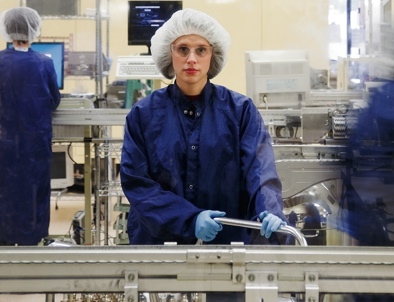
The news that Japan will show a net deficit in trade for 2011 is another signal of a shifting economy that currently favors North American manufacturing. Europe is in a mess, and with the Euro still hanging in at $1.30 and no real structural changes yet, it is also losing competitiveness.
The Mori Seiki plant now being built in Davis, California, near Sacramento is a clear sign of the sea change happening now. Equally significant is Honda’s announcement that it will be building its first Acura in Ohio in three years.
Mori plans to build 20 percent of its production in the U.S. and interestingly, 20 percent in Europe, indicating that its partnership with DMG appears to be working. With Mazak entrenched in Kentucky, I am expecting Okuma to once again manufacture machines in the U.S. They used to produce in Charlotte, which has quietly become one of the machine tool centers of America, and it would make sense for them to start building in that neighborhood again.
Would it be a stretch to see companies like Citizen, Star, even Doosan and DMG begin production in North America? Romi of Brazil, which made a pass at Hardinge, is another candidate. And when is Hardinge going to finally move out of Elmira?
*****
I highly recommend Adam Davidson’s cover story on manufacturing in the current Atlantic. Davidson is one of the finest economic journalists around today, and this piece is one I wish I had written. He wrote about the people of Standard Motor Products, a manufacturer and distributor of after-market automotive products, based in New York City with a big plant in Greenville, South Carolina. It is run by Larry Sills, 72, third generation of the founding family, but publicly held.
I loved the way Davidson focused on Maddie Parlier, a 22-year-old “level one” operator working in the clean room of the company’s fuel injector assembly line, and 27-year-old Luke Hutchins, a “level two” operator who oversees a 7-axis Gildemeister turning center.
Maddie has worked for the firm for three years and is considered a topnotch employee, but she is held back by lack of sophisticated education. Pregnant at 17 in high school, she had to forgo college to work and take care of her baby. As much as she would like to enhance her training now, she cannot afford the time away from her job and child. So she is stuck, and worried that a robot might take her job. And it could happen, if demand picks up enough to justify the capital investment by the company.
Hutchins, the Gildemeister operator, had the family backing and the time to choose his career path. He went to a four-year college, taking biology to become a dentist. He got bored and then thought he would follow his mother’s career path in radiography. Then a friend told him he could made $30/hour if he learned to run complicated machine tools, so he shifted gears and enrolled at Spartanburg Community College where he took a lot of math and learned CNC programming.
Now he is a key guy at Standard Motor in Greenville and doesn’t worry about his job.
I strongly recommend that you read this piece and share it with your friends and family. Even if you know and live this stuff like I do, you will still get a lot out of the article.
******
The Peyton Manning-Indianapolis Colts-Andrew Luck drama is one of the most fascinating sports, business and human stories to come along in a while. Manning, probably the greatest pro-quarterback ever, sat out this season with a neck injury. The team went 2-14 giving them the #1 draft pick, almost surely quarterback Andrew Luck of Stanford.
Luck, whose father played in the NFL like Peyton’s Dad, Archie, could be the next great NFL quarterback. But – maybe he’ll be Ryan Leaf instead. Manning will require $28 million if he comes back to the Colts. But he’s 36 and recovering from surgery and a stem cell procedure.
If you were Manning, would you play again? If you were Jim Irsay, owner of the Colts, would you risk $28 million on him? If you were as good as Luck, would you want to apprentice to Manning for a few years like Aaron Rogers did with Brett Favre?
In business we are often faced with tough calls about bringing in the “next big thing” and letting go of the “horse that brung you.”
Read Adam Davidson’s cover story on manufacturing in the Atlantic here.
