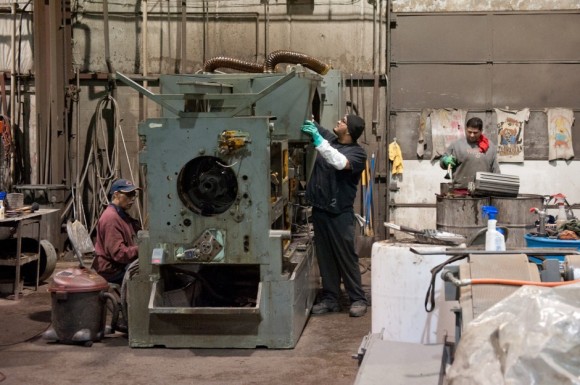
These last several months have been a struggle for me to find workers for the cleaning and painting department of our used machinery business, Graff-Pinkert. You might think, with so many millions of Americans unemployed or underemployed, it should be quite easy to find manual laborers who want to make $11 per hour with the chance to get on the company health insurance plan worth $5 per hour more, plus virtually guaranteed overtime pay and a year-end bonus.
But it isn’t.
I’d like to share my recent experience.
First of all, few women apply for the cleaning and painting jobs. Seemingly, they self-select because the advertising indicates it is a fairly dirty environment to work in, with dirt, grease, oil and chips. In retrospect, I find this a bit surprising and regrettable, because women are moving into all kinds of jobs formerly the exclusive domain of men.
So we mainly have guys to choose from.
During the summer we found a college senior from the University of Illinois, we’ll call him Fabio, who was majoring in Statistics. He was small in stature but savvy and industrious. He caught on immediately to the job and applied himself with a happy attitude. He was a keeper. I noticed it immediately when I asked for a volunteer to prepare our raised tomato garden for planting the vines, a yearly ritual at Graff-Pinkert. He immediately volunteered, which enabled him to work directly with me for a few hours. Fabio understood work was a social enterprise and a physical effort. Without the ability to get along with co-workers and supervisors you do not last, even in a manual labor job.
Unfortunately, Fabio left for college at the end of August and his replacements paled by comparison.
The first failure was hired via Craigslist. We’ll call him Frank. A little guy, he seemed eager for a job. He was 19, a high school graduate living with his grandfather in the area. He seemed shy in the interview. A check for arrests was clean, and I decided to try him on our fledging night shift. I also hired an 18-year-old, Dick, who was in a program at the local community college to prepare kids for joining the workforce. The counselor at the college said he was a good kid, that he was hardworking and “tested off the charts” for technical aptitude. He told me he aspired to be an electrician.
Our nightshift foreman quickly reported problems. Frank disappeared for lengthy bathroom breaks. The foreman also noticed doors were open or unlocked when he was quite sure they had been locked by the first shift group. A few nights into Frank’s short stint at Graff-Pinkert several guys that our foreman called “gangbangers” invaded the parking lot at 11:00 pm to meet Frank when he was leaving work. Our foreman was extremely scared and locked himself in the lunchroom until they left. He reported this event to me the next day. A few days later we discovered that $700 of petty cash from the office was missing.
I could not prove Frank took the money, but I suspected enough to fire him immediately.
Dick, the other kid who had “tested off the charts” was another problem child. He retreated into his phone constantly, was almost totally incommunicative to co-workers, and appeared oblivious to his surroundings. His co-workers saw him as a slacker and constantly complained that he wasn’t doing his share. He also had become chummy with Frank prior to his firing.
In my opinion this kid suffered from being socially ill equipped for a workplace. I felt a little badly that we did nothing to prepare him for the job, but I did not have the inclination to coddle him when his peers had completely rejected him.
Meanwhile, we had hired a temp though an agency who was older and street savvy. He knew he had a good gig and he applied himself, making himself valuable on the shop floor. He did not look like our other employees, with his hair in dreadlocks, but he earned their respect with diligence and following directions. I hesitated to hire him full-time because of health insurance costs, but the temp agency’s weekly charge virtually matched the cost of the health plan.
