Today’s Machining World Archive: May/June 2009, Vol. 5, Issue 05
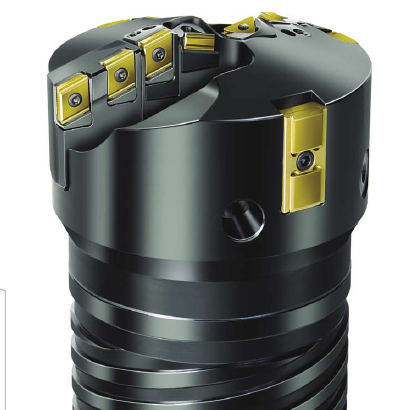
To dig a 35-foot-deep hole, you need a 35-foot drill.
You’re probably accustomed to drilling holes with depths up to, say, five times their diameter, or maybe, with the latest special drills, up to 15 or even 20 times diameter. But what if you have a customer who gives you a print for a foot-long part with a quarter-inch hole all the way through 48 diameters? Then you’re getting into deep-hole drilling.
A deep hole has a depth-to-diameter ratio of more than 20. It could be 1 mm in diameter and 2″ deep, or a 6″ hole that’s 35 feet deep. One hundred times diameter is commonly done. Depths of 200 to 300 diameters are achievable, said Ed Kays, president, Kays Engineering, Marshall, Mo., manufacturer of DeHoff and Eldorado deep drilling machines. It takes some effort, but is not unheard of; it’s just paying attention to details, he said.
Though many consider it a mysterious process, deephole drilling is still metal cutting. But it poses unique challenges. It requires special tools and in many cases, special, dedicated machines.
Gun Drilling
For a smaller diameter hole like a quarter-inch hole a foot deep, you should use a “gun drill.”
A common type of gun drill consists of a shaft with a V-shaped groove, or flute. The cutting oil or fluid is fed through the tool to the cutting edge and exits through the V-groove, carrying the chips with it. Gun drilling is commonly used for holes in the range of 0.5 mm (about 0.020″) to two inches diameter. To help keep the drill straight, you would use a drill bushing to guide it into the part, or provide a pilot hole.
Gun drilling was invented more than a hundred years ago to provide straight, precise gun barrels. It is suitable for holes from about half a millimeter (about 0.02″) to 2″ in diameter. Hole depths can be 100 diameters or more.
A gun drill, by its geometry, limits the area available for cutting fluid flow and chip evacuation. Typically the cutting fluid passes through one or two holes in the shaft of the drill. It exits through the V-groove, which is usually 20 – 28 percent of the cross-sectional area of the drill, says Tom Swansiger, vice president, Technidrill Systems Inc., Kent, Ohio, manufacturer of deep drilling machines. You might need 1 horsepower (hp) for cutting, but perhaps 5 hp to pump the fluid at pressures in the range of 300 psi to 2000 psi.
Dedicated gun drilling machines are available, but gun drills can also be used on conventional machines, as long as the cutting fluid pressure and flow rate are sufficient. For example, Swiss type automatic screw machines can easily incorporate gun drilling. Typical applications include hydraulic system components and medical devices, such as bone screws, said George Bursac, general manager, Star CNC Machine Tool Corp., Roslyn Heights, N.Y., manufacturer of CNC Swiss type automatic lathes. Though gun drilling tends to be a slow process, a Swiss machine can perform other operations while the gun drilling is going on. It’s a very efficient way to get the job done, he said.
Gun drilling is perfect for some applications, but to handle larger diameter holes and provide faster cutting speeds, you’ll need a different type of drilling system.
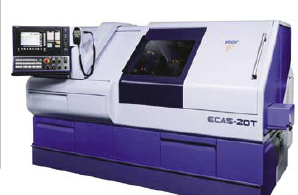
BTA or Single Tube System
In the 1930s in Germany, a new technology was developed for deep-hold drilling to handle larger sized holes, called a “single tube system” (STS) or BTA system (for “Boring and Trepanning Association”—see also “trepanning,” below).
The BTA drill consists of a drill head, a drill tube, a fluid induction unit and associated fittings and supports. The drill head has cutting edges (often indexable inserts) and passages for the cutting fluid to flow through. In addition, the head has guide pads, which ride on the newly cut ID of the hole and help keep the drill going straight. The drill head is mounted to a drill tube, which acts as both the shaft of the drill and a return conduit for the cutting fluid and chips.
