Today’s Machining World Archive: September 2007, Vol. 3, Issue 09
Bar stock in one side, completed parts out the other.
They’re called turning-milling, multi-tasking, multi-function, or mill-turn machines. They turn and they mill, in the same machine, in the same setup, maybe even at the same time. They come with a lathe spindle, or more likely two, and some means of milling – turrets or a milling head or sometimes both, all with enough power to do real metal cutting.
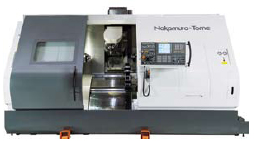
Lathes with live tooling have been around for a long time, and, of course, screw machines have been turning and milling parts too.
But recent generations of turn-mill machines have the speed, power and flexibility to make parts faster, with higher accuracy and less setup time. They can machine from bar stock to finished parts, top and bottom, front and back, inside and out, all in the same machine,
Of course, these turn-mill centers are not cheap. A smaller, unit with, say, a 6-inch chuck, dual spindles, and two turrets, might run you $200,000. A full-blown 9-axis tilting head machine with a 12-inch chuck could cost in the range of half a million dollars.
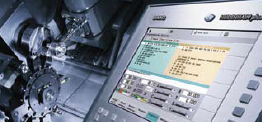
Can these machines really be worth it? A lot of people think so, and more and more shops are willing to pay. Manufacturers of the turn-mill machines find customers need the machines’ capabilities in order to stay competitive.
“We can go to a customer and say, ‘We can improve your overall process time by at least 15 percent,’” said Steve Wilkins, general manager, northeast region for Mazak Corporation, Windsor Locks, Conn. And that’s a minimum, he said. Thirty percent is common, and one customer has experienced 78 percent process time improvement, he said. “They shut down the [turn-mill] machine three days a month to let the rest of the shop catch up.”
Job shops are early adopters
Job shops with 25 employees or more seem to be the most likely to buy a turn-mill machine, Wilkins said. Smaller shops might hesitate at the cost and seek less expensive turning centers or lathes with some milling and drilling capability, and many large companies seem to be slow to adopt the new technology. This is actually good for the job shops that have turn-mill machines, as they can make parts more economically.
Shops need to have their turn-mill equipment in house and running, Wilkins said. “You can’t get the contract and then order the equipment.” He said he sometimes receives calls from customers looking for shops that have particular types of machine, and those shops receive orders.
One turn-mill machine can complete the processes that used to be done on three or four or five machines – lathes, milling machines, machining centers, pointed out Scott McIver, chairman, Methods Machine Tools, Inc., Sudbury, Mass., importer and distributor of Nakamura equipment. “Most of our customers buy this type of machine in situations where they need to be more profitable. [They’re] getting rid of redundancy, can get rid of multiple operators and stations, and get a more accurate part.” Turn-mill machines account for a significant portion of his company’s sales, McIver said.
Sometimes a shop owner will come in and say, “I’ve got a part I want to quote,” but he can’t machine it on his current equipment, McIver said.
Once they start down the road to turn-mill, shops can use the machine to grow their business, McIver said. They can go out and find work, parts that need lots of milling, or secondary operations.
Also, when longtime customers say, “I need a discount,” and the shop owner may think, “I can’t make this part profitably,” a multi-function machine can do just that, McIver said.
“By its nature it’s automated,” said Dion Coleman, application engineer at DOOSAN Infracore America Corp., West Caldwell, NJ. “Bar stock in one side, parts out the other.”
“This is not the way to make every part. The key is the right quantity and the right complexity of parts,” said Coleman. But the correct combination of quantity and complexity is different for every part. For example, for your just-in-time customers, you will want to make short runs. Your turn-mill machine can take care of that. Once you have the part program in the control and the tools in the magazine, you can start running that part quickly, maybe even in a matter of minutes, by just changing the material and work holding.

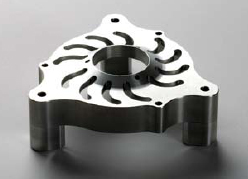
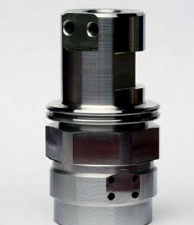

Quality, Accuracy, Scheduling
If you have a multi-tasking machine, once you get it set up you can start producing parts immediately, said Coleman. Even better, you can do a first piece inspection and find out if there’s a problem right away, rather than after running an entire batch of parts through several machines.
And, because you aren’t moving the part from one machine to the next, it won’t suffer from the accumulated loss of accuracy that comes from placing a part in one fixture after another, Coleman said.
