Today’s Machining World Archives June 2011 Volume 07 Issue 05
By Barbara Donohue
Keeping bad, worn or obsolete parts out of the supply chain.
Out-of-spec or obsolete parts may look just like their current and in-spec brethren. In many applications, using nonconforming parts wouldn’t really be a problem. However, in other applications—aircraft, automobiles, medical devices, for example—installing a bad part could create a safety hazard, potentially causing injury or even death.
Where life and limb are at stake, regulators and manufacturers require any such parts to be rendered unusable. Otherwise, those parts could find their way into the supply chain and end up harming someone.
In other cases, perfectly good items may need to be made unusable, such as military equipment or a company’s excess inventory.
Destruction by design
Some recycling companies, such as SOS Metals, Inc., headquartered in Gardena, Cal., offer formal procedures for making parts, assemblies, and equipment permanently unusable. Termed in the industry as certified destruction, this process takes care of the scrap, obsolete parts, etc. that need to be kept out of the supply chain. A similar process handles military equipment that needs to be made unusable. SOS Metals has contracts with many airlines and aircraft original equipment manufacturers (OEMs) to perform the certified destruction of parts and assemblies, as well as the necessary approvals for handling destruction of military items, said Andrew Ballow, the company’s vice president of business development.
Because a certified destruction company has been qualified by its customers (airlines and OEM manufacturers, for example), procedures are in place to make parts traceable and, Ballow said, “if anything should happen, the liability would be on us.”
Demilitarization
Items relating to national defense must be prevented from being useful in the wrong hands. “Accountability and control of significant military equipment (SME) is essential to maintaining the United States military’s superiority,” said Lt. Col. Melinda F. Morgan, spokesperson for the Office of the Secretary of Defense, Washington, D.C., in an email interview. These are national security resources and the process for processing and disposal of SME is vital to the U.S. military.

“Most items in the Department of Defense supply system are assigned a demilitarization (Demil) code, A through Q. In many situations, items with a Demil code other than A will require some type of destruction action, usually through mutilation or demilitarization. “Demilitarization can best be described as the act of destroying the military offensive or defensive advantages inherent in certain types of equipment or material,” Morgan said. The purpose is to prevent the future use of the equipment, material and components for their original intended military purpose.
Items such as battle-loss armored vehicles, tank tracks, crashed aircraft, communication equipment, and weapon system components may require demilitarization in the field.
Aviation safety
“Certified destruction is not a term the FAA (Federal Aviation Administration) uses,” said Les Dorr, spokesperson for the FAA, Washington, D.C., in an email interview. “Instead, we use scrap and salvageable, as they apply to non-conforming aircraft products and articles produced by manufacturers under their approved quality systems.” These parts approval holders must have procedures to provide for identification, documentation, evaluation, segregation and disposition of any nonconforming products they manufacture.
Further, they must have procedures in place to ensure scrap items are rendered unusable.
In general, specific methods of making scrap unusable are not specified in regulations, but contracts require manufacturers to have procedures in place for carrying out the necessary handling and processing of scrap. Documents do offer guidance in identifying, segregating and controlling rejected products and articles to preclude their use in a finished product.
Also, a manufacturer must have procedures for identifying, storing, protecting, retrieving and retaining quality records, Dorr said, and must retain these records for at least five years for products and articles manufactured under their approval, and at least 10 years for critical components.
Chain of Custody
The process of certified destruction requires secure handling of the material to be processed. “A customer has the material—parts and assemblies—stored in a secure area at their facility, usually under lock and key in a caged area marked ‘Scrap material do not enter,’” Ballow said. “Only a few people have access.”
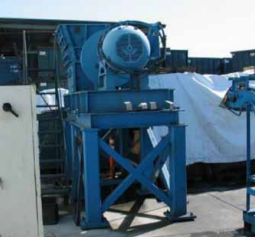
Sometimes there can be a lot of stored material—companies, like people, tend to hold on to things. When they can’t use it, they store it. After two airlines merged some years ago, SOS Metals’ Ballow said, a whole warehouse full of obsolete parts was discovered. “We took out nine truckloads from there,” he said.
Documentation all along the way is part of the secure handling process. “When we back a truck in—our truck or a common carrier—we’ll load the material into the truck and get a manifest—12 pallets, or 15 boxes, or whatever it might be. The truck will be locked and sealed with a truck seal. The truck seal number will be written on the paperwork that goes back to our customer.
“There’s a possibility along the way that the highway patrol or a weigh station wants to see [the contents of the truck]. They’re obligated to write something that says they opened it. Crossing a border, customs may open it, but they’ll reseal with a customs seal, so you know it wasn’t opened by any-one else.
“When the truck arrives at one of our facilities, when it backs in, we take a picture of the truck, the license plate and the intact truck seal, to show it arrives intact.
“We take the material immediately to a locked, caged area—triple security because we have fencing around the whole facility, then the building and the locked cage. It’s monitored 24/7 by cameras and motion detectors. “When we’re ready to process the material, we bring it out and sort it before destruction.”
Means of destruction
“Our processes depend on the parts,” Ballow said. “We would use a plasma cutter on some of the bigger parts. We’d use a chop saw—it’s kind of like a radial arm saw, you just pull it down and chop the part in half. We also use alligator shears—shears that have a mouth like an alligator. Instead of teeth, it’s got blades. You put a part on there, you press the switch with your foot and cut the part in half.”
“For smaller parts—if someone ships us a bunch of aircraft hardware, or we dismantle an engine—we have nuts, bolts, screws, rivets that have to be destroyed,” Ballow said. “If you did it piece by piece, it would take forever, so we have something called a hammer mill.
“A hammer mill has a conveyor that picks up the material and drops it into the top of the mill. Inside there is grinding media, like steel teeth, that does damage to anything you put in there. It will crack it or mutilate it. It will crack the head off a bolt. A thread? You can’t use that thread anymore.
“We dump [the parts] into the hammer mill. It grinds, and chunks, and bends, and breaks, and destroys the threads and heads, so the parts cannot be used or sold as new.”

For all items, when SOS Metals cuts, breaks, or otherwise damages them, “that’s the primary destruction,” Ballow said. “But the ultimate destruction is that we sell only to people who melt metal. So, after we have it all chopped up, sorted, cleaned, packaged and ready to go, we sell it to a melting house that melts it into a new ingot. The secondary destruction is actually melting the metal.”
Viewing the process
Customers have the option of coming to the facility and watching the destruction, Ballow said, but very few do. SOS Metals takes pictures or video during the process. Also, a customer can watch real-time video of the process over the Internet. “We say, OK, we’ll be doing your parts at 10:00 on Friday. Here’s the Web site. Simply go to your computer and bring it up. We have two or three cameras, and we can hold up a sign to show the customer name and lot number. They can record it if they want.”
Documenting the destruction is an important part of the process of destroying bad, worn or obsolete parts, Ballow said, “because of the importance of making sure that they never get back into the supply chain.”
In the shop
Most of the material SOS Metals handles from machine shops is made up of turnings and chips that come out of the machines, Ballow said. “But sometimes maybe 10 percent of what we pick up would be parts that have been rejected or superseded, obsolete inventory, excess inventory, bad machining, bad heat treat—there are a million reasons” for those parts to be recycled.
Shops generally put these scrap parts in a separate box. Safety- or defense-related parts, such as aircraft components, are not only separated, but also stored securely.
In your shop, you’re accustomed to making parts, bringing them to life. But there’s an end to their story, and for critical safety or defense components, they must finish their useful lives by being made unusable.