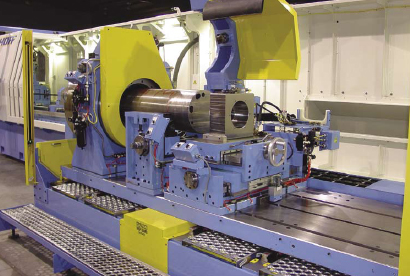
In a BTA system, cutting fluid comes in through a fluid induction unit that seals against the face of the part. This unit also functions as a drill bushing to support and align the drill. The fluid flows in through the space between drill tube and the ID of the hole. In the cutting area the fluid picks up the chips and then flows back out through openings in the face of the drill, exiting through the inside of the drill tube.
BTA drills are used on dedicated deep-hole-drilling machines, which provide the necessary spindle horsepower and high-pressure/high-volume fluid flow. BTA systems are typically used to drill deep holes from about 5/8″ to about 20″ in diameter, said Jim Rose, president of Botek USA Inc., Roselle, Ill., a tool manufacturer.
This type of system will drill five to six times faster than gun drilling, said Mark Sollich, president, BTA Heller Inc., Troy, Mich., a tool manufacturer.
Ejector, or Two Tube System
The “ejector,” or two-tube system, was developed by Sandvik. It does not require a dedicated deep-hole machine and can be installed on a lathe or other horizontal machine, such as a boring mill or machining center. Two concentric tubes carry the cutting fluid and act as the drill’s shaft. The cutting fluid flows into the part between the inner and outer tubes. At the cutting area, it picks up the chips, and then carries them out through the inner tube. A unique feature of an ejector system is that some of the incoming fluid flows out through a venturi arrangement, which produces a suction effect to help evacuate chips and cutting fluid from the drill.
Because an ejector system can be retrofitted onto an existing machine, it offers a relatively low cost way to provide deep-hole drilling.
Trepanning
Instead of making a hole by cutting all the metal into chips, trepanning (pronounced TREE-panning or treh-PAN-ing) removes a solid core of material by cutting around it. This is an advantage when cutting expensive alloys, as the solid core can be used to make other parts, or, if it is recycled, is more valuable than chips. The trepanning head is completely hollow, and the cutting process is similar to the BTA/single tube system, but it requires less spindle power, as it cuts less material at each revolution. Trepanning is more common for drilling larger holes, 6″ in diameter and up, said Jeff Price, sales manager, Entrust Tool & Design Co., Inc., Menomonee Falls, Wis., manufacturer of Unisig deep drilling machines.
A Black Art?
Deep hole drilling has a reputation of being a mysterious process. It is cutting metal, the same as any other machining process, but it poses plenty of challenges. The cutting is going on where you can’t see it—it could be 10 feet or more inside the workpiece. Experienced operators can detect problems or changes in the process from subtle changes in sound. Load monitoring is widely used to quickly alert operators to problems.
“We’ve been doing deep hole drilling for a long time,” said Ron Klas, plant manager, Carlson Tool & Manufacturing Corp., Cedarburg, Wis., a shop specializing in deep hole drilling. “And there are a lot of tricks to it, like grinding our own gun drills to get them to do what we want.”
Deep-hole drilling is not a black art. It’s not different from any other machining. “People just don’t know a lot about it,” said Kays. It’s the same combination of man, machine and equipment as other processes. You need to have “good equipment, good tools and pay attention to details,” Kays said.
“The machines and the tooling go a long way toward making the process work,” said Sollich, but “it is an art, and a good operator can make or break your process.”
Price pointed out that there is no place to learn how to do deep drilling except on the job. “If we could ship an operator with each machine, we could sell a lot more of them,” he said.
Chip Control
It comes down to chip control, said Klas. Cutting metal is cutting metal, even if you can’t see the tool or the chip. The critical part of deep hole drilling is getting the chips out of there. Different technologies have been developed to take care of accurately cutting the metal and effectively evacuating the chips. If you don’t get the chips out of there you’ll ruin the tool and the part.
At startup on a new part, or even a new piece, said Sollich, the operator will start with the recommended feed and speed. Meanwhile, a helper stationed by the chip exhaust port catches chips in a strainer. Depending on what the chips look like the operator makes small adjustments to produce chips that will flow well, increase feed or reduce rpm if the chips are too long, or increase the rpm to thin out the chip.
If even one chip gets stuck in the drill throat or elsewhere, it can cause a logjam of chips. The drill heats up, the piece is ruined and you have to take out the drill and dig out the chips.
