Today’s Machining World Archive: April 2007, Vol. 3, Issue 04
The traditional methods of burr removal – by hand, tumbling, vibratory deburring and abrasive blasting – take care of these unwelcome bits of metal most of the time. However, for problem burrs, you may want to investigate other technologies.
According to LaRoux Gillespie, a consultant in Kansas City, Mo., and the author of the Deburring & Edge Finishing Handbook, there are at least 119 different deburring processes, 80 of which are in industrial use somewhere in the world today.
According to LaRoux Gillespie, a consultant in Kansas City, Mo., and the author of the Deburring & Edge Finishing Handbook, there are at least 119 different deburring processes, 80 of which are in industrial use somewhere in the world today.
Hole deburring
Several brands of hole-deburring tools are available. Most have a spring-loaded cutter that mounts in an arbor. The cutter has a taper at the bottom end which deburrs and can chamfer the front side of a hole as it enters. The center part of the cutter is smooth, with edge, so it passes through the hole without damaging the bore. As the tool backs out of the hole, the edged taper at the top of the cutter blade deburrs the back side of the hole.
Deburring tools from E-Z Burr Tool Company, Plymouth, Mich., feature replaceable cutters and can be customized to perform the specific deburring/chamfering tasks you need. Standard sizes run up to two inches, and larger custom tools are available. A drill can be incorporated into the design, as well as a separate cutter for chamfering or countersinking. E-Z Burr also offers a line of Micro deburring tool for holes as small as 1 mm in diameter.
Brush deburring
Specialized brushes can perform burr removal, especially on-machine, where the brush can be included as one of the tools in the tool changer. Weiler Corporation, Cresco, Pa., provides a wide range of engineered brush products, including nylon abrasive filament disc brushes, designed for deburring flat-surfaced parts with multiple surface holes, slots or cavities.
When using brushes, “If you’re looking at automating a deburring application, you typically have three options,” said John Sockman, director of engineered solutions at Weiler Corporation, Cresco Pa. If you want to use a robot for deburring (see “Robotic deburring,” below) you can either take the part to the brush or take the brush to the part. In a horizontal or vertical machining center with live tooling, he said, you can put the brush into the tool changer. Or you can have dedicated equipment to deburr a part or family of parts.
“In a machine deburring solution,” said Sockman, you have to ask, “what is the geometry of the part, what is the burr geometry and what is the work material? Can we get filaments on the burr? If the part masks the burr we can’t do it.”
Sockman pointed out a particular advantage of deburring parts at the machine: “Single-point accountability for the quality of the part. It is relatively common in high volume [production] for the operator to be responsible for the parts, not the burrs, neglecting that there’s a deburring issue downstream [caused by] running too fast or waiting too long between tool changes.”
High force centrifugal deburring (Harperizing)
Harper centrifugal barrel high-energy finishing machines, also known as “Harperizers,” have been around for about 50 years, said David Krupp, president, Chas. G. Allen Co, Inc., Barre, Mass., manufacturer of the machine.
In a centrifugal barrel machine, several cylindrical containers are mounted to a rotating base, which may be vertical or horizontal, depending on the machine. The base rotates in one direction and the barrels rotate in the opposite direction. This generates high forces so that the centrifugal barrel machine can deburr and finish parts in a fraction of the time required in a conventional vibratory or barrel finishing machine. In spite of the high forces produced, the action of the finishing media on the parts is gentle enough for critical small medical parts like “little stents and tiny biopsy pincers,” said Krupp, as well as larger parts.
Centrifugal disc finishers
Another type of high-force finishing system is the centrifugal disc finisher. This type of unit provides a container in which you place your parts and finishing media. A disc at the bottom of the chamber rotates rapidly, causing the contents to rotate and move outward toward the wall of the container, up and back down again.
The forces produced are nearly as high as those in a centrifugal barrel finisher, said Tony Kenton, president of Nova Finishing, Inc., Huntingdon Valley, Pa., manufacturer of small centrifugal disc finishing units. Finishing time in a centrifugal disc finisher is a small fraction of that required by more common deburring methods. The Nova website gives an example: “For every 100 minutes a standard barrel tumbler operates at 1g ( gravity/ pressure ) a vibratory system will produce the same results in 10 minutes at 8g’s and a centrifugal disc equals 1 minute at 24g’s.” Here, “g” indicates the acceleration due to gravity, used as a measurement of relative force produced.
Centrifugal disc finishing lends itself to many small-part applications in industries such as automotive and medical devices. Extremely small parts may not work, however, as there is a gap between the disc and the container. “On a disc finisher the determining factor is the gap between the disk and the wall. The standard dimension is 0.020”, and you can get [units with] 0.005,” Kenton said.
