Today’s Machining World Archive: May 2006, Vol. 2, Issue 05
Shave and a Hair Cut Two Tenths
No matter how new or state-of-the-art your screw machine is, sometimes the finish and accuracy it produces are still not acceptable for your job. Shaving overcomes the two main causes of variability on the diameter of screw machine parts, infeed error and spindle index error. It overcomes infeed error by feeding past part centerline, and it overcomes spindle index error by floating on the part. On any type of screw machine in good condition, shaving will yield diameters that are round and on size within +/- .0005. Jim Barnette, shop foreman at Graff-Pinkert & Co., who has successfully used shave tool holders for over 30 years, recommends the following approach for setting a shave tool.
How to Set a Shave Tool
1 Determine whether shaving is necessary by running 20 pieces off of each spindle of the machine and then measuring the accuracy of each piece using a micrometer (See A). If you determine that your present finish is unacceptable, employ a professional tool maker to build the proper shaving cutting tool to meet the specifications of your print.
2 Once you have the proper cutter and roll, make a blank with the exact dimension needed, on a lathe. On a workbench, slide the blank between your roll and tool, then preset the distance between them to achieve the perfect fit (See B). Many people use dial calipers to measure the distance between the roll and tool instead of making a blank. If you decide not to create a blank, you must use trial and error on the machine to achieve the correct accuracy. Making a blank will save time and material, and you can use your blank as a reference for future jobs.
3 With a depth indicator, measure the depth from the top of the holder to the base. Set the dimensions equal on each side. Make a scribe line on the back of the shave tool to show the taper line (See C). This will enable you to reset the tool at a later date without having to use a depth micrometer. Remember to save the roller, cutter and blank. Always take a measurement from the tool when the machine is in the back position (the farthest stroke before it indexes). Measure from the point of the tool down to your bar to see if you are on center.
4 The shaving tool must be positioned in the shaving attachment so its cutting edge is in line with the center of the roll (See D). This is accomplished by clamping the shaving tool in the shaving attachment, so the cutting edge is in line with the face of the attachment. Use a straightedge to line the cutting edge with the face of the shaving attachment. Slide the blank between your roll and your tool to get the perfect fit.
5 Mount the roll block on the shaving attachment. Using the roll block adjusting screw, adjust the position of the roll block, so the distance between the roll and the cutting edge of the shaving tool is exactly the same as the finished size of the part.
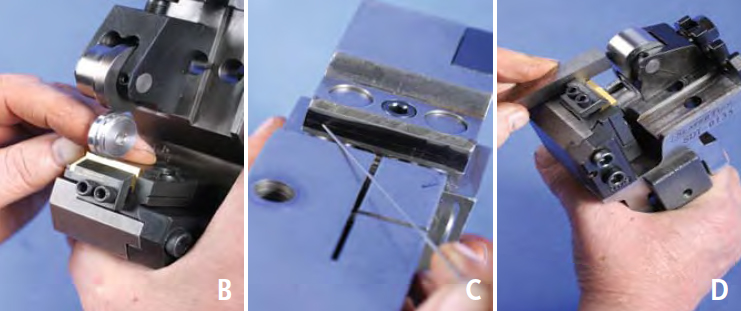
6 Mount the assembled shaving tool and attachment on the cross slide and position the tool laterally, relative to the work piece (See E). Clamp the shaving attachment in place. Using the cross slide adjusting screw, move the shaving tool, shaving attachment and cross slide toward the work piece slowly until the roll contacts the work piece. Continue advancing the cross slide until the cutting tool is drawn to within .010 of the work piece.
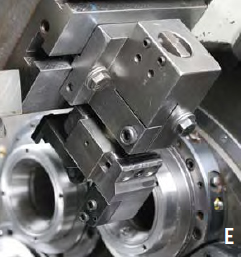
7 With the feed disengaged, run the main drive motor so only the spindles rotate. While the bar stock is rotating, use the cross slide adjusting screw to slowly move the cross slide toward the work piece until the shaving tool and roll reach the centerline of the work piece. The tool has reached the centerline of the work piece when further advancement of the tool fails to produce any chips. A mirror can be helpful to observe the chips being cut as the tool is advanced. Limit the travel of the tool beyond the centerline to the absolute minimum. Then, tighten the cross slide locking screws in place. Before proceeding, you must always check the clearance between the attachment and slide.
8 Jog the machine to be sure the work piece clears the shaving attachment and tool when the machine indexes. Finally, measure the OD of the test part and adjust the roll block with its adjusting screw as necessary. If you do presets, you will save a lot of time and material during your shave tool setup.
1 Comment
Solid information. For my $.02, I simply use a pin gage, sized at desired shave diameter, to gap the holder (pre-setting of distance between roller and top of tool).
Then I remove the tool, apply bluing to rub face, and set aside. Then I install holder and advance slide forward, either eyeballing or dial indicating rise of roller onto workpiece to establish on-center condition, preferring to go past center a bit. I also ensure proper amount of roller contact at this point. Then I simply install shave tool, check lateral position, and make a test cut. Removing tool, I can “read” amount of bluing removed from rub face, and dial in center via slide adjustment.