So chip control is critical, and for every part you have to dial in the feed and speed to make the chips the right size and shape. Small changes in feed and speed can mean the difference between success and disaster.
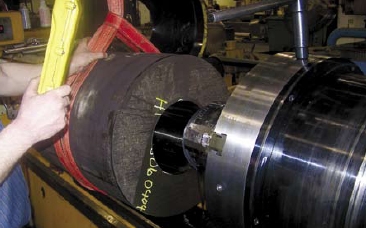
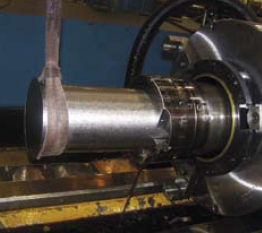
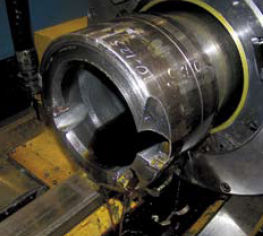
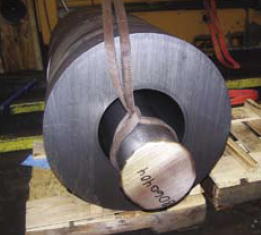
Holding Tolerances
When drilling normal holes, drill wander is not usually an issue. However when you are drilling deep holes, even a little bit of deviation adds up. You can expect to hold tolerances like these for the hole’s variation from centerline:
– Rotating tool/stationary part: 0.001″/inch
– Stationary tool/rotating workpiece: 0.003″ – 0.005″/foot
– Tool and workpiece rotating in opposite directions: 0.001″ – 0.003″/foot
If the dimensions and location of the deep hole are critical, as they often are, you have to make accommodations. One approach is to drill a slightly undersized hole halfway from one side of the part, and halfway from the other, and then use a special counterboring tool designed to be pulled through the part. If the hole location tolerance is extremely tight, you can drill the hole in the raw stock and then machine the rest of the part based on the hole location.
Drill vibration may harm tolerances and surface finish, so it is important to support the long drill to minimize this effect. The rule of thumb, Kays said, is you need to support the tool every 40 diameters, so for a 0.25″ tool, you’ll need a support every 10 inches, or closer for higher feed rates.
Applications
Of course, gun drilling and the other deep-hole technologies are still used for making barrels for weapons, from small firearms to the giant guns mounted on battleships. And from there, the applications for deep holes diverge in every direction. Some examples:
• Aerospace: hydraulics, landing gear components
• Automotive: crankshafts, other components— lubrication holes
• Oil drilling: long drill tubes, other parts for downhole applications
• Earthmoving equipment: wheels, hydraulics
• Marine: large propeller shafts, drilled out to save weight
• Medical: bone screws, dental and surgical instruments
• Metal processing: heavy-wall or non-standard tubing made from bar stock, custom diameters reamed in standard tubing.
• Plastic molding: machines and molds—heating/ cooling liquid passages
• Power generation: heat exchangers, boilers
Bringing Deep Hole Drilling In-house
You can always subcontract out deep drilling to a shop that specializes in it. If you find you are getting a lot of requests for deep holes, or think the capability will benefit your business, consider making the investment for in-house production.
The ability to drill deep holes can add value to your offerings and make your shop unique, said Price. “Regardless of the region of the country, there is a need for deep hole drilling. If you can fill that niche, it’ll generate work for the rest of your machining operation.”
“We’ve had more than one person buy these machines to generate work for their turning machines,” said Price. Doing your own deep drilling can shorten delivery time, he said, as turnaround time for sending out parts for drilling might be three to four weeks turnaround at a busy specialty shop.
Even a smaller machine capable of drilling a 2.5″ hole 60″ deep could do the trick, Price said. Bear in mind that the cost is much more than a lathe because there’s a lot more horse power, he said, and the necessary high coolant pressure and flow rate add cost.
An ejector, or two-tube system, can be retrofitted on a lathe, horizontal boring mill or other horizontal machine. This is not a simple or inexpensive process, as the system requires a high-horsepower spindle and its own high-pressure/high-flow coolant system in addition to the drill tooling. However, installing a retrofit ejector system would be far less costly than acquiring a dedicated deep drilling machine, said Curtis Cole, drilling product specialist at Sandvik Coromant U.S., Fair Lawn, N.J., a tool manufacturer.
As of early this year, the deep-hole-drilling machine manufacturers interviewed said their business was good. Deep holes require special equipment and expertise, but the capability for drilling them could give you another value-added service to offer customers in industries that are still showing growth in these difficult times.