U.S. commerce is moving underground, especially in Kansas City. Lured by the promise of low overhead and virtually no infrastructural investment, some four hundred enterprises currently call subterranean Kansas City home. Working below the sidewalk offers numerous advantages beyond cost reduction, and surprisingly few downsides.
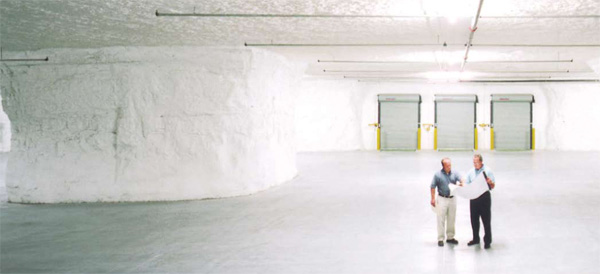
The world below has captivated mankind since that day in misty prehistory when the first proto-human shed its tail. There’s something weirdly compelling about the great unknown beneath our feet, a fascination potent enough to inflame tinder in an artist’s soul. Writers from Dante to J.R.R. Tolkien set portions of their most important works in the planet’s entrails, as did painters like Hieronymus Bosch, whose notorious triptych The Garden of Earthly Delights is still considered by art historians and psychologists alike, the most disturbing depiction of The Region Infernal ever to curse a canvas.
In recent years, commerce has trailed the artistic imagination deep into the belly of Mother Earth. Nowhere is this trend more evident than in metro Kansas City, where hundreds of businesses earn their living in the city’s sub-terrain. Strange, given K.C.’s reputation as something of a dowager among U.S. metros, not exactly famous for a willingness to embrace progressive concepts in business practice, or for that matter, much of anything else. Yet it turns out this Bible Belt buckle of a Midwestern town is uniquely amenable to underground commerce, as it sits atop a subsurface honeycomb comprising literally millions of square feet.
“Kansas City is a natural for mining,” explains Dave Melzer, project manager for Dean Realty Co., the region’s first underground real estate developer. “You can cut horizontally because the rock lies at an elevation accessible to development. There’s also a lot of naturally-formed, subterranean space, which combined with the mines, has created what amounts to a second land-use opportunity. This made our town more geologically suited to underground development than most, and because the environment below is also temperaturestable, green before green was cool.”
A Natural
Kansas City isn’t flat, as often asserted by people who’ve never been there, but river-valley typical. Bluffs rise mightily along the Missouri, while downtown, city blocks undulate in a manner reminiscent of the urban peaks and valleys of San Francisco. These topographical attributes proved very attractive to mining companies, which launched a helter-skelter exploration of the region’s limestone hills late in the Nineteenth Century. The practice of random burrowing was relatively shortlived. By the 1950s, the region’s industrialists had come to appreciate the advantages inherent in creating a usable underground, and were digging for that purpose as well as mineral extraction.
Today the world below Kansas City is a clean, well-lit environment of cement floors, whitewashed walls and huge, rock pillars. This vast, subterranean realm is subdivided into hundreds of roomy designer spaces, which appear from common areas like storefronts in a shopping mall. Claustrophobia is no problem. Unless one goes looking for a window, it is easy to forget the surface is more than one-hundred feet overhead.
Subterranean Superlatives
So why go underground? It’s cheaper, for one. The price of new construction is not a factor, since all the structure one needs is right there waiting to be exploited. Square footage lease fees are much-reduced as a result, along with the costs of preparation. In dollar and labor terms, the occupation of a previously undeveloped space usually entails nothing more punitive than the installation of a little flooring, lighting and plumbing, and a few fire sprinklers.
Cost-saving point two; the temperature below ground averages a cozy 70 degrees no matter what may be happening upstairs, translating to a roughly 20 percent utility expense reduction. This advantage segues to another, even more important in the long run. When fossil fuel usage decreases, carbon emissions travel in the same direction. The point is that doing business underground is environmentally civilized.
