Today’s Machining World Archive: February 2007, Vol. 3, Issue 02
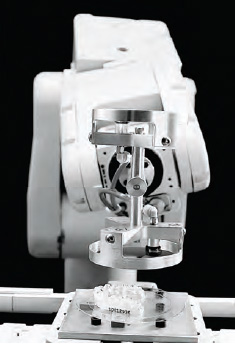
Today, in a factory in Juarez, Mexico, a machine will manufacture a lot size of one. In the time it takes a robot to lift the product off the conveyor belt, the machine will manufacture another lot size of one.
By the end of the day, this otherwise ordinary factory in this bustling industrial park will fi nish some 26,000 single lots, bringing $200 million in annual revenue to Align Technology Inc.
Align’s product:
Invisalign Braces, mass produced just for your mouth.
“We’re making a bunch of unique things over and over again,” said Len Hedge, Align Technology’s vice president of operations. “The process is not that much different. The technology that supports it is not that different. It’s, ‘How do you accommodate the unique individual features of each product?’”
Align is at the forefront of a new age in manufacturing, one that blends the individual specifications of traditional cottage industry with the mass-production capabilities of the post-industrial age. It exists thanks to advances in three-dimensional computer technology, technology that may upend contemporary models of manufacturing just as advances in two-dimensional technology did in entertainment.
In entertainment, companies such as Amazon.com saw in emerging two-dimensional
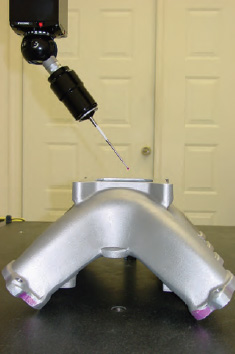
technology the potential to market to individual niche tastes. Few need a reminder how well Amazon.com fared with this idea. As author Chris Anderson points out in The Long Tail, the book coining the niche-marketing phenomenon, the strategy worked because it tapped into the consumer’s innate desire to fi nd a product to his own liking. As a result, consumers became what he calls “active producers,” driving what companies would make available, instead of the other way around. These consumers are, he writes, “a force to be reckoned with.”
The founders of Align observed that the same phenomenon could apply in the material world; emerging three-dimensional technology would allow products to be designed to fi t the individual’s unique physical shape. The two Stanford Business School students – one of whom was wearing a retainer and noticed his teeth shifting – recognized that graphics software could be used to design the multiple stages of plastic liners.
Only in the last decade have software companies tackled the problem of how to program a computer to perceive depth. What comes easily to people is overwhelmingly complex for machines. Engineers have used Computer Aided Design software since the 1960s, but, as its name suggests, it merely aids the human drafter.
Companies such as Geomagic, in Research Triangle Park, N.C., have now made it possible for a computer to render a 3-D image directly from a laser scan. The software triangulates thousands of points, mapping the locations between and among shapes and spaces. The digital image can evaluate a surface for defects; input to a machine to directly build a 3-D object; or simply store an image for posterity. Digital imaging is used, for example, to preserve the exact shapes of ancient artifacts.
Plastic-braces liners have been around since the 1940s, but a craftsman had to saw each tooth from a mold, then adjust and re-wax the teeth in position for all 20 sets of liners. The technique was laborious and rarely used. With 3-D software, the changes are made digitally and still allow for an intricate range of movement.
Align has created a largely digital production system. It e-mails the orthodontist’s dental images to a facility in Costa Rica staffed by 500 English-speaking dental technicians. They use an automated program to digitally realign the teeth in stages and confer with the orthodontist, who is e-mailed a 3-D image of the process. Align uses stereo-lithography to build the molds directly from the computer, but originally cut liners the old way – by hand-laying a sheet of heated plastic on the mold to cut. The company developed its automated “one-lot” system.
“The back end of the manufacturing process was almost an afterthought,” Hedge said. “That’s probably an overstatement. But it was a secondary problem to be solved.”
Align’s technology sidesteps the pitfalls of sequencing through a system of identifi cation. The conveyor-belt tool reads the label on each mold as it slides into place. The tool’s computer then locates the corresponding fi le, then carries out the prescribed cut. The company does not release cycle times, but says there is no perceptible lag.
“Their assembly line is 300 times more efficient than Nike’s,” said Ping Fu, CEO and founder of Geomagic, which provides imaging software for Align. “I told them you will make history: the first company that makes mass customized products. It’s as important as the Ford assembly line.”
Mass customization can mean different things. Anyone who has bought a Dell laptop or ordered at Starbucks has enjoyed the have-it-your-way marketing strategy that lets people customize a product from a palette of options. (If you’ve ever been frustrated in line at Starbucks, take heart: It’s said there are 19,000 possible combinations.)
But Fu’s definition is a custom build of one, as Align has done. Its liners are not assembled from a pre-selected pool. There really is only one of each. Align’s number of variations is limited only by the size of the population. Since launching in 1998, Align has essentially manufactured more than 21 million different products.
“This really is the future, and are we there? Probably not yet,” said Frank Piller, a research fellow at MIT’s Sloan School of Management who specializes in mass customization. “The driving force will be consumers, who find out that this is cheap, flexible technology.”
The technology is not cheap, yet. Fu talks about a day when people will order clothes and shoes based on their own body scans, but even she, a designer of such software, won’t stake out a date. 3-D technology is taking its first steps in high-value, high-volume industries, primarily the aerospace and medical fields. If we want to see what the technology holds for the individual consumer, we can get a glimpse now through the medical industry.
