Today’s Machining World Archive: April 2008, Vol. 4, Issue 04
For thousands of years, humans have made decorative and useful objects by melting metal and pouring it into molds. Now, industrial casting processes are available to produce a variety of complex parts economically in different metals.
Sometimes cast parts can be used in the form they leave the mold. Often, they need to be machined to provide sealing surfaces or threaded holes. In the machine shop, cast parts can present challenges. To machine them, it helps to know about the casting process and the physical characteristics of castings, so you can adapt your machining practices accordingly.
In any casting process, molten metal fills a cavity the shape of the part you want. When the metal solidifies, it has taken on the shape of the cavity. The various casting processes create the cavity in different ways and use different methods to introduce the metal into the mold.
As an introduction to casting and machining cast parts, this “How It Works” covers aspects of aluminum castings, including four common casting methods, and information about machining cast aluminum parts. Many of the principles and processes apply to other metals, as well.
Sand casting
In sand casting, special casting sand is compacted around a three-dimensional pattern, which forms the part cavity and the channels through which the metal will flow. The pattern is removed and the cavity remains. The mold is made in two halves, called the cope (top half) and the drag (bottom half). Where they come together is called the parting line. On the cast part, you can usually see where the parting line is.
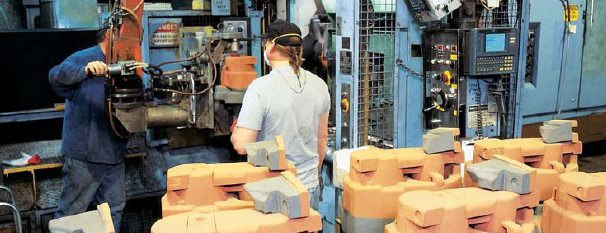
If the casting needs to have hollow sections or holes, one or more sand cores are set in place, usually in the drag, fitted into grooves left by the pattern. The cope and drag are married together and the metal is poured. It cools, sand is removed from the outside of the part, and the cores are broken up and removed. The surface of the part picks up the texture of the mold, which may be fine or coarse, depending on the sand used. Cost is relatively low, and, depending on the part, sand casting may be used for any production quantity.
Die casting
Die casting is done in a reusable steel mold, or die. It is the fastest of these casting processes. Molten metal is forced at high pressure into the mold. The mold is cooled by air or water until the part is solid and can be removed. Cycle times of a minute or less are common. Die casting is suitable for quantities that are high enough to make the cost of tooling worthwhile. It can produce thin wall sections and yields parts with a good surface finish. Porosity can be an issue.
Permanent and semi-permanent mold casting
Permanent mold casting also uses a steel mold, but the metal enters the cavity by gravity, or at low pressure and/or under vacuum. The cycle time is slower than for die castings, often three to five minutes. Movable metal cores can provide holes or internal passageways. “Semi-permanent mold” casting uses sand cores to provide holes and hollows in the parts. Parts have a good surface finish, and often have better mechanical properties than die cast parts.
Investment casting
Investment casting, known as the lost-wax process, uses patterns that duplicate the final part, made from wax or a similar meltable material. Patterns are attached to a gating system made of wax, then the whole assembly is coated with a ceramic slurry (fine particles suspended in a liquid) in several layers and dried to create a shell. The wax is then melted out of the shell. Metal is poured in. After it solidifies, the mold is broken and removed. Investment casting can produce netshape or near-net-shape parts with excellent surface finish.
As with any manufacturing process, there are trade offs – production quantities, part size and complexity – in selecting which casting process to use, said Alfred Spada, director of marketing, public relations and communications at American Foundry Society, Schaumberg, Il.
Not the same as bar
Castings bring a degree of difficulty to the machining process. If you are accustomed to machining nice, clean, precise bar or other dimensioned stock, castings may surprise you.
“The main difference is, if you start out with bar stock, you know what you’re getting – tolerances of maybe a couple of thousandths of an inch,” said Lanning Brandel, president of AMT, Inc., Sharon Springs, N.Y., a producer of ferrous and non-ferrous precision investment castings. Even on investment castings, which tend to hold tight tolerances, they are likely to be in the neighborhood of a few thousandths per inch.
On a six-inch aluminum sand casting, the foundry will likely be able to hold tolerances of +/– 0.010” to 0.020”, and there may be a mismatch across the parting line, where the two halves of the mold come together, of up to 0.020”.
Two-part molds will produce a visible parting line on the casting. Often, the part is designed so this parting line is on a surface that will be machined. If it will not be machined, and the parting line is intrusive, it will be removed with a belt sander.
Metal may leak out between the mold halves, producing flash on a part. For die casting processes, an automated trim press may be used for cleanup. Sometimes this may cut into the part, or sometimes fold over the flash rather than remove it.
Location, location, location
An as-cast part will not have a nice, flat surface to seat on the machining center table, or a close-to-perfect diameter to hold on to. You have to figure out how to hold the piece, and you will have to gage off of locating surfaces incorporated into the design. These are surfaces or features built into the casting, left as-cast, and indicated as target or datum locations on the drawing. You will use them for initial setup in the machining center.