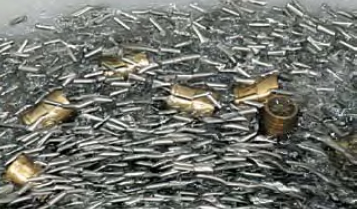
Magnetic deburring
Magnetic deburring offers another alternative to traditional methods. “What we do is we excite tiny magnetic pins in a magnetic field,” said Greg Webb, vice president of sales, Earth-Chain USA, Indianapolis, Ind., manufacturer of the sPINner deburring system. “This creates a deburring action on small precision parts,” including their inside diameters, without damaging the surfaces or removing stock.
You place your parts and the stainless steel pin media in the deburring container, add the deburring solution and turn the unit on. As the magnets beneath the container rotate, the pins circulate and jump about, striking the parts inside and out. The deburring solution is a soap and water mixture, which helps to suspend the pins during the process. Parts made of magnetic materials may need to be fixtured within the deburring chamber. Average cycle times are 10 to 20 minutes, Webb said.
Applications include “anything coming off a Swiss-type [screw machine],” Webb said, typically parts 2” in size or smaller. The sPINner units are available in different sizes, including one that is mounted on casters and can be brought to the machine as needed.
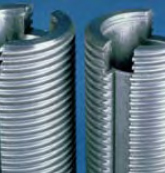
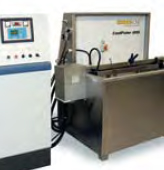
Electrochemical machining
Electrochemical processes may be thought of as “reverse plating,” where material is removed from the part rather than added to it, explained Jim Koroskenyi, electrochemical machining business unit manager at Extrude Hone Corporation, Irwin, Pa.
Electrochemical machining (ECM, not to be confused with EDM – electrical discharge machining, a spark erosion process) may be used for deburring. Koroskenyi described the process: You use a tool the shape of the edge you are deburring. The tool and the part are immersed in an electrolyte solution with a gap of 20 to 30 thousandths between the tool and the edge being deburred. The tool is made negative, the part positive, and current flows. The part material nearest the electrode dissociates, causing the metal to migrate out into the electrolyte. There it forms an insoluble compound, which precipitates out of the solution. The tool is not affected by the ECM process.
ECM deburring usually takes only 10 to 30 seconds, maybe a little longer if the edge needs to be broken. Multiple parts can be fixtured in an ECM system to be deburred at the same time. Deburring is done quickly and inexpensively at room temperature and does not consume the tool. However, for conventional ECM, deburring, you do need that customized tool for each part.
In addition to the large ECM systems used in a shop’s deburring area, small ECM systems can be used on the bench next to a screw machine for on-the-spot deburring.
A new type of ECM
Extrude Hone has developed a new ECM technology, CoolPulse, which overcomes some of the limitations of conventional ECM. In the CoolPulse system, parts are suspended between two metal plates immersed in a proprietary electrolyte − you don’t need a part-specific tool. The electrolyte solution is optimized for edge effects, so that the CoolPulse process “finds” the sharp edges that need to be deburred or radiused. It can also reach inside holes up to about half the hole diameter.
The process takes perhaps one to three minutes, said Koroskenyi. While it deburrs, the CoolPulse also polishes the part’s surfaces. This new technology is ideal for small precision medical-industry parts, Koroskenyi said, such as the miniature tools used in laparoscopic surgery.
Abrasive flow machining
Probably the most ingenious deburring technology available today is abrasive flow machining (AFM) from Extrude Hone. Invented in the 1960s for the aircraft industry, AFM uses abrasive grains embedded in a polymer material. The process can finish complex surfaces, removing burrs and leaving a very smooth surface, even in areas that are completely inaccessible to conventional deburring and finishing methods. “We take a puttylike substance filled with abrasive [and flow it] back and forth,” said Tom Kohut, vice president, abrasive flow machining division at Extrude Hone. “It acts like a grinding wheel,” but conforms to any surface shape. “You can achieve surface finish improvements of 90 percent,” said Kohut. “Starting with 100 [Ra] you can easily take it down to 10. . . We have generated surface finishes under one micro-inch.”
AFM finds application in a very wide range of industries, anywhere superior surface finish is required, and especially among parts that are difficult or impossible to deburr and finish by more conventional means. In the diesel industry, for example, Kohut said, AFM is used to treat fuel system components. It’s not uncommon for pressures within a diesel engine fuel system to exceed 30,000 psi, he said, and any sharp edges or burrs on holes act as stress raisers and can cause failure.
Ultra-pure applications in the pharmaceutical and semiconductor industries make use of AFM to finish tubing, valves and other components to smooth surfaces so they can’t harbor even microscopic amounts of contaminants. AFM also imparts ultra-pure surfaces to implantable medical devices such as heart valves and knee joints. In a lot of these applications, even a 10 Ra finish from machining leaves too much opportunity for contaminants to stay on the surface. Other applications include automotive manifolds and heads, and rotating parts in aerospace applications. “In one particular [helicopter turbine] engine,” Kohut said, “we do 21 different components.” The smallest holes processed with AFM were 40 microns in diameter, he said, and the largest part was “in excess of 10 feet in diameter, with 320,000 holes under 1/4” [diameter].”
