Today’s Machining World Archive: July/August 2009, Vol. 5, Issue 06
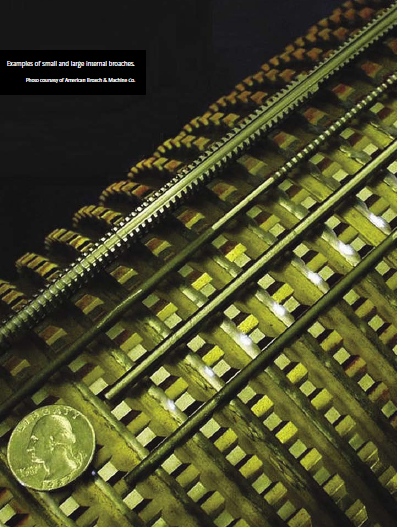
Making accurate and complex cuts easy and economical for high-volume parts
A broach is a cutting tool with many rows of teeth, each slightly larger than its predecessor. They are designed to produce simple or complex forms quickly, usually in one pass, with repeatable and reliable accuracy. As the broach moves past the workpiece (or the workpiece past the broach), each tooth takes a shallow cut along the whole length of the part, carrying the chip to the end of the part, said Dave West, general manager at V-W Broaching Service, Inc., Chicago, Ill., which provides broaching and broach sharpening services and manufactures broaching tools. In many cases, a single pass of the broach completes the machining of the surface. For some workpieces, multiple passes with multiple broaches may be required, depending on the geometry of the part and the amount of stock to be removed.
A typical broach consists of many rows of teeth that do roughing, then a few rows of teeth for semi-finishing and another few rows that finish-machine the surface. The tool design is based on the shape being cut, the properties of the workpiece material and related factors. You can broach internal or external surfaces to almost any shape imaginable, from simple flats and slots to gears to turbine blade hubs for aircraft engines.
Broaching can be quite simple in geometry—cutting a keyway in a gear or other component, for example—or quite complex. Broaching is often used to cut precise diameters or to produce non-round holes in shapes such as a hex, square, or “double D.” You can also use broaching to cut splines, gear teeth and other shapes. West spoke about a surface-broaching job at V-W Broaching that cut 50-plus different dimensions in one pass. “All the dimensions are built into the tool,” he said
A very simple manual broaching job, such as cutting a keyway in a single part, requires only a broach, an arbor press and the appropriate fixturing. Production broaching requires specialized machines and is best for a very large number of parts.
Broaching can reduce the cost of machining certain features to pennies per part. In addition, broaching can sometimes perform cuts that would be impossible to make any other way. In use for more than 100 years, broaching is still widely recognized as the best process for many applications.
Broaching machines come in different configurations; horizontal or vertical, and are designed for internal, external, spiral or surface broaching. In a typical internal broaching machine the part is fixtured and the broach is pulled through it. For broaching outside diameters, typically the broaches are fixtured in the machine and the part is pushed past them. Spiral broaching is often done on a horizontal machine that drives the broach to spiral through an inside diameter and create helical grooves, such as those in a rifle barrel.
Applications
Many materials can be broached. “Almost anything you can cut by machining,”said West, including ferrous and nonferrous metals and even some plastics. V-W Broaching runs dozens of broaching machines, producing parts large and small, for just about any use or industry you can think of—hand tools, appliances, automotive, farm implements, turbines, plumbing, military and many others.
Broaching works best in materials with hardness in the range of 26 to 28 Rockwell C, said Ken Nemec, president of American Broach & Machine Co., Ypsilanti, Mich., manufacturer of broaching machines, broaches and CNC sharpening machines. It is commonly done in the range of 10 to 32 Rockwell C. Chip formation is critical in making good broaching cuts, however, and soft materials
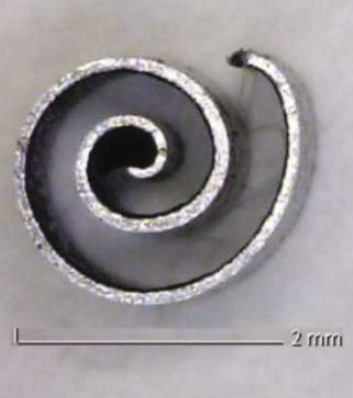
“are like bubblegum,” Nemec said, but in the ideal range of 26 to 28 Rockwell C, you get clean chips and good tool life. The tool designer needs to take the workpiece material properties into account and needs to run the tool at the appropriate cutting speed to achieve the best results for a given part.