I also had considered hiring an older guy who seemed intelligent and pleasant, but his 60 extra pounds scared me for such a tough job.
Then, out of the blue, Derrick came along. He had a “big personality” and was completing a course to get a commercial driver’s license. His job pitch appealed to the sympathy factor. He said he was out of work and virtually destitute. He seemed eager and strong so I gave him a chance.
He was great for the first week, then he started to get into arguments with the other men on the floor. He demanded “equality with radio time,” to listen to gospel music, not a good idea for a guy in his second week. He approached me to buy a semi-truck for the company, which he would drive. He started slacking off in the plant and taking long bathroom breaks, while making a grandiose effort to ingratiate himself to me. Our guys hated him. I fired him and received a soliloquy about how he would be out on the street.
I have a better idea about the workforce after these encounters. I respect Starbucks’ ability to hire and train kids, and pick them skillfully. Seemingly, we do not have the knack.
I see now why so many young men slip through the cracks in the workplace. They do not understand the demands of work, and bosses have little time and inclination to teach people what it means to work.
Question: How can we do better at hiring and firing?
23 Comments
Tough situation, but very common (at least in small town New England). The adage, “Hire slow, fire fast” seems to work, but it’s not always followed when you’re in “warm body” mode.
Not so very different in the UK Lloyd I am afraid to say they blame the attitude to work on the welfare system but I don’t think that is the real issue.
First off – it doesn’t surprise me one bit. I hear that same story all the time.
I don’t know where you are located but if any kind of urban area at all – $11/hr won’t pay much of a person’s daily expenses. I mean at full time that generates $22K a year. Hardly pays for a commute and certainly doesn’t cover childcare [one reason why so few women apply – not trying to be sexist, just looking at my own family members].
Secondly in most urban areas a person can get a lot more flexible working conditions in ‘services’ – fast food and retail – that pays about as well. Or better if tips included. Health insurance is frequently an issue but if another family member has it already – they are covered. Or if young – just roll the dice.
I realize you have cost constraints and maybe believe $11/hour is all you can pay. I get it and know others in that same situation. But can you better afford to not have those tasks performed at all or pull other, more valuable people off other more valuable tasks, to get it done if it absolutely has to get done?
It is why so many companies I work with either budget for the ‘real market wage rate’ [even for menial tasks] and then pay it to get ‘good people’ instead of trying to force misfits to take the jobs at less than market rates. And the ‘market rate’ isn’t what papers report or some gov’t statistic – its the dollar per hour you have to pay to get good people to apply and then stay on.
Either that or you will have to outsource the tasks to somebody who can pay that rate or walk away from orders that require those tasks altogether. Obviously something you can’t easily do.
I have no idea what we do the the ‘misfits’. But frankly – while that is all of our problems on a societal level – I wouldn’t want it to be my problem on a day-to-day running a shop level. Got enough problem without hiring more.
I wish you the best of luck.
Welcome to the world of millennials, self entitlement, me attitude first and “I am here, so give me what is owed to me”. I believe we all are having the same problems with hiring skilled laborers. They all jump from McDonalds, to Wall Mart to Subway to the shop down the street. You can find the diamond in the rough once in a while and reward them with much better pay but like everything else is short lived. They always seem to jump to whatever else is out there.
One thing that has worked fairly well for me for the past several years; I hire everyone through a temp agency and if the employee really needs or likes the job; after the 3 month period, I hire them with full benefits. Sad to say that about 85% of the ones that come and test the waters at our company; leave before the probation period ends. But is good because you have the time to see their work ethic or lack of.
More reason to have our inept leaders in DC fix our immigration laws; to have a bigger pool of people that really want to work.
When I have similar issues with new young employees I remind them that the sign on the front window does not say “Adult Daycare Center”.