Extrude Hone sells AFM and other deburring/finishing equipment and also provides contract finishing services at plants located in different areas of the country.
Thermal energy method
The thermal energy method (TEM) is another problem-solving technology available from Extrude Hone. TEM uses the energy from ignition of a fuel/oxygen mixture to “burn” off burrs anywhere on the part, even in small, deep holes or passages. It also removes stray chips from the part.
The parts are placed in the TEM chamber, which is then tightly sealed. The chamber is filled with a mixture of oxygen and a fuel gas such as natural gas or hydrogen. “The gas goes into all the nooks and crannies of the part. When it is ignited, burrs or chips are oxidized,” said Koroskenyi. The part absorbs any remaining heat energy. The amount of fuel/oxygen is determined based on the burrs to be removed, and other factors, to provide enough heat to take off the burrs, but not to harm the part.
“Many parts can be put into the chamber at the same time. Very often, small screw machine parts can be bulk-deburred in a basket,” said Koroskenyi. Fixturing is required only for parts that need protection from nicks or scratches, such as those with an O.D. thread, or finish-turned surfaces.
Where does the burr material go? “You’ve converted the burr into an oxide, which resettles on the part,” explained Koroskenyi. The oxide is removed from the part during subsequent heat treating or plating, or you can use a simple cleaning process. “Basically [TEM] converts the burr into something you can wash off the part,” said Koroskenyi.
Robotic Deburring
For some applications, using a robot to deburr a part may make sense for complex edges that retain burrs, parts that will be in high volume production for a long time, and where close tolerances are not required.
You have to profile every edge that has a burr if you are using a robot, author Gillespie pointed out. He recommended using flexible tooling, and providing for the tool to back off when it encounters a surface it doesn’t expect.
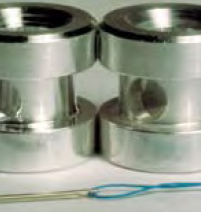
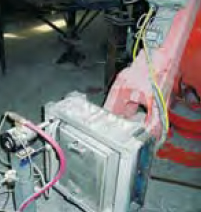
Turbo-abrasive machining
Turbo-abrasive machining (TAM), an innovation of Turbo-Finish Corporation, Barre, Mass., gives a fine, isotropic surface finish to complex rotating parts for the aerospace and other industries. Available through Chas. G. Allen Co, Inc., Barre, Mass., TAM machines rotate a part in an aerated bed of abrasive. For most parts, all surfaces can be deburred and finished without special fixturing or hand work. Non-rotating parts can also be finished with TAM if they can be appropriately fixtured in the machine.
Controlling your burrs
Burrs that are small and consistent in size help all these deburring technologies to do their job. Even better are the burrs that aren’t there and don’t need to be removed. Consider the following concepts and suggestions from Gillespie and his Deburring & Edge Finishing Handbook.
• While there may sometimes be a burr created where the tool enters a part, there will always be a burr where the tool exits the part, if the part is made of a ductile material.
• Sharp tools and appropriate feed rates can help minimize the size of burrs.
• Plan the machining steps to minimize burrs. Burrs generated in one cut may be removed by a subsequent operation.
• You may be able to machine a part to create the burr where it is easy to remove, or does not interfere with fit or function (in which case it may not need to be removed).
• When turning, you can use a form tool to minimize the number of burrs.
The size, condition and location of burrs affect whether your chosen deburring technique will work. “You have to understand that if the burr is larger, it is harder to remove,” said Sockman. To help quantify the range of burrs, his company, Weiler Corporation, has a classification system for burrs, rating them from one to five, depending on how large the burr is and how it is attached.
Since burrs are a fact of life in the machining business, Gillespie recommended having a written standard, so you and your customers all know what you mean by “burr free.” This needs to include the inspection procedure, so you’re not saying “burr free to the naked eye,” while your customer is thinking, “burr-free at 40x magnification.”
Though many deburring technologies may seem to work wonders, they won’t perfectly remove just any burr. New users of an automatic or mass deburring system are often disappointed, until they learn what it can and cannot do, said Koroskenyi of Extrude Hone, echoing the comment of others in the deburring business.
“When the machine arrives, they think they can cut faster and use the tools longer, because they have a ‘magic deburring machine,’” said Koroskenyi. “This is one of the most important things for a customer to realize: there’s no magic out there.” Deburring systems “have limitations. For customers to automate deburring, it means they have to pay attention to the machining side, make the burrs as small as possible, and uniform − stay in a relatively narrow range.”
No, they’re not magic. But when integrated as part of your machining process, these deburring technologies can help improve product quality, customer satisfaction and your bottom line.