By Barbara Donohue
Today’s Machining World Archives April 2011 Volume 07 Issue 03
The thinnest of thin layers can make a big difference in tool life and performance.
In the early days of tungsten carbide tools, before coatings, tool manufacturers realized the tools would last longer and resist cratering if they put a little bit of titanium carbide (TiC) in the mix when making the tool. This had the desired effect, but the more TiC that was added, the weaker and more brittle the tool became. Then someone hit on the idea of applying a thin layer of TiC to the surface of the tool. It worked. This was in about 1970, said Don Graham, manager, turning products and education services, Seco Tools,Inc., Troy, Mich.
A year or so later, tooling companies started using a titanium nitride (TiN) coating, and in 1973, aluminum oxide began to be used.
Graham described the properties of these three coatings:
- TiC gives abrasion resistance and prevents the chip from dissolving the tool material, leaving craters.
- TiN prevents a built-up edge, where the workpiece material sticks to the cutting edge. This spoils the surface finish and also, when the buildup is dislodged, it pulls away part of the coating and maybe the cutting edge. This coating is the familiar gold-colored one.
- Aluminum oxide provides resistance to heat in two ways. First, it is an outstanding thermal insulator; second, and more important, it is stable to very high temperatures.
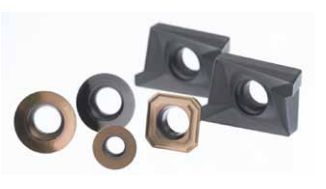
These coatings are applied by a chemical vapor deposition (CVD) process, Graham said. The tools are placed in a chamber. At 950 – 1100 degrees C, gases are pumped into the chamber, where they react and deposit a thin layer of material on each tool.
The other widely used coating technology is physical vapor deposition (PVD), “a newer and more sophisticated process,” Graham said, “where you’re building up the coating by shooting ions into the surface.”
For the PVD process, the tools or inserts are placed in holders or on rods, which are mounted on a sort of carousel that goes into the coating chamber. The carousel rotates and so do the rods and holders. Meanwhile, a strong negative electric charge is applied to the tools. In the chamber a “hockey puck” of titanium or titanium-aluminum is vaporized with an electron beam. The titanium and aluminum ions have a strong positive charge, so they are drawn to the negatively charged tools, colliding with the surface. Then nitrogen gas is introduced, and “if you do it right, [the process] will form a nitride [TiN or titanium aluminum nitride] on the surface of the insert,” Graham said.
With both CVD and PVD many kinds of coatings can be applied.
These days, a CVD coating typically has multiple layers, said Bill Tisdall, development and turning manager of tooling manufacturer, Sandvik Coromant US, Fair Lawn, N.J. Starting from the surface of the carbide tool it might have the following:
- TiCN (titanium carbonitride) provides flank wear resistance and provides adhesion between the carbide and the next layer.
- Aluminum oxide provides heat and crater wear resistance.
- Some grades might have a flash of TiN. The aluminum oxide is black, so this gives the operator the ability to see the condition of the cutting edge.
Of the two types, the CVD coatings are usually appreciably thicker than the PVD coatings.
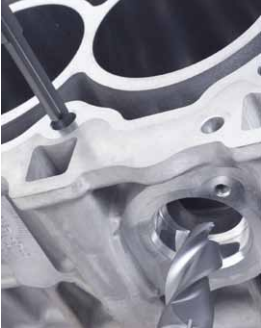
Thick coatings work very well in alloy steel and cast iron, Tisdall said. Thin coatings are best with materials that tend to be a little sticky, such as low carbon or stainless steels. If you cut a sticky material with a thick-coated tool, the material will tend to adhere to the tool. When the adhered material gets knocked off, it may take some of the coating with it.
The difference between a CVD tool and a PVD tool is more than just the type of coating. PVD tools have that thinner coating, but they also are designed with a finer structure in the tool material, a micrograin structure with carbide particles smaller than one micron. CVD tools have that thicker coating, but they also are designed with a medium-sized grain structure. This difference can help select the right tool for a particular application.
“If you are doing an interrupted cut with a CVD grade tool and get chipping along the cutting edge,” Tisdall said, “using a PVD grade might solve that,” because of the Evacuated tool’s fine grain structure.
If a PVD grade insert is breaking, he said, try a CVD grade—it has that larger grain structure and resists shock. The tool and the coating are designed to work together.
You can tell what is going on with the tool by the way it is wearing. Each wear pattern will tell you something: cut off the coolant, try a harder or softer grade tool, look at PVD vs. CVD grades. “There are probably nine different wear patterns we see in the industry,” Tisdall said. “They can give you a much better understanding what’s going on in the cut” and help improve your process. (See “For more information.”)
Evolution and revolution
Recently most of the changes in coatings have been more evolutionary, Graham said. Changes to improve performance included using different thicknesses and polishing the layers.
Some new, different coatings have become available, however. Gary Lake, president, CemeCon Inc., Horseheads, N.Y., a manufacturer of PVD coating equipment and provider of coating services, talked about titanium diboride, a unique coating that resists material transfer from copper or aluminum. It was used by the casting industry to prevent aluminum from sticking to molds, he said, and now it has been adapted for use as a tool coating.
Diamond Coating
Diamond Tool Coating LLC, North Tonawanda, N.Y., coats tools with polycrystalline diamond applied with a CVD process. The company works with tool manufacturers to develop the right combination of tool and coating to match such challenging applications as machining composites or graphite. The diamond coating can withstand the abrasiveness of these materials.