Locators should be on the same half of a two-part mold, usually the drag. “The worst is taking your machining locators across the parting line,” said Tom Prucha, vice president of technical services at the American Foundry Society. That way, any cope/drag mismatch would add to the other tolerances.
Once you mount the part in the machining center, you can also use a touch probe to pick up selected features and to give the correct offsets to the machine control.
“In general, you would like to start by locating at a surface that won’t be machined,” Brandel said. Pick up three locating points and make sure the print indicates where they are and notes that they should be left as-cast and not be damaged, ground or machined.
Hold on
Workholding for castings can also pose a challenge. Without the right fixtures, a part can easily be misaligned. However, you don’t want your fixturing so tight that it requires the locators to be pristine, said Prucha. With cast parts you need to take the tolerances into account, and can’t depend on the features being perfectly flat or perfectly smooth.
“I can’t emphasize enough having quality-built fixtures” to hold castings during machining, said Mike Stahl, sales manager, Olson Aluminum Castings, Rockford, Il, manufacturer of high-end commercial and industrial grade sand castings. “It’s well worth the few dollars up front to have dedicated fixtures.”
Machined surfaces
Creating a quality machined surface on a cast part isn’t just between you and the metal. It’s a team effort that includes you, and the foundry, and your customer.
The areas you finish machine need to have enough metal for you to remove the entire cast surface, allowing for the tolerances of the casting. The foundry needs to make the part selectively oversized to provide enough material so you can machine over the whole area. This additional material is called the “finish allowance” or the “machine stock.” If there isn’t enough machine stock, after you’ve run the cutter over the surface, some as-cast surface may remain, and you will have to scrap the part.
Porosity inside heavier sections of die cast parts can be an issue, so you won’t want to cut into them too deeply.
Fortunately, die casting holds tight tolerances, in the range of a couple of thousandths, so with a properly designed casting, you don’t need to remove much material, and can stay clear of the porosity.
Other types of castings may also have porosity problems, so when you cut into the piece, pits show in the surface. You can work with the foundry to remedy the situation, or, if necessary, you can convince your customer to find another foundry that can produce better-quality castings.
Hard to tell
If you look at the Aluminum Association specs for 356 aluminum, a common sand-casting alloy, said Stahl, you’ll see a wide range in the Brinell hardness spec. Particularly with aluminum, the hardness affects machining qualities. Maybe last month’s lot of aluminum castings worked fine, but you now are having trouble machining this month’s shipment. The aluminum tears and smears and won’t make clean chips. Check the hardness, he suggested. You will probably find it is softer than last month’s shipment. A casting supplier that carefully controls the alloy formulation and does its own heat treating will be able to provide you with parts that will machine the same from one lot to the next.
In the middle
“There seems to be a lot of ‘matrix buying’ out there,” said Stahl. The customer will source a low-cost casting supplier and a low-cost machining supplier, and put them together. The machine shop then may have a problem.
“You don’t know what will come in. Where are the datums? Where is the parting line?” said Prucha. “Usually none of that information is conveyed.” Porosity and inconsistent hardness may degrade the finish of the machined areas.
As a result, your customer may blame your shop for problems that originate in the casting. You may be able to work with the foundry to improve the situation. If not, you may need to push back on your customer to source better castings.
Start at the very beginning
When you are going to machine a casting, it’s a good idea to begin communicating with both your customer and the foundry as early as possible.
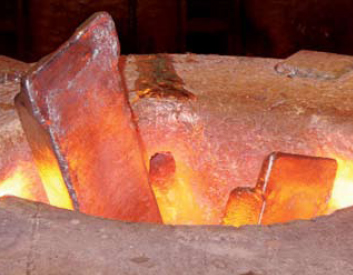
Try to get as much information as you can up front, said Stahl. “Even an hour talking about [the part] will save time down the road.”
“The most important things are the surface finish [of the] castings, and the tolerances,” said Brandel. “And [you] need to look at the parts and see how much of the part can be used as-cast and how much needs to be machined.”
The design of the casting is critical for providing good flow and fill characteristics for the foundry, and providing you with useful locating features and sufficient machine stock. If there’s not enough machine stock designed in, you’ll be scrapping parts after you’ve invested machining time into them.
Clear communication with your customer and the foundry will help provide you with the good castings you need to start with. “You can’t machine quality into a casting,” said Stahl.
Ready to cut
The foundry should have thoroughly inspected the castings`before shipping them. However, you would be wise to do your own inspections, too, before putting castings into your machining center. You may want to check the hardness, especially for aluminum parts. Make sure the locating features are intact. They should not have been ground, knocked off, dinged, dented, or otherwise damaged.
Look at the cast surface. The overall roughness should be uniform. Note any rougher patches or protrusions.
If the part is from a metal mold process, look for indentations from the ejector pins used to push the part out of the mold, and see if there are any areas that were scraped during removal from the mold.
Working with castings is definitely different from cutting bar stock. To save yourself headaches and keep your customers happy, work with the foundry to get good castings to start with, and keep in mind the special requirements for machining cast parts.