For precision parts that need to be heat treated, such as gears, a part can be broached to near net shape before heat treating. Then a finish broaching operation is performed, removing just a small amount of the hardened material, Nemec said. In this case, the very expensive, specialized machines can cut material as hard as 58 to 60 Rockwell C.
Broach it yourself
The machines and the broaches tend to be quite expensive, but if quantities justify the investment you could bring this capability into your shop. “Most people have sticker shock when they get into broaching,” said Nemec. “It is pretty expensive, especially if you want to get into high production.” You may have a high-volume part on which it costs 20 cents to machine a particular surface that is suitable for broaching. “We can show you how to do it in a lot less time, but you have to invest in capital equipment,” he said. In addition to high-volume machines, American Broach & Machine also offers lower cost broaching machines suitable for shops that want to broach smaller quantities of parts.
If you have a high-volume part or family of parts that look as if they may lend themselves to broaching, the machine manufacturer would start from the print. “First we design a broach for you, then design a machine for the broach,” said Nemec. “We have about 10 different types of broaching machines. We stretch them bigger, and use more or less pressure,” depending on the specific application. Since each machine is different, it is designed and built to order. Delivery can be 26 weeks or longer, he said. Options such as automated parts handling or pressure- monitoring can add capability. “Buying a broaching machine is like buying a car,” Nemec said. There’s a base price and then you add on the options. In his experience, some customers want relatively bare-bones machines. But adding options can save money in the long run—and sometimes, in the not-so-long run.
TLC for tools
An increase in force during a cut indicates that the broach needs sharpening. American Broach & Machine offers a pressure monitoring option that allows you to track the condition of the broach. This capability will add about $16,000 or $17,000 to the cost of the machine, Nemec said, but it can quickly pay for itself. Considering that a broaching tool may cost $2,000, you can easily scrap enough tools in one year to pay for the monitor, he said.
To make good use of the machines you’ll need to understand a few basics of broaching and how to keep your process in order. The machine manufacturer should provide training—just two or three hours with your staff “can save a lot of time, trouble and money,” said Nemec.
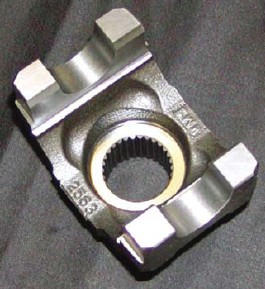
Care of broaches, both on and off the machine, is critical to keeping a broaching process profi table. You can run a new $2,000 broach until it fails, get maybe 8,000 parts and then throw it away. Or, you could run 3,000 parts and then sharpen the tool, as many as 20 times, said Nemec. This makes your cost come way down—8,000 parts versus 60,000 parts with the same tool. If sharpening costs $80, this works out to a tooling cost of 25 cents per part versus 6 cents per part.
Off the machine a user must take pains not to damage the cutting edges. Don’t leave broaches lying around on the bench, Nemec said. Store them in wood, plastic or cardboard containers or sleeves, which allow the teeth to dig in but won’t damage them.
Timely and correct sharpening extends tool life and helps keep tooling costs down. You can send tools out to a shop that specializes in sharpening broaches. However, by the time you have three or four broaching machines, you would save a lot of money by sharpening them yourself on a CNC sharpening machine instead, said Nemec. “The guy who is putting that broach in a box could sharpen it.”
Rotary broaching
Rotary broaching is a completely different process. It can cut the same forms as conventional broaching, but you can use it on your screw machine or lathe. A special rotary broaching tool holder mounts on the machine turret, and rotary broaching becomes just another step in your process. This eliminates the need
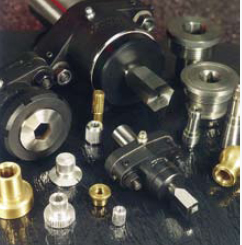
for secondary operations to form square holes, hex holes, splines or gear teeth, or almost any other internal or external shape you want. Rotary broaching easily works in blind holes, which is not possible with conventional broaching.
A rotary broaching tool has cutting edges the shape of the hole or form you want. It mounts in a toolholder that holds the tool at a 1-degree axial tilt in relation to the center line of the workpiece. Bearings in the toolholder allow the tool to rotate freely. The workpiece is turning, and when the tool comes in contact, it rotates right along with the workpiece. Because of the 1-degree axial tilt, the tool appears to wobble as it rotates. Because of this, rotary broaching is sometimes called “wobble broaching.” It is also known as “Swiss broaching.”