“Kansas City can get blisteringly hot in summer, and just as cold in winter,” comments Hugh Gardner, area manager, Priority Envelope Inc., a printer/manufacturer of envelopes with one of three facilities in the K.C. Underground. “Utility costs can be pretty high above ground, but in a subterranean space they’re not a big deal. That, combined with low square foot leasing cost, had a significant impact on our decision to move down here. We’ve been in our underground facility for more than two years, and while we’ve had to make some accommodations to humidity, everything has worked out pretty well.”
Priority’s subterranean factory consumes 38,000 square feet, and employs 35 people. Like a basement, the space traps humidity, a major issue for a company for whom paper products are stock-in-trade. To get around what might otherwise be a deal-killer, special dehumidifying gear was installed throughout the facility to great effect. A cruise through the plant is like a walk on the beach. The temperature never rises above 70 degrees. Natural ventilation freshens everything, and customized dehumidifiers steal moisture hanging in the air.
“We had to run a lot of lighting and dehumidifying equipment to make the underground concept work for us,” Gardner recalls. “But even after all of that was factored into the equation, it still made good economic sense to set up shop down here. The scope of envelope manufacturing is very large, and until quite recently, plants were rarely air conditioned. A facility will get really hot in the summertime, so compared to the megabucks we’d have to throw at A/C, the costs of extra lighting and dehumidifying are practically negligible.”
Ventilation also factors in other types of light subterranean manufacturing. This is certainly the case for Byrne Custom Woodworking Inc., a K.C.-based producer of mid to high-end residential and commercial wood products. According to owner Ian Byrne, the dust clouds generated in furniture making necessitated an investment in exhaustive vents for every piece of equipment in the facility.
“It wasn’t cheap,” owner Ian Byrne recalls. “We had to lay out roughly $40,000 for a single dust dispersing unit with multiple attachments. Dust is only one of the issues you have to cope with when making furniture in a closed space. Another is fumes, for which the cost of an exhaust system is more than we can currently afford. In some ways this slows us down. We offer a line of pre-finished cabinets, but because of the hazards you run into with fumes, we’ve have no choice but to work on them off-site.”
Fumes are potentially destructive not only to the lungs of employees but the facility itself, Byrne adds. A single spark can be enough to cause a massive explosion in a vent-less, fume-permeated space, a sobering fact that all by itself cancels any possibility of doing finishing work underground.
What About Shop Work?
The answer is “yes,” with stipulations. Take the case of K-Ter Imagineering Inc. a machinery and tool manufacturer with several years in subterranean K.C. According to President Roger Gubbels, working below imposes limitations on manufacturing operations that can have hampering effects on operational efficiency.
“Ceiling space is at a premium,” he explains. “Sixteen feet is all we’ve got, and sometimes that’s not enough. You also can’t do spray painting underground because of air quality issues. We used to paint frames with a brush and roller, but when that became impractical we gave up on painting altogether. There are strict regulations in effect, limiting what you can and can’t do in a closed environment, and we have to abide by every one of them.”
But the assets earned operating underground more than outweigh the liabilities, Gubbels admits. Some affect areas of business one might not normally think about in that context. Insurance is one example. K-Ter’s rates have gone down overall because the company no longer has to worry about being on the receiving end of a twister, or some other act of God arriving out of the blue. K-Ter also pays less for fire protection by virtue of the fact that limestone doesn’t burn. A sudden conflagration may take out equipment, or God forbid, people. A limestone mineshaft, it can’t destroy.
“The underground offers manufacturing operations like ours a number of significant cost and comfort perks,” adds Robin Collins, office manager, Collins Machinery Inc., a manufacturer of sawmills and portable backhoes. “Our facility is nearly 15,000 square feet, big enough to contain 17 employees, a forklift, four welding machines, a Miller mig welder and a plasma cutter. The welders and assembly people love the space because they get to work in a temperate environment all year long. I love it too, except in late August when we get our yearly gnat infestation. That inconvenience lasts only a month, and the remaining eleven more than make up for it.”
1 Comment
Great article about “going underground”. At Pride Machinery’s new Independence Missouri plant our 3D CAD Engineering division is quite busy working with companies in the underground. By the way, Kansas City area is the best keept seceret in America. Let’s keep it that way, we came from California to get away from unmanageable traffic, taxes and restrictions. Shhhh don’t tell anyone.