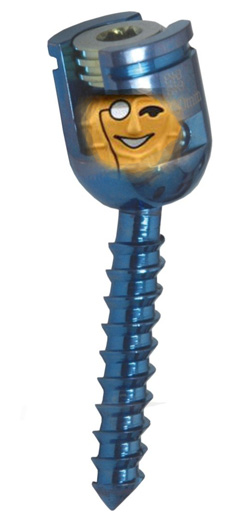
Dear Shop Doc,
I’m going to be rotary broaching a 9/64” hex in titanium. The hole is a blind hole about .160” deep. I’m worried about hydraulic pressure building up during the broaching operation. What are my options?
Mr. Bone Screw
Dear Mr. Bone Screw,
You have a few options available. But first, let’s talk about the hole. Be absolutely sure to drill it deeper than the broaching depth. You will need to leave room for chips, fluid, etc. The deeper the hole, the more room is available for swarf to get out of the way.
The first option has to do with your pilot hole. A pilot hole drilled to size will create significantly more pressure than one drilled oversize. The oversize hole allows air and fluid to escape. This larger pre-drill diameter also reduces the size of the chip while broaching. The chips are also sure to be separated. A standard 9/64” hex has a dimension across the flats of .1425”. Drilling the pilot hole about 3 percent larger, requires a drill size of .147”.
The following tooling options are all intended to reduce pressure while broaching. Most of these options are commonly available in the marketplace.
- Spun, Ground Diameter – Eliminating the sharp corner from the broach reduces chip size and depth and strengthens the broach at the corners. Rotary broach failure is often a result of chipping at the corners.
- Broach Pressure Relief Holes – Small holes added to the center of the broach and used in conjunction with secondary holes drilled in a cross direction allow the fluid and air to escape.
- Broach Holder Relief Holes – A relief hole in the broach holder allows air and fluid to escape completely. Air and fluid are pushed through a center relief hole in the broach, and out of the holder through its relief hole. This option is currently available from Polygon Solutions and reduces cost of broaches requiring two vent holes.
Here are a couple tips to make sure you get the most out of your tooling. Make sure the broach is aligned with the pilot hole. This may seem obvious, but many machines can be off center by more than a few thousandths. Most broach holders have end play built into them. The broach will follow the hole. But double check it anyway; this is a common troubleshooting problem. Also, if you’re going to be broaching titanium, upgrade to a premium broach material, such as M-42 or PM T-15. These broach materials are very hard and include elements like cobalt to enhance their strength.
As you can see, all of the information here has to do with reducing the forces required while broaching and strengthening the broach. Hopefully these tips will relieve some of the pressure created when trying out a new machining operation. If you’re still uneasy, run the broach in aluminum to get a feel for the set-up.
Peter Bagwell is a Rotary Broach Product Engineer at Polygon Solutions. He is a frequent contributor to Today’s Machining World’s Shop Doc column and is also an Essential Oil enthusiast. To contact him, go to www.polygonsolutions.com.
3 Comments
Peter, Hydraulic pressure can be alleviated by using Broach tool with holes thru them. While making millions of bone screws for a leading medical devices company I push and rotary broached many bone screws, both small and large. I can’ give you the manufacturers name due to NCO but you should be able to find one doing an internet search.
Tim,
Thanks for the reply. I think your point about ‘thru’ holes and my point about pressure ‘relief’ holes are the same. Some rotary broaches are available with through holes as a standard feature, some with additional cost. Cross-vent holes are also avilable.
Hi,
I have manufactured tens of thousands of bolts, but have never noticed a problem with not having pressure holes, can you tell me the symptoms ? and if this only applies to smaller fixings ?
Thanks