By Bridget Mintz Testa
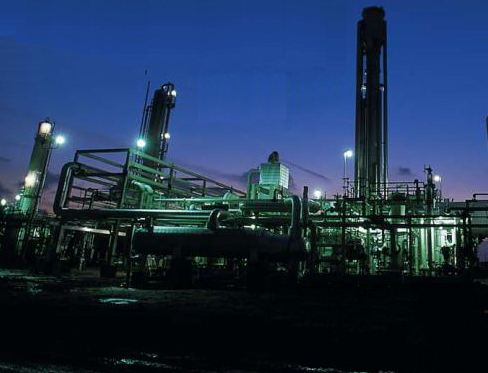
Until about three years ago, it was widely thought that most natural gas in North America was either gone or too expensive to drill. Today, new approaches to extracting this fuel have revealed drillable reserves sufficient to last another hundred years at current levels of consumption.“Unconventional” natural gas is the source of this new abundance. Conventional natural gas is typically found along with oil. Just as the easiest oil is gone, so is the associated natural gas. Shale gas is the main source of the enormous increase in reserves.
Shale gas lies in deep high-pressure and high-temperature formations 10,000 to 25,000 feet (or more) beneath the Earth’s surface. Shale is impermeable, and it must be fractured repeatedly to create pathways for the gas to flow back to a well hole. Without a wide variety of precision-machined products that follow the American Petroleum Institute’s specifications, like tubular steel, couplings, valves, wellheads, drilling bits, bridge plugs, perforating guns and packers, unconventional natural gas extraction and production would not be possible. Any good machine shop can make oil and gas products, but getting a foothold in the industry involves much more than cutting steel.
The Long Road To Exploiting Shale Gas
“The oil and gas industry has known for decades that shale is a source rock for hydrocarbons,” says Chip Minty, a spokesperson for Devon Energy, a major player in unconventional gas. “Shale has produced the reservoirs we’ve used for about 100 years.”
Over geological time periods, oil and gas from shale formations moved into permeable sandstone reservoirs. Those sandstone reservoirs were reached by drilling vertical wells through the shale.
Attempts were made to extract the hydrocarbons in shale, but they weren’t very successful. “The old literature said that the typical shale gas well would produce about 500,000 cubic feet per day in its first year and then drop off to a very low level (unprofitable) for the next 30 years,” says Rick Smear, a director of the natural gas practice at Navigant Consulting in Houston.
“In 1981, George Mitchell of Mitchell Energy directed his engineers to look into tapping the Barnett Shale north and west of Fort Worth,” Minty says. Mitchell had leased about a half million acres of land above the Barnett Shale, where he’d been producing oil and gas from conventional sandstone reservoirs associated with the formation. Mitchell knew, however, that the shale held far more hydrocarbons. He drilled more than 100 vertical wells into the Barnett Shale to learn how to get the gas so it could be produced, according to Steven Holditch, head of the petroleum engineering department at Texas A&M University in College Station.
“Mitchell’s people started experimenting with fracturing the shales,” Minty says. “They tried a number of methods and started seeing progress in the late 1990s. That was when they started honing in on hydraulic fracturing, which is injecting water under high pressures into the well. This created enormous pressure on the rock, which shattered the shale. That creates the porosity necessary for the gas to move to the well borehole.”
Only some 150,000 acres of the lease could be reached this way. In the other roughly 350,000 acres, the shale lay above the Ellenberger Aquifer. When hydraulic fractures penetrate through shale into water, the water seeps into the wells, which “kills” them. In the 150,000 acres Mitchell was drilling, tough layers of limestone encased the shale, both top and bottom. There was no possibility of seepage.
Devon Energy bought Mitchell Energy in 2002. The company wanted to exploit those other 350,000 acres of the Barnett Shale. It applied a familiar industry technology, horizontal drilling, to the Barnett Shale and also figured out how to use the shale itself as a barrier against the Ellenberger Aquifer.
“We drilled down into the Barnett, but took the well laterally through the top half of the shale, using the bottom half as the fracture barrier,” Minty says. “This let us get to the other 350,000 acres. We also discovered that by drilling horizontally, we could make the well even more productive than vertical wells because we were exposing the well to a much greater area of the shale.”
