Today’s Machining World Archive: March 2008, Vol. 4, Issue 03
Relief when you need material that is out of stock – or doesn’t exist.
When you’re going to make a part for a customer, you usually just look at the drawing and order the material from your supplier. Then it shows up on your dock and you can start making chips.
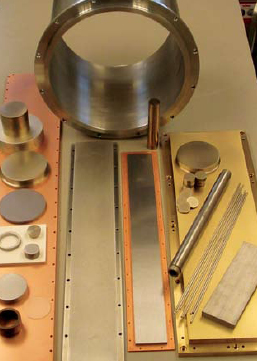
But sometimes it’s not that easy.
Sometimes, for performance or machinability, you need to source a high-purity version of an alloy or a precision form of the material. Sometimes, a customer may specify a material that is out of stock everywhere, with a 40-week lead time, or maybe the mills just don’t make that particular alloy anymore.
Occasionally, perhaps for a brand new application or for a super-high-performance part, none of the available materials will do the job. Your customer may work with a company that specializes in custom alloys to develop a new alloy to meet the requirements of the application.
Unique alloys
Sophisticated Alloys, Butler, Pa., has melted just about every imaginable kind of alloy, from ordinary ones that happen to be unavailable from stock, to specialized magnetic alloys used in computer disc drives, to reactive solders, to high-temperature materials used for coating jet engine components. Company president Jim Patterson said once he even worked with a cinematic special-effects expert to provide a metal that was liquid at room temperature for a particular movie.
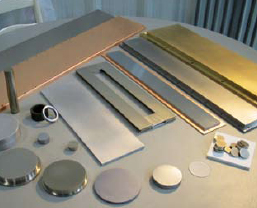
Orders usually range from a few pounds to a few hundred pounds, said Patterson, though sometimes a client wants only a few grams for research purposes. “We’re a place of first choice for some people, or of last resort [or others],” he said.
Starting with high-purity raw materials, Sophisticated Alloys prepares alloys in one of five vacuum induction melters, the largest of which has a capacity of 400 to 500 pounds. “What we do is make any type of alloy you can think of. We don’t stock any materials except raw materials,” said Patterson.
One of Sophisticated Alloys’ specialties is sputtering targets. Sputtering is a type of physical vapor deposition process that lays down a very thin layer of a material on a part or substrate. In sputtering, a cathode, or “target” made from the desired coating material is bombarded with ions. This causes atoms or molecules to come off of the target, and then attach themselves to the part being coated. Sputtering is used to place the metalized layer on compact discs, add anti-reflection coatings to optics, deposit thin layers of material during semiconductor fabrication, and in manufacturing many other products.
Designed to order
A custom-alloys house works with clients to develop materials that have the properties needed for specific applications. “We know the addition of different alloying elements can do different things,” said Susan M. Abkowitz, vice president, technology and operations, Dynamet Technology, Inc, Burlington, Mass. Dynamet Technology specializes in titanium alloys produced from powdered metal.
A client might say, “We like titanium, but would like it to be stronger at higher temperatures.” Another might want better wear resistance or higher stiffness. In some medical applications, the desired quality is lower modulus of elasticity so the titanium alloy will more closely match the mechanical properties of bone.
Dynamet Technology’s process produces full-density, near-net-shape parts from powdered metal mixtures through a process of cold isostatic pressing, sintering and then hot isostatic pressing. Working with powders allows the creation of novel materials, Abkowitz said, some of which could not be made by melting methods. In addition to near-net-shape parts, the company also can provide material in bars or other forms.
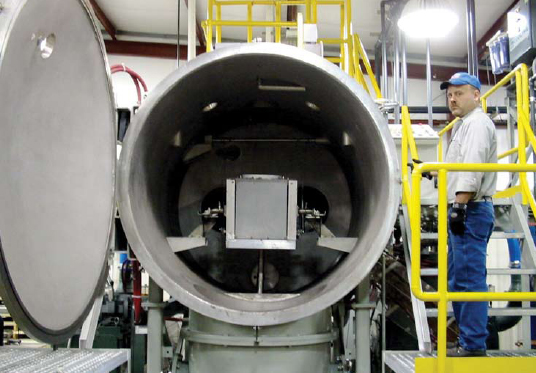
Composites
Besides Dynamet Technology’s range of new titanium alloys, the company also uses powdered-metal techniques in designing and producing the CermeTi family of titanium metal matrix composites.
One type of composite is made from titanium and tiny particles of titanium carbide, a ceramic similar in properties to tungsten carbide. The resulting composite material has improved wear resistance over titanium metal. Different formulations of this titanium/titanium carbide material are being used in and developed for an extremely diverse range of applications: In medicine, CermeTi composites can be used to fabricate orthopedic implants with wear-resistant surfaces, as well as titanium’s excellent biocompatibility.