Not just any tool can be diamond coated, said the company’s general manager, Doug Mueller. “What tool material we can apply the coating to is limited. The best substrate is 6 percent cobalt, fine-grained carbide,” he said. “That will produce the best adhesion, which is the key to the success of diamond coating.”
You may be familiar with conventional polycrystalline diamond (PCD) tools, where a slice of diamond is bonded to the tool to provide a diamond cutting edge. That approach limits the available geometries, Mueller pointed out, while the CVD-applied diamond coating can coat complex shapes, such as helical geometries and chip breakers.
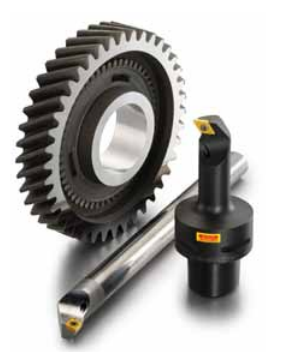
A CVD diamond coating works well for cutting anything abrasive, said Cyle Anthony, product manager at Niagara Cutter LLC, Amherst, N.Y. “We started with it about seven to 10 years ago for machining graphite for electrodes and things like that.” The coating has since been used on tools for cutting metal matrix materials, green ceramic, and a lot of different composites: carbon fiber reinforced polymer, fiberglass, Kevlar-reinforced materials. Composites are used in applications for such industries as aerospace, wind power, military, medical and automotive.
Not just a tool, not just a coating
How is the coating matched to the application? At CemeCon Inc., which specializes in PVD coatings, Lake said, “we use an empirical process. A customer brings an application, such as milling stainless steel. We have probably eight different coating chemistries commonly used now. We will provide three samples, each a little bit different from the others, for a cutting test to see if there is a difference. It’s an iterative process.”
“As we have gone through the evolution of the coating process, we have learned to adapt the coating to the substrate and cutting parameters,” he said. “We’ve learned how to do edge preparation. A little bit of a break on the edge gives some support to the coating.”
“We don’t look at it as just the tool anymore, we look at it as a cutting system,” Lake said. “It’s a question of knowing what is happening at the cutting edge.”
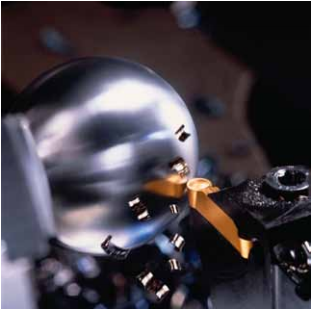
New on the horizon
New, challenging materials may be showing up on your customers’ prints, Graham said. You may have already encountered composites as used on the Boeing 787, others are out there, such as compacted graphite iron for diesel engine blocks, and zirconium oxide ceramic for knee and hip replacement joints.
Graham recommended that shops stay abreast of new developments in tools and coatings. “They should make judicious selections of emerging technology. Sometimes a product comes to market that will be the best for them. The faster they jump on it, the better they’ll compete.”
Generally a shop can rely on tool suppliers to help match tools with tasks, but you should be sure to ask a lot of questions about a new or updated tool or coating. Why is it good for my application? What kind of improvement can I expect? Any downside? Then you must be willing to give it a try.
2 Comments
I enjoyed reading this primer on tool coating, but overall the comments from various manufacturers are certainly over simplified as far as the wear types observed on cutting tools. The most glaring omission though is the truth behind the CVD or PVD question.
With the exception of easier to machine Cast Irons, PVD is the correct choice for coated tools. It not unlike the choice between using a carburetor or fuel injection on a gasoline engine. The Carburetor is old technology – best in its day, but inferior in at this point in time.
It may be true that in some limited applications, CVD coated inserts will run at higher cutting speeds, but the small potential for faster cutting is more than offset by the inconsistencies observed in tool performance from edge to edge, and insert to insert.
Major tooling companies continue to push a plethora of CVD grades into the market place. The main driver of this approach is that the cost of coating inserts by the CVD process is many times less that the cost to coat by PVD. Yet cutting tool companies routinely introduce all types of new CVD coating varieties and layers into the market at higher and higher prices. This approach is a winning strategy for tool manufacturers as they make higher profits and can keep their customers confused and captive with an incomprehensible variety of tool choices. Unfortunately, CVD inserts are almost always a loosing strategy for machine shops.
The significant majority of shops would be wise to confine their tool and insert selections to about 3 different PVD coating options, and eliminate CVD entirely. With this approach, Machinists will better understand tool applications and performance, and focus on correctly applying the tools for each operation. This approach always results in higher overall production rates. If anyone doubts this the advantages of doing this – just take a look at the inventory of solid carbide endmills in most shops. You will find one, two, or perhaps three options (uncoated, TiN coated, and AlTiN/TiAlN coated) Ever wonder why just three options can quite successfully cut all the various operations and materials that need to be milled with 1/8 to 3/4 diameter milling tool?
Be cautious, and don’t study this too hard. The next thing you will start to wonder is why the price of a typical insert is in the mid-teens per insert, when a solid carbide endmill, that has twice as much carbide by weight, and obviously is much more labor intensive to manufacture, costs about half what a normal insert costs. A real puzzle that one.
We have a similar experience with rotary broach tools. Coatings on a rotary broach don’t have the same advantages as with a drill or end mill. The options available are growing. Yet, just TiN and TiCN are still our most popular rotary broach coatings.