By Barbara Donohue
Direct Part Marking (DPM) with a laser offers a way to permanently identify parts for tracking, tracing and control.
In medical, military, aerospace and other applications where safety or security are especially important, more and more manufacturers and end users are requiring permanent identifying marks on individual parts to aid in traceability in case there is a problem or failure in the future. Individual part marking is also becoming a standard practice in many non-critical applications to enable automated inventory control and other functions. “Eighty percent of the time marking is customer driven. The customer says, ‘You have to do this,’” said Kevin Warman, co-president at Kevron, Inc., Louisville, Colo., a manufacturer of laser marking systems.
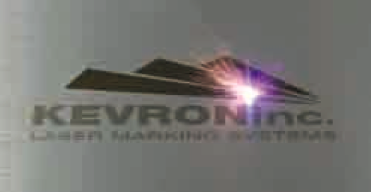
Marking, scanning and tracking individual parts in-house can help with monitoring work in process and staging parts for operations on different machines, and the ability to track individual parts and assemblies through manufacturing can be invaluable in troubleshooting when errors occur.
The U.S. Department of Defense (DOD) has played a role in the increasing use of laser marking and other identification technologies. The DOD now requires Item Unique Identification (IUID) for all tangible property valued at $5,000 or more. The unique identification code must be marked directly on the item or permanently attached, and must withstand the same environmental conditions as the item. The data required in the mark typically includes the manufacturer and part identification—such as a part number and/or serial number.
Making Your Mark
You have many options for labeling parts or assemblies. Direct part marking (DPM) involves marking on the surface of the part with laser, ink jet, chemical etch, dot peen or bonding processes. You can also attach labels, but they tend to be more expensive, and the labels can fall off. For machined metal parts, laser marking directly on the part offers speed and permanence not available with other methods.
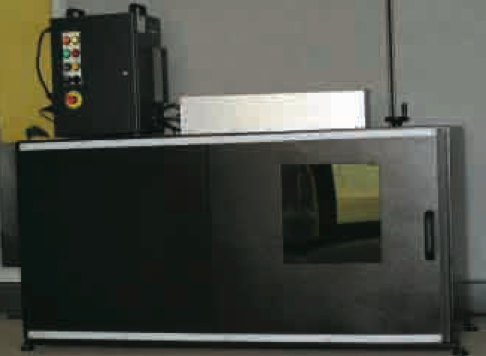
Of course, you could program any CNC machining center to mill names, numbers or symbols on a part, said Ron Quinlan, co-president at Kevron, Inc. However, part marking may not be the best use of an expensive machine. You could send parts out to a laser-marking shop. Or, you might find it cost effective to set up a laser marking station in your shop to take care of all your part-marking needs.
Some forward-thinking machine shops have their own laser marking equipment, Warman said. “If they treat it as [they do] their CNC machines or lathes, it becomes a profit center.” They can offer laser marking to their machining customers as a value-added option, and can also sell contract laser marking services to others. Most shops can make their own fixtures so they can process multiple parts at once, Quinlan said. A shop might charge $60 to $100 per hour for the laser marking machine. So if marking a particular part takes 20 seconds, that works out to 33 to 56 cents per item marked.
Lasers at Work
Laser marking can be done in a number of ways. A laser can engrave lines or other shapes into the material, it can remove paint or another type of coating to allow the underlying material to show, or it can cause a color change in the desired pattern on a surface by a localized annealing process.
Engraving vaporizes some of the material, creating visible dimples or grooves in the surface of the part to form the desired shapes. The laser can produce textures, labels, ornamental designs or identification marks such as data matrix codes. One shop that machines the heads for golf clubs, customizes the heads by laser-engraving them with names, dates and other information relating to a particular country club or tournament, said Scott Wolfson, president, All-Marks, LLC, Reseda, Cal., a supplier of laser marking equipment.
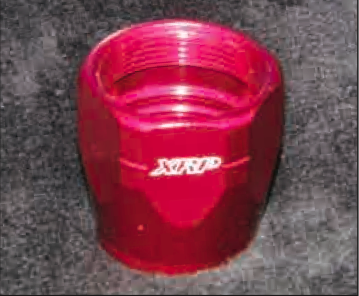
For parts that need a visible mark but cannot tolerate any grooves or roughness, the annealing method uses the laser to locally heat the surface of the metal so it changes color. Bright steel turns black. Aluminum turns white. This approach leaves a visible mark but does not affect the surface finish or other properties of the workpiece. It is often used for marking medical instruments or implantable medical devices, where there must not be any grooves, holes or porosity to harbor bacteria. As with other aspects of the manufacturing process for medical devices, the marking method also needs FDA approval.
