By Barbara Donohue
Today’s Machining World Archives January/February 2011 Volume 7 Issue 1
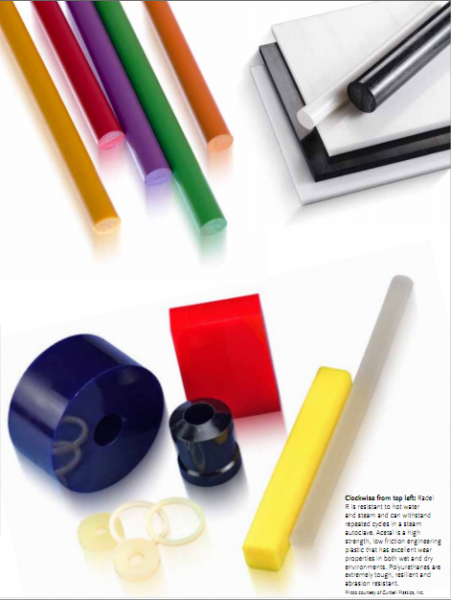
Plastics can behave in mysterious ways, but a lot of shops machine them successfully.
Machining plastic is another technology often regarded as a black art by those who don’t do it. Imagine trying to machine a part to print in a material that changes size and shape as you work it (and sometimes afterward), chips or melts as you cut it, and cracks when you squirt it with your usual degreaser. No wonder many shops accustomed to cutting metal don’t want to deal with the wide range of mechanical properties and the sometimes strange behavior of plastics.
O’Brien Consolidated Industries, Inc. started out machining metal, said Jeff Parisi, a manufacturing engineer at the Lewiston, Maine, shop, but when one of their biggest customers asked if they could make some insulators from Teflon, they gave it a try. After that they quoted jobs in plastic. “Now we do 13 different kinds,” Parisi said. At trade shows, people see the plastic parts on display in the company’s booth and they stop to ask what plastics they have worked on, Parisi said. “A lot of it is our being willing to try out the different plastics.”
You have to deal with each plastic on its own terms. “Some like to be climb milled, some conventionally,” he said. “Some, like the acrylics and polycarbonates, are very brittle and crack easily. Some cut just like metal.”
Here is a brief tour of some things you need to consider when working with plastics.
Thermal Expansion
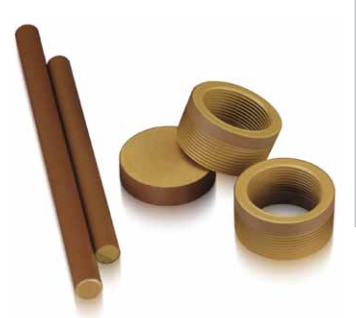
Just about any material “grows” as it gets warmer. When you’re machining metals, this is not usually an issue. However, some plastic materials expand at five times the rate of metals, or more. Over the same temperature rise, a part made of UHMW (ultra high molecular weight polyethylene) will expand 10 times as much as a similar part made from aluminum.
So if you machine UHMW in your cool shop in Minnesota and send it to your customer in sunny Phoenix, it’s likely to get rejected. A foot-long UHMW part machined and inspected at 65 degrees will measure about 0.046” longer when it reaches its destination where the temperature is 100 degrees.
Though it would make sense to specify the temperature at which a plastic part is inspected on the drawing, Keith Hechtel, director of business development, Curbell Plastics, Inc., Orchard Park, N.Y., said he has never seen such a temperature spec.
Moisture absorption
Some plastics absorb moisture from the air, which causes them to grow larger. Nylons are known for this. “If you machine a part in New Orleans and put it on the shelf in a nonclimate- controlled area, it will be out of spec after a while,” Hechtel said. If you’re working with a moisture-absorbing material, keep it in an air conditioned room, or seal it in a plastic bag that allows little moisture transfer.
Residual stress
The processes used to form your plastic stock tend to produce residual stresses in the material. Extrusion leaves stress in plastic, and so does the cooling process—the outside cools faster than the inside, leaving a lot of residual stress in the surface, Hechtel said. When you machine the plastic, the residual stress can make the workpiece deform as you remove material.
Annealing (gradual heating and cooling) relaxes and removes residual stress. You can often purchase annealed, stress-relieved plastic stock. If you invest in your own annealing oven, you could rough out blanks and then anneal them before finish machining.
Reaction to chemicals
“The material may resist chemicals at room temperature,” said Hechtel, “but raise the temperature a little and you can get cracking and crazing.”
Acrylic or polycarbonate plastics, widely used as transparent windows and covers, tend to have poor chemical resistance. Hechtel told of a “beautiful acrylic greeting card rack made for our biggest customer.” It was ready to ship when someone wiped it down with acetone to clean it, causing the acrylic to craze.
In one case, a bullet-resistant polycarbonate window had long cracks growing up from the bottom. It turned out that the person who had cleaned the window every night used Windex, and the cleaner pooled at the bottom in the uchannel that supported the window.
Be very careful what chemicals you use with plastics. Consider using clean compressed air as your coolant. “Some water-based coolants are pretty benign,” Hechtel said, but best to consult your plastic and coolant suppliers to determine whether the materials are compatible.