Question 1: Would recruiting as is done for high school athletes work for recruiting new manufacturing talent?
Question 2: Would you release Peyton Manning if you owned the Colts?
6 Comments
Yes, my two sons and daughter took machine ship in high schools (1978- 1982) and worked on a drill press after school in our garage, while my husband was starting his business. All three of them work in machine shops now, know how to operate manual mill & lathe as well as CNC Mill and CNC Lathe and can program the CNC. We have taught one grandson to operate manual and CNC machines as well as programing and teaching another grandson to do the same. We need machinist and not button pushers.
Question 1: Would recruiting as is done for high school athletes work for recruiting new manufacturing talent?
I don’t think recruiting the way it is done for athletes is a model you would want to use but I am sure the attention given to kids who show a mechanical and mental apttitute for manufactruing would build self confidense and encourage kids that it’s ok to not be a Dr., Accoutant, Rapper, Reality Star, Pop Sensation, Pro Athlete, Lawyer, or any otehr profession media hypes as being important and relevant to success.
The fight is with culture and parents telling kids and everyone else that manufacturing works is for stupid, ammount to nothing, trouble makers, who can only find that kind of work and that it does not pay because you know we should all be millionares. Not to mention the majority of the babyboomers instill in their kids entitlement and worked hard so their kids dont have to. Even thoug tons of babyboomers got everyting they have from working in manufacturing.
Question 2: Would you release Peyton Manning if you owned the Colts?
Yes…Even though Peyton has been one of the best QB’s in NFL history no player can be bigger than the health,well being, and future of the franchise. There is still a horseshoe on the side of the helmut not Peytons face.
I have several friends that work in the vocational education field; To them their classes have become a dumping ground for the dysfunctional and troublemaking students; According to one in a class of 25-30 kids there are maybe 1 or 2 that are there because they want to learn the “trades”; Seems the next generation doesnt want to get their hands dirty, maybe when they have bills to pay they will realize the wonderful opportunity presented by the manufacturing world; As for Manning if I was Irsay I would cut him and give him a ticket to Chicago where Bear fans would smother him with love and adulation; Dem bears need a QB!!! In all seriousness I think if I was Irsay I would keep Manning, even if he doesnt play Luck will need his guidance and expirience to be the next QB of the Colts, plus he would make one hell of a coach!
Recruiting high school students is proven to work!!! Our local High School has a great CNC training class. I hired their top student last year and plan on bringing in a few more. They are filled with young energy and the desire to learn. A lot of these kids know they are not college material so they are very thankful to have a job with growth potential other than being a Burger King manager.
Don’t over look the Auto Shop kids either. If they can diagnose problems on a car they can handle most anything mechanical in your factory. Also proven in my shop.
Joe
Hopefully, Manning stashed a bundle under his mattress. He should leave while he is able to move about with out having to use a wheel chair or worse-be connected to tubes for the duration.
As regards careers pointed out by high school administrators-the idea that it’s not college first is alien. There are so many well paying jobs in the skilled trades and some of them are real sleepers. When the crapper is plugged up by one of your grand kids you don’t look for a guy with a degree-you call on your local plumber who knocks down $70k+++ a year which ain’t hay in todays economy.
Recruitment is not the tactic I would use to obtain a dedicated and trained machinist. Two things need to happen simultaneously. An advocacy for the profession, and the means to achieve status. In the middle and late sixties, I was president of one of the largest machining houses in the U.S. There was a shortage of skilled machinists. It started a program to train both machinists and tool and die makers. The effort was a failure, because as soon as the student achieved a minimum standard they left the program for journeyman wages. This was Macon, GA. I went to Europe and stayed for 25 years, but I visited the U.S. on a regular basis. There was a significant change in the education system, especially in the Southeast and Southwest. Community And “Technical Colleges were teaching a new generation the skilled trades and were displaying the results of that instruction in the shopping malls. This is what I call “apprenticeship with dignity.” This is the way to get dedicated workers. South of the Mason-Dixson Line the phrase, “Made in America” is back.