This question about Wickman threading attachments came from Bob Schneeberger of LD McCauley in Orchard Park, NY.
BOB’S QUESTION:
Our client needs a thin walled brass part. My screw machine is a 1” 6-spindle Wickman. We were concerned about flaking in the threads with brass parts so I knew I had to come up with a cut thread. Our two options were thread milling and thread chasing. We couldn’t get the brass to gauge on our Johnson Gauges because of the flaking. I tried running a drill inside the part while I was thread rolling to avoid crushing of the part but it still didn’t gauge. I tried putting a thread chasing die on the machine and saw that the lead on the threads (or the pitch) was off. We had tracking problems. The thread die is 400 thousandths wide. It wasn’t tracking properly as it ran across the part.
We went through the machine and the chasing attachment looking for the cause of the problem. The attachment had just been rebuilt by a very reputable source. We did see a little play as the cams rode inside the thread chasing attachment. We eliminated the problems in the attachment but our pitch was still off. We are now going to try a thread milling attachment and a thread milling die. How can we eliminate the play in the thread? What caused it? Do you think this will solve the problem on the thin walled part?
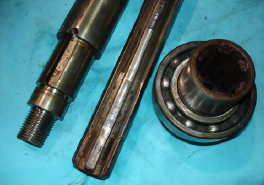
AL’S ANSWER:
On a 1” Wickman, on the center drive shaft where the spindle speed gears are mounted, there is a coupling between the back half of the drive shaft and the front of the drive shaft. As the machines get old, and typically because people run hex material on these machines, they start to pound out the spline on the shaft and the coupling gets loose. This creates looseness or play in the machine, which I call “slopposis.” Toward the spindle end of the machine there is a drive key that engages the main spindle drive gear. That key can get pounded out and you get slopposis at that point. On each spindle there is a drive gear that engages the center drive gear. If the keyway on the spindle is pounded out that is another source of slopposis.
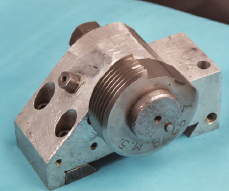
When you chase a thread with a single point thread chasing attachment you use a multiple tooth chaser. If for some reason there is play in the machine and the lead does not repeat itself, in other words it doesn’t track in the same place every time, you will get a very sharp crest on the major diameter of the thread. If you look at the thread on a comparator it will show a very sharp crest on the major diameter of the thread and you will notice a wide area at the minor diameter of the thread. What is happening is that the chaser is not following the lead of the thread, and the chaser is shaving the sides of the thread.
You should check the lead on the thread chasing attachment. Usually what I do is mount a dial indicator on the thread chasing head manually (without the machine running). I turn the spindle one complete revolution to advance the thread chasing attachment to the lead of thread. Now lets say it’s supposed to travel .062 per revolution – if you do this three or four times, the lead should be within a tenth or two at the end of it.
The attachments do wear out, but that is probably not the case with yours because your attachment was rebuilt by a reputable source. However often people will put the thread chasing cam on the attachment and forget to put the spacer washers on. This would result in the cam flopping back and forth, which will throw the lead off.
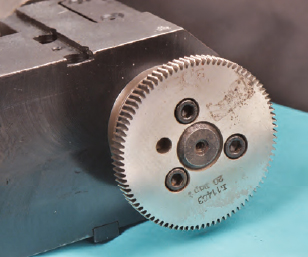
BOB’S QUESTION:
Do you think using a thread milling attachment and a thread milling die will solve the problem?
AL’S ANSWER:
Thread milling is a completely different system than thread chasing because the lead is built into the tool itself. There is probably less chance for slopposis to affect a thread mill than to affect a thread chaser because the load is constant all the way through the cut. On a single point thread chasing attachment every time that attachment makes a pass the machine is loaded and then unloaded. So thread milling could be the way to go, especially because it’s a thin walled part. The chip load per tooth is much lower with thread milling than with thread chasing.
Al Seniw of New Lenox Machine Co., Inc. in Dwight IL. Al has been working on Wickmans for forty years and he has taught machining courses at community colleges.
Today’s Machining World Archive: June/July 2005 Vol.1, Issue 06