Rotary broaching in action
Before the rotary broaching operation, the workpiece needs to be drilled or turned to the correct diameter for use with the rotary broaching tool. This minimizes the amount of material that the tool will cut. Then, the area where the tool will contact the workpiece is countersunk or chamfered, to allow smooth engagement of the tool. If the chamfer or countersink is not acceptable in the final part, you can design your process to remove it afterward. Then the part is ready for broaching. The following describes internal rotary broaching; external is similar.
As the prepared workpiece is turning, the rotary broaching tool/toolholder advances toward it. Because of the 1-degree axial tilt, only one corner of the tool engages the workpiece at first. When the tool makes contact, the workpiece drives the tool to rotate in unison with it. During rotation, first one corner of the tool contacts the workpiece, then the next, and so on, around and around.
As the tool advances into the workpiece, each corner, in turn, cuts into the metal. This way, bit by bit, the tool cuts a shape that matches the shape of the tool.
How large a form you can rotary broach depends on the material. In aluminum, you can usually rotary broach up to 2”, in steel to 1″. You can rotary broach harder materials, but in smaller sizes. For example, you could broach a quarter-inch hole in Inconel, said Peter Bagwell, engineer at Slater Tools Inc., Clinton Township, Mich.
Toolholders and setup
The technology was developed decades ago, but rotary broaching companies continue to improve tool holders and tools to increase tool life and make the technique easier to use. Because of the precision alignment and offset required, rotary broaching tool holders traditionally required many adjustments and painstaking setup, which could take considerable time, depending on the employee’s experience. A standard rotary broach setup might include six set screws, two bolts with nuts and a sliding plane between the toolholder body and the machine adapter.
Rotary broaching engineers have developed innovations to streamline setup procedures. A specially designed tapered-centering-pin gage can allow you to set
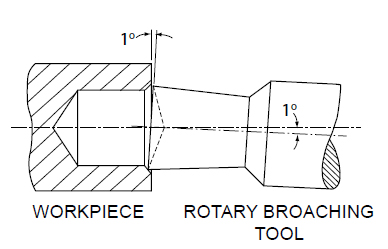
up a fully adjustable tool holder in a minimum of time, said Dick Noti, sales engineer at Somma Tool Company, Inc., Waterbury, Conn. Some toolholders require only an X-axis adjustment, and, in recent years, no-adjustment rotary broaching toolholders for Swiss-type machines have become available.
If you are sending out parts for broaching, or have a job that might take advantage of rotary broaching, contact a rotary broaching tool manufacturer. An application engineer can look at the part and advise you. If you’re not sure you want to make the investment, many suppliers will let you try out a toolholder and broaches on your own machine, without obligation.
Cutting fluids also influence the tool life and part finish, of course. Generally, you should use a good water-soluble oil, Nemec said. In more challenging applications a heavy cutting oil may be needed. Many cutting fluid suppliers offer specially formulated coolants for broaching applications. Your machine manufacturer and tool supplier can recommend appropriate coolants.
With brass parts you’ll want to use a water-soluble oil that won’t discolor the material. You’ll also need a watersoluble fluid with certain thin-walled parts. “Especially for internal [broaching] with thin wall sections, sometimes coolant can make a difference in what your final tolerance is,” said West. “If you broach a round hole [with] a thin wall, it gets hotter than blazes and expands.” In this case, a water-soluble oil will help dissipate the heat.
Whether you broach high-volume parts yourself or send them out for broaching, you can take advantage of the capabilities of this time-honored process: precision, low per-part cost and the ability to cut complex forms with accuracy and repeatability not found with many machining processes.
2 Comments
Rotary Broaching also works on mills and VMCs. At least one half of the set-up needs to be turning, either the tool, or the broach. Broaching tools used in mills can also be fixtured with Broaching Orientation Dogs to align the holes to part features.
The real key to determining if the form can be broached has more to do with material removal per side than overall diameter. For example, a .75″ diameter spline with 1/8″ material removal per side will be much more difficult than a 1″ diameter form with .025″ material removal per side. Polygon Solutions has tooling to help some customers broach larger forms if needed.