With Alan Earls
Today’s Machining World Archives January/February 2011 Volume 7 Issue 1
Today’s Machining World’s new feature “Origins” tells us the stories of how successful technologies, companies and people got their start. This month we interview a pioneer of rapid prototyping technology, Scott Crump, the founder and CEO of Stratasys Inc.
Back in the mid-1980s PCs were just starting to take over the workplace and CAD/CAM was a bleeding edge technology that only large companies could afford. The idea of a machine that could create 3D parts automatically was pure science fiction.
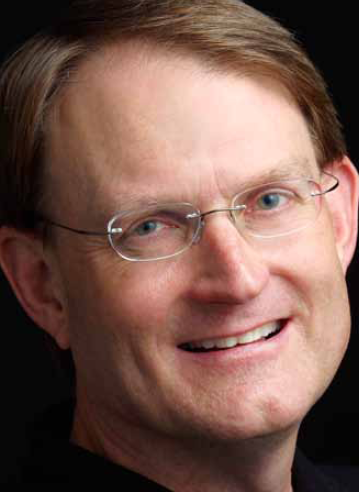
That changed between 1987 and 1988 when Scott Crump had a vision of an easier way to create prototype components, which resulted in the invention of a technique called Fused Deposition Modeling (FDM). (Generically, FDM can also be referred to as “additive” technology.) As it turns out, others were thinking along the same lines, notably 3D Systems, which actually brought its own prototyping system to market in 1987, two years before Stratasys.
Although the development of 3D prototyping technology generated considerable excitement, initially it was too expensive for any but the largest companies. But there were enough customers looking for a competitive edge, particularly those in aerospace, medicine and automotive, to make Stratasys viable.
It wasn’t long before these early adopters discovered that they could use Stratasys products not only for prototyping but for making production items, too. In fact, the ability to produce in small quantities began to seem like a competitive advantage. Since the first machines, dimensional tolerances and surface finish have improved. Costs for the machines have also dropped dramatically from the six figure range to the low five figures.
Additive technology has proven so successful that it is often used for small and medium-size production runs and, for manufacturing concerns, has proven to be a cost-effective method of producing custom tools and fixtures.
What inspired you to develop this technology?
CRUMP: While running another company I experienced firsthand the need to get prototypes quicker and less expensively than the traditional manufacturing processes allowed. I realized that every manufacturer faced the same problem I did. I imagined there being a better way.
Did you have a specific vision for what the technology might do?
CRUMP: I dreamed of a machine that could help the design engineer get prototypes quickly and without the huge expense. I thought that if this were possible it could make product development departments much more efficient and enable designers to improve products, because they wouldn’t be so limited in the number of prototypes available to them. With additive manufacturing equipment, in-house engineers can make a dozen iterations of a design if they choose, and the design gets better each time. The second part of that vision was the windfall—the savings in tooling costs that naturally follow.
Have you been surprised at the growth and development of this technology and the way it has been applied?
CRUMP: The vision I had was to provide a small machine that would fit on the desktop of the design engineer and be affordable by any design or manufacturing organization. This has really become a reality in the last few years, which has driven the growth in unit sales. Something that never ceases to amaze me are the unique applications manufacturers continue to find for additive manufacturing. I never imagined that fashion designers would make purses and clothing with this technology. And I didn’t imagine the business of Shapeways.com, which builds customized items for consumers, or that cities would build models of their entire downtown to promote tourism.
What have been the biggest challenges in developing and improving the technology?
CRUMP: It’s a continuing challenge to drive the cost down while bringing the machine quality up and reducing the footprint of the machine. We’ve come a long way improving machine accuracy and repeatability, and have greatly reduced machine size. But these are ongoing challenges that will never end. Another major challenge was to create a better user experience by making the machines very simple to operate. We have come a long way in this area. Several of our machines can be run by beginners with no training. They just follow prompts on an LCD menu.
Where do you see the technology evolving and fitting within manufacturing enterprises?
CRUMP: The various additive manufacturing processes available are already being used frequently for producing manufacturing tools like jigs, fixtures, assembly aids, guides and gauges. They are also being used for low volume manufacturing of parts. Additive manufacturing is so much more efficient and cost effective than traditional processes, it’s just a matter of time before it becomes mainstream. In the not too distant future additive manufacturing equipment will reside in every shop next to the machining equipment.
How could precision machine shops and others in similar manufacturing fields use additive technology in their shops today?
CRUMP: They can use this technology to help win bids. Overnight, you can produce a physical model of the customer’s job to give them immediate feedback. You will pleasantly surprise the customer because they are used to waiting for weeks to see a part.
It is also a great way to make manufacturing aids, like jigs and fixtures. One of the biggest benefits to any size of manufacturer is to quickly and inexpensively produce custom manufacturing and assembly tools. Every manufacturer needs a variety of custom tools. With additive manufacturing, you can have that tool in under a day and you can save from 50 – 95 percent of the costs. It can also help make short run production parts. Although it’s not for mass production, if you make only 10’s, 100’s, or a few thousand of any given product model per year, there’s a good chance additive manufacturing could save you an enormous amount of money. You can eliminate the high costs of individual part machining or of making injection mold tooling and let the additive manufacturing system build the components using nothing but the CAD file. The machine can even produce complex assemblies, already assembled, requiring no humans to do it.
Getting started is easy. You can initially use a service bureau— we have our own but there are many others—or you can invest in the technology yourself. Our products start at around $15,000 and range up to around $450,000. The main difference is the maximum build size. Our largest machines can create parts up to 36” by 24” by 36”. There are also some differences in the range of materials and ease of use.