Since 1981, seven more major North American shale gas basins have been developed. “We produce 20 trillion cubic feet per year of natural gas in the United States and import three trillion cubic feet from Canada,” Smear says. Including all natural gas sources, “the total recoverable resource in 2008 was 2247 Tcf,” he says. “At 23 Tcf per year, that’s about a century of low-greenhouse-gas-emitting fuel for the United States.”
Can’t quite visualize those volumes? Try this. Lake Superior, the biggest of the Great Lakes, is 350 miles long, 160 miles wide and an average 483 feet deep. It contains 2900 cubic miles of water (more than all the other Great Lakes combined). The total volume of recoverable natural gas Smear cites, at 2247 Tcf, would fall about 5.26 Lake Superiors. The volume of natural gas the U.S. uses in one year, 23 Tcf, is about 5 percent of Lake Superior.
Hydraulic Fracturing
“To produce natural gas at commercial flow rates and recover enough volume to make a profit, the horizontal wellbore must be treated to create cracks or fractures in the shale,” says Holditch. This is done through a “fracture treatment,” which means applying high-pressure hydraulic fluid at specific locations along the wellbore. “The cracks provide the paths for the gas to flow to the wellbore,” he says.
Before hydraulic fracturing ever begins, a vertical well, or “hole”, as it’s called in the industry, is first drilled to assess the quality of the shale formation. If the quality is good, data about the formation from the original vertical hole is used to gradually turn the well horizontally. The point where the well becomes horizontal is its heel and the point furthest from the surface is called the toe.
A horizontal hole is typically 2000 to 6000 feet long and 8 to 12 inches in diameter, according to Holditch. Once this hole is drilled, the operator must decide whether to leave the hole open or cased and cemented. Most commonly, the second method is chosen: steel casing is run into the well and cement is pumped down and around the casing to anchor it in place.
To fracture shale in stages by the conventional method, sections of the horizontal hole are isolated with bridge plugs. These devices completely plug the hole from the casing to the cemented wall of the formation to isolate sections of the wellbore. Bridge plugs can be made of steel or steel alloys but are usually made of composites that can be drilled easily.
Once a section is isolated, the hydraulic treatment must be applied, and for this, the casing, cement and shale must be opened up in some way. Perforating guns, which are tools that contain shaped charges, create entry cracks in the shale. The perforating gun shoots high-pressure jets of gas and particles out in 360 degrees, all around the gun.
Next, “fracture fluid” is pumped at high pressure down the casing through the perforations in the formation. Mainly composed of water with small amounts of bactericide, a friction-reducing agent, and a polymer to increase viscosity, fracture fluid also contains large quantities of sand. When this high-pressure fluid is pumped in, the entry cracks expand and penetrate further into the shale. Pressure forces the sand into the fractures, where it remains, propping them open. The industry refers to the sand as a “proppant.”
Fracture treatments start at the toe of the well. Each stage requires setting bridge plugs and perforating. Subsequent stages are pumped by moving closer to the heel of the well, until the entire horizontal hole has been “stimulated” to allow the gas to flow.
“Each stage of the treatment can take a day or more to complete, although two stages can sometimes be pumped in a single day,” Holditch says. “If an operator pumps 10 or more fracture stages in a single well, it can take days to completely fracture-treat the shale formation along the entire length of the wellbore.”
Once all the treatments are complete, the shale is laced with fractures, most of which will be propped open with sand. In the first few days after fracturing are complete, fracture fluid flows back along with small amounts of gas. Before the gas can be produced in significant quantities, the bridge plugs must be removed by milling. All this debris must be cleaned out and removed with water or brine before real production can begin.
Machining for the Oil Bidness
If you’d like to make bridge plugs, perforating guns, packers, tubing or any other oil and gas products, the good news is that you don’t need any special or exotic machining skills. The bad news is that getting into the oil and gas “bidness” isn’t easy. And due to the boom-bust nature of the industry, a conservative business owner should think twice about relying solely on oil and gas for a living. Nevertheless, a good shop with the right attitude and capabilities can do it.