Scheduling becomes a non-issue when one machine does the process, start to finish. And work-in-process inventory goes way down. A turn-mill center can even save floor space, as you don’t have carts and tables of parts waiting for their next machine.
Of course, there is more to getting up and running than just buying the machine. Application engineers at the manufacturer will help you get started. You’ll probably need to get up to date on the latest CAM software for programming your machine. This may be an easy step if you’ve been programming machining centers, but if you’re stepping up from simpler machines or have been programming manually, it’s going to take a while to learn and get comfortable with the software and operation of the machine.
Programming
A turn mill is really a lathe with up to eight different kinds of milling going on as well, said Hanan Fishman, president of Partmaker, Inc., Fort Washington Pa. There is a lot happening inside the machine, but the individual motions aren’t that complex if you break them down into their individual steps.
Besides controlling the cutting, you’ll want to synchronize operations, move the part from the left spindle to the right, perform cutoff, etc. You will also want to balance the operations on the left and right spindle, so they take approximately the same amount of time. Much of the time-saving potential of a turn-mill machine is that cutting can happen at both spindles at the same time.
To maximize the uptime for your new turn-mill machine, you’ll want to create the program for each part offline, with a CAM (computer-aided manufacturing) software package.
What you really need your software to do for you is produce code that works on your machine. The offline programming process actually consists of two aspects. One is creating a program to guide the actions of the machine. The second is transforming that program into code that will work on your model of machine. This is called post-processing, and is very important. If the post-processor for your machine doesn’t work right, you will have to tweak and edit the code on the machine.
You will also want to check out the program before running it on the machine. Software packages often include simulation features so you can see what happens, step by step, and watch out for any problems.
In selecting software, your primary question should always be, “Can this software generate good code for my machine?” Fishman said.
When evaluating which software to buy, you should keep in mind the following:
• One size does not fit all
• Different shops approach programming differently, and start out with different part documentation, whether drawings, or electronic files.
• Do not take the vendor’s word for anything. Check it out yourself.
• Make sure the vendor demonstrates the software in a way and at a pace that is comfortable for you.
• Be sure to get independent references. You want to talk to people who are using the software and have the same machine you do.
• The manufacturer of the turn-mill machine may have a recommendation. Listen, but check out the software yourself.
You may want to take the “try before you buy” approach, in which your staff receives some training and then has a free trial of the software for a month. Or you may prefer a web-based demonstration, or a demonstration in person at your shop.
Tooling
On mill-turn systems that have a milling spindle, the spindle will sometimes be milling and sometimes be holding a static tool for turning. This function can place a burden on the tool holding hardware.
One thing to be aware of when ordering a machine, Coleman said, is that manufacturers offer milling spindles with different types of tool connection systems. Turn-mill machines place more demands on the tool connection than either turning or milling. “You’re using that spindle to hold both static and rotating [tools],” he said. “The indexing is critical.” Many tooling companies have application engineers who specialize in tooling for multi-function machining and can advise you. Some offer tools and accessories specifically designed for multi-function machines.
The Coromant Capto connection system was developed for multi-function machines, but can be used elsewhere, as well. It is designed to provide repeatable installation within 80 millionths of an inch, said Jim Grimes, a product specialist at Sandvik, Inc., Fair Lawn, N.J.
Grimes said Sandvik has also developed a line of tooling for multitask machines. Multiple cutters can perform different types of cuts, which saves time on tool changes and saves space in the machine’s tool-changer magazine.
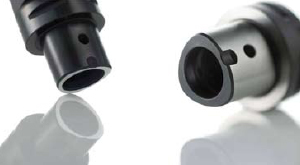
Getting the most from your turn/mill machine
Today’s turn-mill machines will give you higher milling speeds than you may have been accustomed to on your older machines. Take advantage of their ability to take light, fast cuts. For best results, consult your tool vendor for the appropriate cutting tools.
And then there is the number of tools. Though the option for a larger capacity tool changer may seem like an unnecessary expense up front, consider how you will be using the machine in the future. If you keep all the tools for all the parts in the tool magazine, you will consistently minimize changeover time.
To help minimize the number of tools, look for places where you can use a single size of a cutter instead of multiples. For example, you may be accustomed to cutting part A with a half-inch end mill, and part B with a three-quarter-inch end mill. You can revise part B’s program to use the half-inch mill, thus saving one tool.
These turn-mill machines may sound too good to be true, but users are finding they can cut process time, not to mention setup time and work-in-process inventory. The wave of the future? These multi-tasking machines may be a key to success.