We’ve taken a different approach. We’re not looking for experienced machinists anymore. With the proliferation of CNC and automation, we’re looking for mini-managers. People who are computer savvy, can follow a process, are career oriented, and who are a specific personality type. Yep, that’s right, we do personality testing, and we have a rigorous, confrontational interview that tests the applicants under duress. It weeds out problem children.
When we made the point to local Tech Schools that their approach to certifying CNC Operators wasn’t helping us, it fell on deaf ears. We were asking them to focus on math, and on how the actual contract machining business works. Then to focus on communication and problem solving skills. We can teach them to run our machines.
They roundly rejected what we asked. So we brought a Teacher on staff, and started a curriculum designed to educate new and old employees on what we were looking for in an employee. It focuses on life skills, like credit, insurance, retirement, budgeting and communication for a quarter of the course. It then moves to math skills needed in the environment they will work. Then we move to the history of manufacturing. How did we go from anvils to HMC’s? Finally, it focuses on the core values and philosophy of our company.
They do it on their own time. Local high schools have contributed classroom space, so we do the classes away from the plant. We also bring in high school students to attend who are in our school to work program. 16 weeks, twice a week. We want a strong personal commitment. The focus is on proving that these aren’t Jobs, they’re careers. You can raise a family and retire in these positions if you have a career plan, and goals. These “trades” put me through college, and my father before me.
We’ve recently received a state grant to continue and expand the program, and are offering it to employee’s spouses and adult children as well.
The status quo doesn’t work, and if we’re wiring for the Government to help…. well that’s the definition of insanity. They can’t help themselves. They talk about creating jobs, meanwhile businesses can’t fill positions. It makes no sense.
We need to promote the business. People have a mental picture of factory work as shoveling coal into a blast furnace. When they are educated as to what we really do, they realize it’s not manly-man material. It’s a thinking person’s business, and thinking people make very lucrative careers.
We all have to think outside the box, promote our industry, and focus on the most vital parts of our businesses. Our employees.
I had a similar experience 20 years ago when i was running a sheet metal business. However now that I’m at a college training skilled machinists, I have another point of view. Here are some comments:
– You would probably attract better people if the wage is higher. People working for $11/hour, unless they live with their parents, will be marginally homeless.
– The candidates that offered you insight into their aspirations had dreams that did not include your company or the jobs they are doing for you. They were never going to be anything but short term.
– You might raise the wage and instead of hiring for this position hire people who through training can eventually take higher skilled positions. Give them somehting to aspire to.
Just a few thoughts.
Really sorry to hear the story and follow-ons. Thought workers in Midwest had that “midwestern work ethic”. Perhaps true when we left Chicago in 1972. Not much better out here in California, I’m afraid.
Lloyd,
The reality is that 98% of laborers willing to work for $11 per hour need constant supervision. To keep laborers that can be counted on to get the job done with less than constant supervision in our area costs between $16 and $20 per hour, or possibly more in your area. We like to start them at about $13 or $14 and then move the keepers up to a full pay over the next 3 or 4 months. When you consider the lost time and efficiencies of poor employees, a few dollars more in salaries for the keepers is money well spent.
It’s easy to look at the younger generation and say they have no work ethic, but a lot of younger folks haven’t had the opportunity to work for their necessities yet. Growing up, I was expected to contribute from an early age, with a paper route, with door to door magazine subscription sales, mowing lawns, etc. The work ethic isn’t something we are born with, it has to be learned. A friend of mine has a large job shop in this, mostly rural area, and when I asked him where he got the workers for his machines, he said, “I look for people who grew up on a farm. They learned early on the value of work and they don’t call in sick.” There may not be many farms left in the chicago area, but I bet there are plenty of people who started paying their own way at a young age.
Lloyd,
Thanks for your informative and useful report.
A minor comment: $700 in petty cash seems like a lot to me. I guess you buy more than donuts with that.
Hi Lloyd,
I don’t get too much joy out of reminding you who you voted for in the last election.