In the mid 1990s, Emanuel Sachs, a mechanical engineer at MIT, developed the 3-D printer. It is a deceptively simple idea. It uses the same principles as an ink-jet printer, but instead of ink on paper, it sprays a soluble binder onto a sheet of ceramic powder. After 250 layers, the soluble portion is an inch high. Machines can now print objects nearly a foot high.
Unlike other additive processes, MIT’s printer allows for a great freedom in materials. Today’s commercial 3-D printers typically use ceramic to build marketing and machining prototypes, but can also print with metal powders, or be infiltrated with a fl exible or hard epoxy afterward. They make incredibly complex shapes, are porous and have a rough surface.
James Serdy, a researcher at MIT’s 3-D lab, thought these qualities would make them perfect for medical implants. Working with bioengineers, Serdy patented a process to print bone polymer scaffolds already being put inside people.
Instead of a ceramic powder, the machine lays down a powder of polycaprolactone, a biodegradable thermoplastic; tricalcium phosphate; and ground sugars. Instead of an epoxy, the printer sprays tiny droplets of water, electrostatically steered in fine streams down to 40 microns (a cell is one or two microns). Where the water strikes, the sugar particles melt and fuse together.
“It’s a pretty simple concept,” Serdy said, “just using water to cement these sugars together.”
The remaining powder is blown away and the water is leeched out. The crystallized sugar remains bound. The object is bathed in a chloroform vapor, which melts the PCL to create a plastic film over the shape. A water bath then dissolves the sugar. The result is a complex, porous polymer shape, whose outside and internal geometry can be designed on a computer alongside x-ray images.
Once inside the body, the scaffold is injected with the patient’s stem cells to stimulate new bone growth. In time, the scaffold dissolves. MIT originally convinced just one of its six 3-D printer licensees, Therics, to pursue medical applications, but has recently spurred Ex One and Z Corporation into the field.
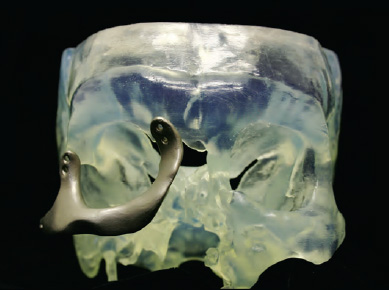
“I regret that the biological fi eld got so little attention until very late in the game because in many ways it is the natural use for this process,” Serdy said.
Therics concentrated on craniofacial applications, filling small, intricate voids, but its product wasn’t fully launched into the marketplace, and the struggling company was bought by Theken in 2005.
The opportunity for consumer-driven manufacturing is already clear. Sunil Saini, director of research and development at Therics, said a spine surgeon contacted the company last year seeking a half-cylinder cap that could protect his bone grafts from displacement by soft tissue.
Like two builders hunched over a bar napkin, the surgeon and the software technician sketched a design on paper. Therics translated it into a digital design and printed the surgeon a few dozen caps. A pediatric spine surgeon is now working with Therics on his own, small design for his own small patients.
“We’re scratching the surface of this now,” Saini said. “They’re not just relying on what the manufacturers give them. Even if it’s not an economic blockbuster, there are definitely more ideas out there that haven’t been developed.”
Andrew Christensen, president of Medical Modeling LLC, uses Mimic 3-D software from Materialize to design models of missing bone fragments from CT and MRI scans, allowing surgeons to sculpt a replacement before surgery. He recently invested $1 million in an electron beam melting machine, capable of building titanium and cobalt chrome, thus propelling him to build the actual implants.
Prosthetics and other large implants will remain in the realm of standard manufacturing for now, experts say. Not only are they cost effective, but additive manufacturing processes, such as the 3-D printer, have yet to conquer the materials problem. One of the next hurdles is to print scaffolding that can hold weight.
“Within 20 years, everyone will have a piece of equipment to print teeth,” said Thomas Cole, president and co-founder of Atlantis Components, which uses 3-D software to make low-cost abutments for dental implants.
If that’s not futuristic enough, consider another great 3-D materials challenge: to print organs.
Vladimir Mironov generates a media buzz with his obsession to raise money. The director of the Bioprinting Research Center at Medical University of South Carolina, Mironov says that with $1 billion and fi ve years he can complete the processes to print a kidney. And he is hardly alone. Mironov has convened three international symposiums on the topic. The Chinese have already found that 90 percent of cells can survive the printing process.
“You could have a patient in an operating room, opened up. You could put him through the MRI or CT scanner, get the data you need, then almost be printing that body part,” said Terry Wohlers, a leading consultant on rapid prototyping technology. “That’s the goal.”
It’s quite a few years away. But given such technology, who knows what the consumer of the future, the “active producer,” might design himself, or request?
Computer programmer John Braun has a 3-D printer in his kitchen. Although he has no architectural experience, he bought a Z Corp 410 for $75,000 and launched a successful business printing architectural models. He upgraded to an improved, color Z Corp Spectrum Z510 for $50,000. He can digitally design and print in two weeks what takes two to four months to build by hand.
He is fascinated by the technology. He attends conferences on the machinery, spoke at Euromold last year and likes to invite friends over to watch things print.
“I’ve got this vision of having this machine in your kitchen, where you would have an animal protein substance, a plant substance, and maybe five base flavor substances, kind of like RGB colors in your printer,” Braun said. “You could call up on your way home, say, ‘I would like fried chicken for dinner.’ When you drive up, the house smells like fried chicken and you pull it out of the machine.”
“I think that’s within the realm of possibility. You just have to convince the FDA.”