In the aluminum casting industry, CermeTi composite shot sleeves withstand the flow of molten aluminum for 10 to 15 times longer than the tool steel components they replace. The composites can even be used in sporting goods. Hockey skate blades made from a titanium/titanium carbide composite will stay sharp longer than blades made from conventional materials.
Machining custom alloys
Sophisticated Alloys provides customers with the alloy they want in the form they want it. Some parts are shaped on EDM machines. Some are machined. Patterson has a number of machine shops he depends on. “These materials [can be] difficult to work with. I need to find machinists that are flexible… and able to work in these materials. [They] have to be able to think on their feet.”
Often, because customers need the parts to be super-high-purity, the machining requirements may seem downright strange. For example, to prevent contamination, some sputtering targets destined for the electronics industry, need to be machined with isopropyl alcohol as the cutting fluid. “You’ve got to be really [aware of] what your customer wants,” said Patterson. What you normally do may not work.
Some of the products from Sophisticated Alloys contain costly metals such as platinum, so when they’re in the machine shop, it’s important to collect and save the chips, and to keep the blanks, parts and chips secure from theft.
Composites can pose their own challenges in the shop. Though Dynamet Technology’s composite parts are made to near-net-shape, they do require finish machining. The material looks like titanium, Abkowitz said, and can be machined with conventional uncoated carbide tools.
But the carbide particles in the composite tend to cause increased tool wear. Grinding, honing, and water-jet cutting work well with these materials, she said.
Obtaining the unobtainable
Do you need bar stock in an odd size? Did your customer specify an obsolete alloy for a mil-spec part? Did you try to order material for a job, only to discover it’s out of stock, and you would have to order 20,000 pounds from the mill and wait nine months to get it?
About four years ago, when the metals market got very tight, said Lewis A. Weiss, president of All Metals & Forge, LLC, Parsippany, N.J., he started hearing from customers who were desperate to get the material they needed to run jobs. “Is there anything you can do?” they would ask.
All Metals & Forge is a stocking distributor of metals, from carbon steel to superalloys, and provider of open-die forging. But Weiss listened to the need, and before long, the company started offering custom melting and custom rolling to provide those hard-to-get materials that customers needed.
Of course, this custom work is not cheap, Weiss said. The price can run $50 per pound or higher. However, with custom melting and hand rolling, metal can be available to the customer’s exact specifications in weeks instead of months. Custom melting might take two or three weeks, and custom rolling another 10 days. “I can produce something that’s unobtainable – in four weeks,” Weiss said.
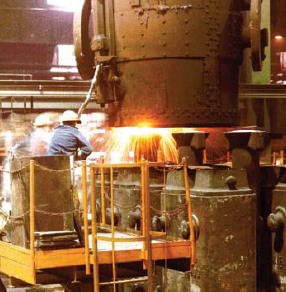
Or sometimes sooner. In one case when an oil drilling operation had to stop due to a broken part, All Metals & Forge got the melter to produce a couple hundred pounds of the needed alloy, on overtime. The forging shop turned out the part overnight. Then it went for heat treating. Obtaining that part would normally take months, Weiss said, but this time it happened in days.
When an oil drill is out of commission or a ship is disabled due to a broken part, the cost to the customer can be enormous. A ship sitting idle can cost $150,000 a day, Weiss said. In such situations, fast turnaround is critical, and the cost of the metal is of very little concern to the end user.
Special grades and forms
You may never need a designer alloy, but sometimes perhaps a variation on a standard alloy will improve your process or product.
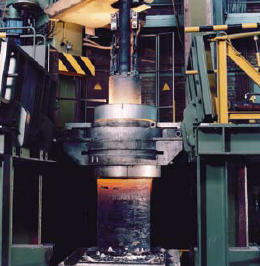
Many suppliers offer special-purpose materials and services. For example, Schmolz + Bickenbach (formerly known as Ugitech USA), Doylestown, Pa., has a line of “screw machine quality” (SMQ) bar stock that has better diameter tolerance and straightness than mill-run bar, at less additional cost than centerless grinding. Bar ends can be ordered chamfered or pointed. The company also makes this type of bar in special UGIMA XL alloys, which offer ease of machining and guaranteed lot-to-lot consistency.
For applications that require superior toughness or polishability, such as dies for die casting or molds for plastic, you can get tool steel that has been remelted to improve its purity, uniformity and microstructure, according to John Stocker, technical director at Schmolz + Bickenbach. The electro-slag remelting process available from his and other companies, for example, uses a layer of molten alumina or other material to capture impurities as an ingot is melted. After remelting, the material ends up more uniform than it was after the initial melt.
You can get what you need
There’s a lot happening out there in the world of materials. You may be able to gain an edge over your competition when bidding a job by quickly sourcing the needed alloy, or maybe simply by being able to find it at all. And, if you are ready to deal with the newest types of alloys and composites, that could be a path to increasing your customer base – and your profits.