By Barbara Donohue
Today’s Machining World Archive June 2010 Volume 6 Issue 05
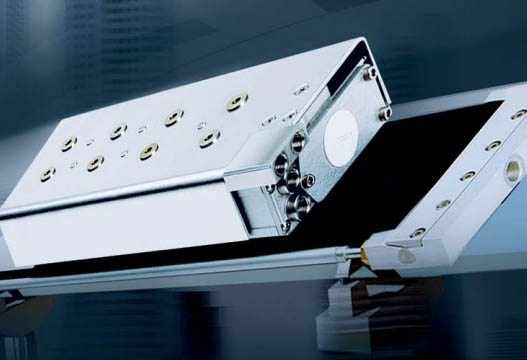
Electric motors go around and around, right? Not necessarily. About a hundred years ago, the idea of a linear motor was conceived—a motor that directly produces straight-line motion, rather than rotary motion. Over the years, inventors and engineers developed many different types of linear motors, suitable for many kinds of applications. You’ve probably seen machine manufacturers touting products with “linear” in the name, as these unusual motors have begun making their way into machine tools in recent years.
How a linear motor works
The familiar type of rotary motor depends on magnetic attraction to make the shaft rotate. Magnets located around the circumference interact with the magnetic fled produced by windings affixed to the shaft, which pulls the windings around and makes the shaft turn.
You can think of a linear motor as the same thing—magnets and a coil. But they are “unwrapped” to lie fat. There is a fixed component (called the track, platen or secondary) and a moving component (called the forcer or primary).
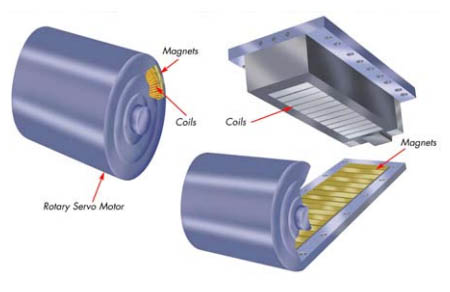
In this type of linear motor, the track, or fixed component, contains a series of permanent magnets laid side by side along its length, and the moving component contains electrical windings. When current flows through the windings, the resulting magnetic fled engages with the fled from the magnets in the track, causing motion. You can increase the length of the motor simply by adding more fixed sections. In one machining application, the linear motor was 100 feet long.
Manufacturers build many types of linear motors, large and small, with different technologies and capabilities. MicroMo Electronics, Inc., Clearwater, Fla., produces a tiny linear motor that uses piezoelectric “legs” that essentially walk the output shaft back and forth with nanometer resolution. Baldor Electric Company, Fort Smith, Ark., manufactures dual-axis linear motors that position the moving component anywhere on a rectangular platen, across both the length and width.
The linear motors designed for various types of machine tools are typically linear servomotors. For some applications—most often the X and Y axes on a vertical machining center, for example, or all three axes on a laser cutting machine—linear motors provide distinct advantages over the usual rotary-motion-into-linear conversion through ball screws or other devices.
Each model of motor has its own dynamic and force characteristics. When a single motor generates insufficient force, adding a second moving component on the same track can increase the load capacity, said Steve Czajkowski, application engineering manager, motion control business machine tools; Siemens Industry, Inc.; Elk Grove Village, Ill. This is similar to connecting two rotary motors to a single shaft to produce higher torque.
The operating characteristics of a linear motor
Linear motors bring several advantages to an application:
- High traversing speeds
- High acceleration
- High precision
- Elimination of mechanical transmission elements, such as ball screws
- Long life: only one moving part, and, because the motor elements don’t touch, no need for lubrication
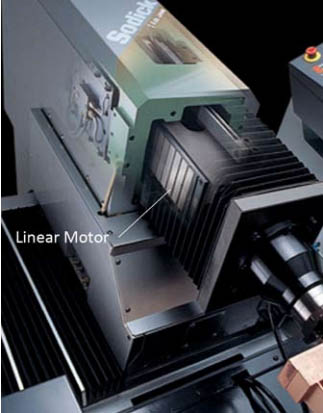
Linear motors directly produce the back-and-forth linear motion required by machine tools and many other applications. Where a conventional rotary motor is used to drive a load in a linear motion, some kind of mechanism is required to transform the rotary motion of the motor shaft to the desired straight-line motion. A mechanism such as a linear ball screw, rack and pinion assembly or linkage can do the job. Each type of mechanism places one or more components between the motor and the load. Each component defects to some degree, and everywhere components connect there is a potential for backlash.