Mike Bowman, president and owner of Hunt and Hunt, a contract machine shop in Houston that specializes in perforating tools, identified a couple of barriers to entry. The industry is now “chasing low-cost overseas manufacturing,” Bowman says. He says these are “just low-quality, low-tolerance parts. High-quality, intricate parts are still made in the United States, but [the overseas manufacturing] makes it very difficult to compete as a domestic manufacturer.”
Another barrier is the face-to-face nature of the business. “The oil field likes you to come down and discuss a project, so being close to your customer is important,” Bowman says. “It’s all about in-person relationships.” The headquarters of the Big Four oil services companies— Baker Hughes, Halliburton, Schlumberger and Weatherford—are in Houston, which has more than 4,000 machine shops. If you’re not in or near Houston, Bowman believes your shop faces a disadvantage.
These barriers can be penetrated. If your shop is far from Houston, but has special capabilities, like the ability to work with exotic materials such as inconel or hastalloy or handle large-diameter tubular goods of 40 inches in diameter or more, that may trump the distance issue.
“Machine shops that want to get into oil and gas need to have capacity, good prices and quality,” says Mark Adamson, owner and founder of Tech-Seal International, a 40,000-square foot facility in Houston. Adamson makes flow-back equipment and a solar-powered pump for the oil fled. By capacity, he means knowing how to work with large tubular goods and how to provide fast product delivery. Because so many of the products in oil and gas are tubular, Adamson says that knowing how to work with those goods is very helpful.
He also stresses the value of certification by ISO or the American Petroleum Institute. “Certification by either of these shortens the time to become an approved vendor for the major oil and gas service companies,” he says. “They won’t even send out an audit team otherwise.”
Dan Themig, CEO and c0-founder of Packers Plus, a Canadian oil service company, advises machine shops to develop relationships with the large oil services companies. “That usually starts with small jobs,” he says. “Develop the expertise to machine oil-field products. Pick specific products. A starting point would be to meet with companies that purchase downhole tools, learn their requirements and then start developing the expertise to do that work. The larger service companies have the staff to set up inspection and quality standards. Then transition to some of the smaller services companies.”
Besides providing certification, The American Petroleum Institute is helpful in other ways. “The API publishes about 500 standards,” says Dave Miller, API’s standards director. “But if you winnow those down to the specs that facilitate discussion between buyers and sellers, it’s about 60 standards.”
API’s Web site, www.api.org, features a list of API-licensed manufacturers, along with the products they make categorized by standard. Machine shop owners and managers can study this list to identify products they’d like to make. “Then they can go to the publications part of the site and search for the specs they want,” Miller says.
API holds regular standards meetings around the country. “The meetings draw 300 to 500 people, including owner-operators, oil companies, oil services companies, manufacturers, consulting engineers and government representatives,” Miller says. It’s an opportunity to network face-to-face with people in the industry, discover their needs and where you and your shop might fit in. Registration fees are $400 to $500 for the week-long meetings. “Look at the site and the composite list,” Miller says. “Zero in on a particular area and maybe buy one or two of the standards. Then maybe go to a meeting to find out about the needs in the industry or if a standard is going to change.” (To go directly to the list, go to www.API.org, click on “certification program,” then “monogram program,” then “composite list.”).
Taking this advice can help a machine shop overcome distance from Houston and build its own network of oil and gas customers. Packers Plus started out in Canada and didn’t start working with the oil and gas industry in Houston until several years after its founding. Despite its small size of 300-400 people, it’s now a major player in the industry, and its technology is so highly sought-after that in 2005, Schlumberger bought an undisclosed minority share of the company. It also entered into a partnership where Schlumberger would internationally promote several Packers Plus technologies. Themig won’t cede any more control, however. He wants to keep the company closely-held and focused on being world-class. It took Packers Plus a few years to find its niche, as it did for Bowman and Adamson. The two Houstonians each did job-shop work initially, but then they found specialties that set them apart. That’s the path to success for machine shops in oil and gas.