Workholding
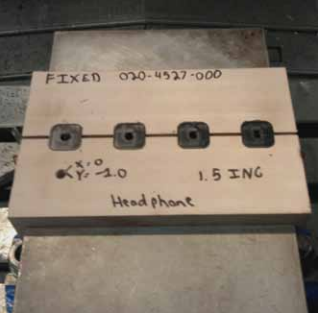
You have to be careful in workholding, as “obviously, the material is much softer and more delicate than metal,” said Mike Morris, president, American Plastic Fab, Brookneal, Va. It deforms if you clamp down on it too hard. But you can easily make soft jaws from a plastic material such as Raku- Tool modeling and tooling board, he said. You mill the shape of the workpiece into the jaws, so you can nest the part right into the jaw. Then, because the soft-jaw material is machinable, you can mill down into the jaws if needed.
With workpieces that have a flat surface, you can use a vacuum chuck. The advantage of this is you can pull the vacuum and profile the whole part—all four sides and the top.
“Remember, you don’t have the cutting forces you have with steel,” Morris said, so the workholding method doesn’t have to clamp as hard and you can get creative with how you secure the workpiece.
Feeds and speeds
You can’t talk generally about feeds and speeds in plastic machining because there are so many different plastics with disparate characteristics. You have to play with the combinations.
“Keep trying to speed it up until something happens you don’t like. Then back it off just a notch. All machining is like this,” Morris said. “It’s a problem solving thing. If you’re not getting what you want, you have to figure out what to do to fix it.”
Chip handling
“Certain materials have horrendous chip problems,” Morris said. “Nylon is bad—long stringy chips. UHMW is worse.”
“You can use roughing end mills—the geometry of the cutter breaks up the chip,” Morris said.
With plastics you do have a lot of flexibility with feeds and speeds. “With different feed and speed, you can generate any kind of chip you want. Make a big chip that throws right off the tool. If you’re drilling at 1000 rpm and five inches per minute, try slowing down to 500 rpm and increase the feed rate to 10 inches per minute,” said Morris. “That will give you a chip that fills the flute, and when [the drill] pecks, the chip flies across the shop.”
Phenolics and glass-filled plastics produce a lot of dust that can be irritating. You need to provide dust collection or cut with coolant to keep the dust down.
Tools
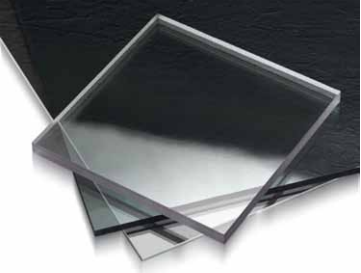
“Generally tools don’t fail,” said Morris, “except on glassfilled materials, which are abrasive.” In most cases, he can get away with lesser quality for tools such as drills, he said, “but you do have to buy the standard good-quality inserts to get that nice smooth surface.”
“The difference between plastic, metal and wood tools is actually the rake or angle the tool is sharpened,” said Victor Miranda, president, American Woodworking Equipment Distributor, Suwanee, Ga. Otherwise, the tools are much the same. His company offers a line of end mills and reamers for plastic machining applications where a polished finish is required.
Look for tools specially designed for cutting plastic, such as No-Melt saw blades from Forrest Manufacturing Company, Inc., Clifton N.J., and Plexi Point drill bits from FTM, Inc., Placerville, Cal.
Plastic is not metal
One of the reasons metal shops don’t like plastics, Morris said, is because you can’t do things the “normal way,” the way you would in metal. “I grew up in a plastics shop, so I wasn’t contaminated with such ideas.”
Plastics can be so challenging—there are so many variables, Morris said. “Sometimes we’ll have to machine it out of tolerance because we know it will relax and go into tolerance.”
“Say I’m doing a UHMW bushing, hogging out all this material,” Morris said. Stresses that remain in the material from its manufacturing process will make the part move. “Make one and set it aside” to see what it does. One lot of material will be fairly consistent, he said, but the next batch may be slightly different.
“We’re a machine shop willing to do different materials,” Parisi said. Some don’t like changing over and cleaning out the machine between jobs, he said, but that’s what makes it possible to cut aluminum and plastic on the same machine.
Help your customers
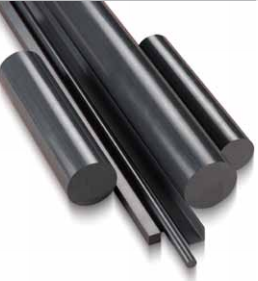
“A very common situation is engineers who want things in plastic that were really designed for metal. You have to tell them it’s not possible in plastic,” Morris said. On a 10-footlong UHMW part one of his customers wanted to hold eight thousandths tolerance from the first hole to the last, which, of course, wasn’t going to work. “You can’t change physics,” Morris said. “Instead of holes we made slots; it was still a functional part. You have to design around the qualities [of the material].”
Sometimes customers will want to use a particular plastic because it’s inexpensive. But it may not be so machinable. You can recommend a different material, as Parisi sometimes does. “For just a few pennies more we can make [the part],” he said.
In some ways, machining plastic is a black art—there are so many variables you have to deal with. However, experience and the advice of plastic suppliers and other experts can take a lot of the mystery out of it.