisting of a handgrip attached to a cradle which the phone locks into. They also sell a viewfinder, their patented Z-Finder, that attaches to the iPhone’s screen to give the shooter more stability and a better view of the image.
Manufacturing the Kits
The bulk of Zacuto’s parts are machined at BEM CNC, Schaumburg, Ill., a job shop that makes parts for an array of different industries.
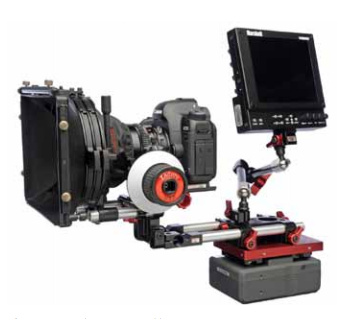
The parts are machined primarily on milling centers. Fast changeover is a priority rather than fast cycle times because new products are constantly introduced. Volumes range anywhere from 10 to 500 parts. BEM CNC uses several Mori Seiki horizontal machining centers and Brother pallet machines because the pallets enable quick changeover.
Bogdan Falat, one of BEM CNC’s owners, said that the tolerances for Zacuto’s parts range in tightness. The parts aren’t going into airplanes, but Falat said that some of them are relatively intricate. He also said that Zacuto puts a high priority on the aesthetics of the parts. BEM CNC constantly watches over the parts to make sure their red color is consistent when they come back after being anodized.
Zacuto’s Next Challenge
Steve and Jens have recently embarked on their first foray into electronics by engineering the very first electronic viewfinder (EVF) specifically designed for DSLR cameras (see photo below). In essence, it is a 3.2” monitor that one will put in front of the viewfinder Zacuto currently makes.
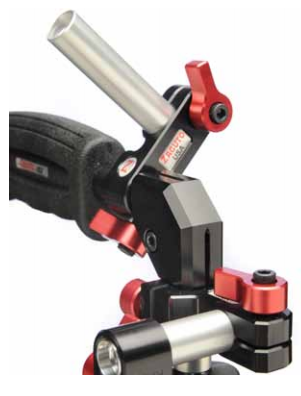
One of the current drawbacks of shooting video with DSLRs is that although the cameras have viewfinders for taking still photos, a camera person can only see their video images on an LCD screen on the back of the camera. This is the trend for most consumer and prosumer video cameras today—to see an image the camera person has to look at a flip-out LCD screen. LCD screens can be difficult to see when you’re around a lot of sunlight, they are not as accurate for focusing on an image, and they take away an important method for holding a camera steady—pushing it firmly against the eye.
Presently, Zacuto manufactures its Z-Finder, which is a viewfinder that attaches directly onto the LCD panel on the back of the DSLR camera. It helps to steady the camera, block out light, and focus, but a camera person must have their face pushed right up against the camera at all times, which limits the ways it can be rigged and positioned.
The new electronic viewfinder will enable a camera person to look through a viewfinder that isn’t pressed up against the back of the body of the camera. The camera body connects to the viewfinder with a standard HDMI cable, the same cable one would use to connect a computer or HD camcorder to an HD TV. All the parts for the monitor will be assembled and manufactured in the United States apart from the panel for the screen. Jens and Steve say there is no other company they know of today that manufactures an electronic monitor of that type in the United States.
Their First Love
When Steve and Jens went into the manufacturing business in 2004, they made a vow to themselves that the only way they were going to do it was if they could fulfill their personal passions to make films too. Jens and Steve produce three ongoing Web series, Critics, Film Fellas, and The Great Camera Shootout.
On Critics Steve and co-host Philip Bloom review films created specifically for the Web. On The Great Camera Shootout Steve and Jens Compare the latest DSLRs with traditional film cameras. On Film Fellas they record veterans of the film industry discussing the world of filmmaking over dinner. In addition to those series, Steve and Jens are constantly making videos demonstrating and educating current and potential customers about their products. All of the videos have a great energy, and Steve and Jens glow as they have fun with their products and discuss filmmaking. The videos speak to the heart and soul of the two manufacturing filmmakers, who approach their lives’ work with a refreshing zeal.
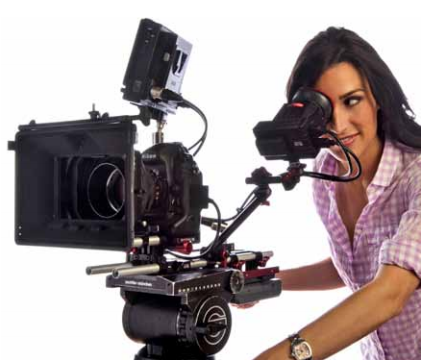
“If you were to ask me … first and foremost, I’m a filmmaker. And that’s what I want to do. I’m a manufacturer and I love doing it, but I started as a filmmaker and I’m going to end as a filmmaker,” says Steve.
Jens follows, “It’s still weird to think that we’re manufacturing. It’s another creative outlet, just … I’d rather make films than make the products. But at the core, it all comes from probably the same part of your brain—the creative part. You’ve got to be creative with anything you do.”
For more information or to watch the videos mentioned
in the article visit Zacuto at www.zacuto.com.
1 Comment
Made in America, hight quality, rugged, who could ask for more. I have Zacuto rails, base plate, etc. and love them.
I wish Apple would make their computers in the US and put some of our people back to work. I would vote for tariffs on Chinese police-state made products.