Maybe someone with a business background would have seen that the problem is not with the people but the systems, starting with education, that must be replaced (with something like the education system in GERMANY that fosters testing folks to ensure that those who cannot be rocket surgeons learn a trade or Beruf) Until one becomes a Meister one does not expect to make much Eurowise. Maybe you shouldn’t hire employees but convince folks – like at NBC – that they are unpaid; pages, trainee, apprentice whatever term has the most status.
You know I find it curious that so many wanting to learn will gladly pay colleges or even welding schools just so they can get a piece of paper that will supposedly force you to pay them more money. I can teach a twelve year old kid to weld in week…..ooops forget I said that. I did not teach my kids to weld when they were twelve….they were around ten!
As usual respectfully submitted….C. Smith / Jacksonville Florida
Hey Lloyd
I am retired from a union trade that has a starting rate today of just over $20 per hour plus some benefits. There is a 6 month probation period, and then full benefits and a raise on acceptance after the probation. The new hire can be let go without reason in that 6 months. But let me tell you, even that isn’t a guarantee of a good worker. I eventually came to hire only people that did not currently have a job, with the emphatic explanation to them that if they couldn’t, or sadly wouldn’t, tow their own weight SAFELY, they would be back in the same situation very quickly (no job). Nonetheless, none of that was any kind of a certainty on finding “good people”. We kept less than 30%. Some were right out of a college with a specialty diploma well suited to us. Some were just laid-off from some other trade. We found the best was to ask the best of our current guys if they had anybody in mind, and that worked pretty well. Nothing like having your father or brother or some other family member on your ass all the time!! Still there is no easy way to determine ahead of time if any particular candidate will still be with you after 6 months, even with those incentives.
Keep trying. Good luck!!
We can commiserate! Finding good people is hard but lately we have discovered that recent Veterans make excellent employees.
The military training and experience often do instill a much better work ethic, team work understanding and skills. Especially those who advanced above private or continued on in the reserves or National Guard.
I feel like we owe these men and women something for their service to all of us….hiring and giving them the opportunity for rapid advancement in job position and pay is our way of giving something back!
Hire people with a Military background and an excellent attitude. Then train them. They will be eager to learn, and will have a great work ethic.
Next, get rid of Welfare in it’s current form, so people are incentivized to work, not sit home playing with their phones and Xboxes while taking $40K a year from Taxpayers.
To significantly reduce the number of people on welfare you need to start with paying a living wage. At least $15/ hour. There are to many hard working people getting a paycheck not making ends meet. They too end up in the welfare system. Lloyd you gave your $11 an hour employe the opportunity to steal a 3.2 percent raise from you.
A $15/hour minimum wage?
Hello from Texas!
Your problem is pretty well nationwide, apparently. While we are having better success at creating jobs here than some areas of the country, we also are having our share of problems finding good employees. In our area, seems that a great many of the mechanically inclined, who don’t mind getting dirty and sweating a bit, are all gone to the oilfields, or are thinking that they should be paid for not going there at least.
However, at $11 an hour, your very close to where we try to start entry level employees. Or where our top end management wants to start them. I’m in mid-level management, and looking at $11/hr, I’m reminded that you get what you pay for, and $11/hr isn’t going to get you much. They can serve burgers at the local burger chain and get that, better if they can get insurance. It’s a tough line to make work. Your margins are pinched by what your customers want to pay, but you have expenses going in that limit the amount of cost cutting you can do at the input end.