With a linear motor, the moving component moves the load to the desired position. A linear encoder, sometimes called a tape scale, reads the location precisely. According to Siemens literature for 1FN series linear motors, “If suitable measuring systems are used and the temperature conditions are appropriate, the motors can be positioned in the nanometer range.”
Because linear motors can accelerate and move very quickly, the controller needs to be able to handle such rapid movement. “It’s not just the motor components. It’s the control,” as well, said Dave Thomas, president of Sodick, Inc., Schaumburg, Ill. “You can add a linear motor to a machine, but if your controller can’t handle it, it loses [some of it’s] advantages.”
“With a traditional ball screw or rack and pinion there is a good deal of mechanical stiffness,” or resistance to movement of the load, Czajkowski said. A linear drive, by contrast, depends on the control system to realize constant position. To test dynamic stiffness, the mass is struck and the axis defection measured as a function of the force of the hit. This can be compared to the force of a cutting tool coming into contact with a workpiece. The lower the defection for a given external force, the better.
The linear motors are fast, and are especially good for use where the table needs to be traveling fast, aerospace and automotive applications, for example, said George Yamane, marketing manager, Mazak Corporation, Florence, Ky. The force the linear motors are capable of providing is less than a conventional drive setup can achieve, so they are best suited for applications with lower cutting forces, he said.
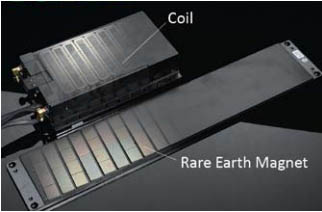
Because linear motors accelerate and move so fast, they can cut machining time if the tool needs to move frequently from place to place on the work piece. Even short distances add up, Yamane said, and high acceleration and rapid traversing can save considerable time.
To operate at their full rated capacity, linear motors may require special cooling, with air or liquid.
Linear motor applications in metal cutting
Linear motors were first applied to metal cutting back in the 1990s, in a laser cutting machine, Czajkowski said. Since then, linear motors have found application in machining, laser- and water-jet cutting, electrical discharge machining (EDM) and honing, he said.
The precision and stability of linear motors makes them ideal, even for some applications that do not need their speed. Sodick, Inc., makes linear motors and controls, and builds EDM systems that use them, said Thomas. The linear motors provide better positioning accuracy than ball screws, he said. Ball screw machines typically showed a loss of accuracy after one or two years, and high-precision customers often needed to replace the ball screw driver after three years. Linear motor EDM machines showed no detectable loss of accuracy over five years. By 2001 all Sodick machines used linear motors, Thomas said. Sinker EDM systems take advantage of the linear motor’s speed, too, by using the advancing tool to flush out debris from the hole or cavity, he said. This eliminates the need to drill flushing holes in the work piece.
More recently Sodick developed a line of linear motor machining centers. They are high speed surfacing machines designed for high precision, small features and producing a fine surface finish. “We are able to do what is not possible with a ball screw, which has inherent vibration and backlash,” Thomas said. Linear motors produce next to no vibration and have zero backlashes. For operations with very small cutters, linear motor machines provide the acceleration necessary for keeping the tool in the work with the correct chip load. Consistent loading and the lack of vibration help extend tool life and prevent breakage, he said.
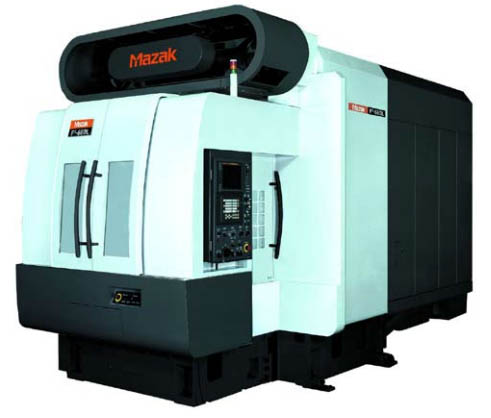
Mazak Corporation uses linear motors in some of its machining centers. “The F3-660L [horizontal machining center] is designed for automotive applications, especially for die-cast aluminum,” said Yamane. “Automotive manufacturers put a lot of money up front for die castings such as transmission casings,” where the F3-660L would be used for operations such as facing and hole making, he said. This machining center uses linear motors for X, Y and Z axes, and offers a traverse speed of up to 208 meters/minute (8189 inches/minute), according to product literature.
Simple concept, big benefits
A machine tool that uses linear motors will offer faster traverse speeds, higher precision, lower vibration and lower maintenance cost than a similar conventional machine. Linear machines can also provide longer tool life and lower operating cost. If you have a suitable application, linear may be worth considering the next time you’re planning to buy.