Data Marking
Two-dimensional (2-D) data matrix codes are often direct- marked on parts. A data matrix consists of an array (or matrix) of many rows of light and dark blocks. Several different types of data matrix have been invented. A common 2-D format used for laser marking consists of a square array, which has all dark blocks along two adjacent sides, which appear as solid lines, and alternating light and dark blocks on the other two sides. This configuration enables the reading device to determine the correct orientation of the mark. A 2-D matrix is scalable in size to meet the needs of the product on which it is marked, said Wolfson. “We have laser- marked a data matrix on the head of a pin and put one on the side of a freight train.”
When you set up a laser marking system to mark a part, the desired data is encoded in the matrix by the software of your marking system. When the mark is read, the reader essentially takes a picture of the 2-D matrix and the reader software determines the meaning of the combination of dark and light blocks.
You could also mark parts with the familiar one- dimensional bar codes, similar to the Universal Product Code (UPC) bar codes seen on supermarket items. However, a data matrix can contain 100 times as much information as a bar code, in one-quarter of the space, said Kyle O’Brien, product manager with Microscan, Renton, Wash., a manufacturer of automatic identification and machine vision solutions for ID tracking, traceability and inspection.
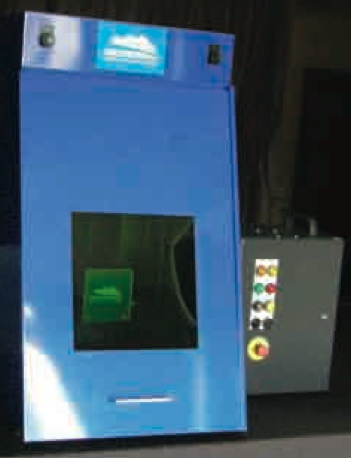
Check It Out
Customer specifications may require you to verify the marking on the part. Over time, any part marking system may drift, producing marks that become progressively more difficult for readers or scanners to interpret. A verification system scans the mark and rates its quality—how closely it matches the specification for that particular type of data mark. A basic verification system runs about $5,000, O’Brien said. For comparison, a handheld reader capable of interpreting 2-D matrix marks might cost about $500. Some laser suppliers offer laser marking and mark verification systems together on a cart that can be rolled about the shop.
Safety
Even relatively low-powered lasers can cause burns or eye damage, so self-contained laser marking systems include an enclosure around the working area, with interlocks that prevent the laser from operating when an access door is open. In many systems, a heavily tinted window allows you to view the laser at work.
Since the laser is heating and maybe vaporizing material to make the mark, fumes come off the workpiece. These must be removed with a suitable fume extraction/filtration system.
Ready for Lasering
Vendors specializing in laser marking can provide you with a self-contained marking system that includes the laser, its power supply and controller, a protective enclosure, software to control the process and a computer that runs the software. Several different kinds of lasers can perform marking operations. When selecting a system, be sure to investigate any special power or cooling requirements. Find out what normal maintenance is required and whether the laser head is likely to require any adjustments over time. Also, ask about the expected service life of the laser head and how much replacement will cost.
Typical standalone systems available from All-Marks use a 10- or 20-watt pulsed fiber laser, Wolfson said, and include a light-tight enclosure. The cost for such a system would likely be $40,000 to $50,000, he said, depending on the power of the laser and whether you choose a simpler or more sophisticated enclosure. Leasing may be available, with monthly payments in the range of $825 – $1,000, he said.
Laser marking systems these days don’t have much of a learning curve, according to Wolfson. When asked what it’s like getting started, he said, “If we sell a laser and take it in to a customer and teach the people [how to use it], we’re gone in two hours, including having a cup of coffee.”
If there is enough space to install a laser head and the necessary safety guards inside a machine tool or other manufacturing equipment, you may be able to integrate automated laser marking into your process. Some laser heads are quite compact; for example, the head from Kevron is about 15 x 5 x 4.5” (381 x 127 x 114 mm).
Whether you partner with a contract laser-marking shop, or decide to purchase your own marking equipment, laser marking can be a valuable addition to your manufacturing capabilities. And once you have marking in-house, you may find that marking and tracking parts and tools within your shop can help you improve your process flow and maintain consistent product quality.
1 Comment
Pingback: The Top Three Features To Seek Out When Purchasing A Laser Device – laser cutter metal