I’m currently looking to replace at least two, maybe three positions. Two just quit. One was let go a good while back. The two that quit were both recently reprimanded/written up, basically for doing such a crappy job that it just couldn’t be overlooked anymore. When you dumb down a job to where any warm body can do it, and then they progressively get worse by the day, till the point that they are not even the warm body isn’t paying his way, what more can you do. Attitude is SOOOOO important. And these guys just didn’t have it anymore. Started out well, both of them, than got lazier by the day after their probation ended.(90 days)
Interviewed my first potential female shop helper?operator candidate yesterday. Fortunately, she took one look at our parts and pulled herself out of the process. She was smart enough and realistic enough to realize that lugging 50 lb castings into and out of a CNC lathe is not what she wanted to do. A shop with more manageable sized parts might work out for her, but not here. And once the interview was instigated, I couldn’t legally just tell her that I didn’t think she’d be happy heaving those parts round all day. I’ve had healthy, able bodied men that bailed after less than a day of that.
Recently hired a young Marine reservist. He’s working out well. heaving those parts around is actually building up his upper body strength, Marine Corps got to like that. Country boy to boot, so he’s got a good work ethic. Eager to learn, and quick to learn. Need some more like that.
Then I had a young fellow come in with loads of schooling and school related honors in the local High Schools drafting and Engineering classes. Went to a community college for some more of that. Honors there too. He’s been helping his dad, doing architectural drawings and carpentering, but he’s more interested in learning mechanical engineering, and how to actually MAKE some things in a Machine Shop. I’ve recommended that we hire him if we can. For however long we can keep him. Unless I miss my guess, he’ll learn some CNC ops( already has a little bit of VMC operator time under his belt), then move on to the big city and something that shines better for him than cast iron and clutches. But we’ll get some use out of him for a while, and who knows, maybe I’ll be past my retirement threshold by the time he flies.
Cleaning machines is a crappy job.
I’ve done a lot of it for myself in my own shop over the years.
Doing it for someone else for $11 in this day and age
is unthinkable. What do you expect? That level of crappy work for $11/hr?? Sounds to me you’re looking to get out of it cheap…..bump up the pay to at least $15 and then maybe you’ll get luckier in your search…
Hopefully you provide coveralls, gloves, etc. to your workers so they can at least stay reasonably clean in the process. It’s a dirty thankless job, pay them accordingly
and make it as bearable as possible.
Seattle has passed a $15/hr min wage to be phased in over the next few years.
It’s hard for me to imagine that it’s really any cheaper to live in Chicago.
I find minimum wages dubious policy, but I also find the thought that you could reliably get people to do nasty work for $11 an hour rather a stretch.
A real problem in the current economy is that there are more and more two types of jobs – high skill jobs that pay well, and lower skill jobs that pay poorly. BUT the lower skill jobs still require certain human attributes (otherwise you’d use a machine or robot) and those *attributes* have a kind of “floor price” – that is, nobody who is reliable at anything will be happy at $1 per hour. In some sense, there are two wage markets afoot here – the market wage for people to blast gunk off machines, and the market wage for competent people – where competent means they show up, have appropriate responses to workplace circumstances, don’t normally make utterly daft mistakes, and so on. You will find that these people are hard to keep until you get your wage rage over the hourly rate for “general competent person”.
The poster above who talks about wanting computer and math savvy people, rather than people who remember what G857 does, is onto this. The computer savvy person can look it up on their ipad, do the math that says “uh, that’s a net loss”. That’s a “competent person”. The “expert” who remembers all the specifics of some controller but can’t grok cost per hole versus cost per tool is not actually very helpful.
By the way, there are industries like software that pay Very Well Indeed for key people, and in spite of sometimes stunning compensation, still struggle to find people.
We start our lowest paid workers, who deburr aluminum parts, at $12-$13 per hour. This is in Central FL where wages are historically low and cost of living is also low compared to Chicago or any big city. Many wont work for this when they find out they actually have to work. I dont think $11.hr in Chicago or any real city is going to cut it. You might buy some pill heads for that, but expect them to steal everything they can, take a half a shift in breaks per shift, and work slowly when they do work.
We have the most trouble getting skilled machinists and programmers. Any that are really good want to start at $40-$50 per hour. Even at high wages, It is still hard to find machinists that can do what they think or say that they can do when we hire them.
Hire Mexicans, problem solved.