By Barbara Donohue
Today’s Machining World Archives August 2010 Volume 06 Issue 06
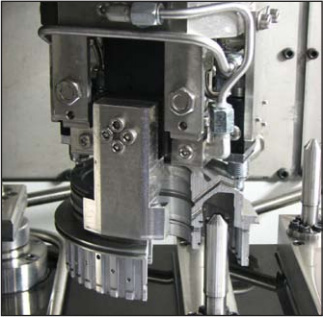
The right parts cleaning system will fit into your process and cost-effectively give you the clean you need. Some systems can even do deburring.
Parts come off your lathes and machining centers covered with oil or cutting fluid and a lot of chips. The customer probably wants nice, clean parts. The best way to clean those parts depends on:
- Part material
- Part geometry
- Debris and soil to be removed
- Cleanliness required by the customer’s specs or for plating or other processes
- Other factors, such as the need to maintain lot integrity
An aluminum or plastic part might require a different cleaning approach than a steel part. A complex part with blind holes or small cavities will be more challenging to clean than a simpler part.
Parts are specified to be visually clean, maybe 50 to 70 percent of the time, said Jeff Brouchoud, president, Alliance Manufacturing, Inc., Fond du Lac, Wisc. Some customers want an “oil break” test—water beads up on an oily surface, but forms a uniform sheet on a clean part. For critical parts, a Millipore test is done, which collects debris from a part and analyzes it for particle size and quantity.
A matter of chemistry
People in the part-cleaning business, talk about the chemistry of the materials used in the cleaning process. Sometimes tap water, deionized, purified or distilled water can do the job. Often, a soap mixture is needed, and sometimes you’ll need to use a solvent.
The chemistry is really important. If your parts are soiled with coolant, chips and oil, you’ll probably use a high-alkaline soap solution, Alliance’s Brouchoud said. But if the parts are made of aluminum and the soap is too alkaline, it can damage or discolor them, so you’d need to use a different soap.
With a given machine and chemistry, you can fine-tune the process by adjusting temperature and processing time, enhancing the cleaning action with ultrasound or agitation, using multiple cleaning baths, or adding stations to rinse, dry or apply an anticorrosion coating.
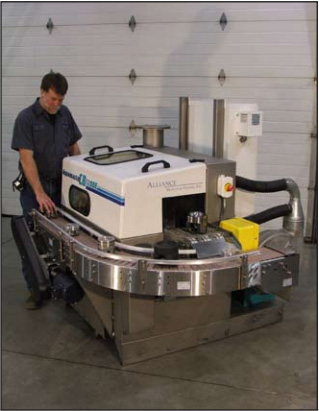
Taking a bath
A common cleaning method is to place parts in a bath of cleaning solution—water-based solutions rather than solvents, these days. Agitating the bath by moving the parts around enhances the cleaning action. Almco, Inc., Albert Lea, Minn., offers a different method, a rotary drum cleaning system in which parts are fed into a drum with helical vanes fitted inside. As the drum rotates, the parts follow the vanes. During part of the process the parts are immersed in the cleaning solution. When the parts emerge from the solution, nozzles spray them to remove oil or debris. The parts exit through the far end of the drum.
Tiny bubbles
Humans—at least the young ones—can hear sounds at frequencies up to 20,000 cycles per second (20 kHz). Higher frequencies beyond the range of human hearing are called ultrasound.
For difficult soils or to achieve cleaner parts, you can use an ultrasonic cleaning system. The parts are immersed in water or a cleaning solution in a tank fitted with sound transducers. An ultrasonic cleaner is essentially “a stereo system in water,” said Frank Pedefous, president of Omegasonics, Simi Valley, Cal. A transducer similar to a speaker emits high frequency sound into the cleaning bath. A frequency of 40 kHz is usually used for cleaning machined parts, he said. Omegasonics designs custom systems and also offers standard systems ranging in size from a tabletop unit with a half-gallon tank to a standalone unit with 110-gallon capacity.
Each oscillation produces a bubble, so at 40 kHz you get 40,000 tiny bubbles per second from each transducer. Each bubble is a low-pressure region within the liquid in the tank. When a bubble strikes the part, it implodes, loosening soil from the part in a very gentle way, said Cheryl Larkin, director of marketing, Miraclean, Ashville, N.Y.
Lower frequencies produce a more aggressive cleaning action, Larkin said, and 25 kHz ultrasound may be used for applications like removing rust or removing mold release from an injection molding process. Higher frequencies—68 kHz up to 132 kHz—provide gentle cleaning, and the smaller bubbles created can get into the confined spaces like screw threads or small passages in parts. If needed, multiple frequencies can be used in multiple cleaning baths.
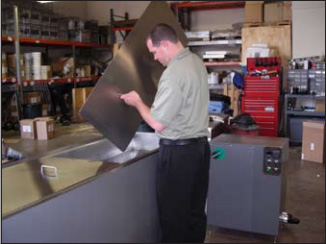
The Sugino U-Jet III cleaning system from Sugino Corp., Itasca, Ill., uses high-pressure water jets in a cleaning bath to create bubbles. The high-velocity flow in and around the parts produces cavitation bubbles, which implode and clean surfaces in a fashion similar to the bubbles produced by ultrasound. The Sugino U-Jet III controlled cavitation system has a workspace of 20” x 10” x 8” and can clean parts weighing up to 22 pounds.
Spray wash
Spray-type parts cleaning systems offer focused cleaning with spray nozzles that aim streams of cleaning solution directly on the parts. With spray cleaning, you have control over the cleaning process, Alliance’s Brouchoud said.
Alliance Manufacturing, Inc. produces water-based spray cleaning systems for batch or continuous conveyor zed processing. With the Aquamate cabinet system you can “put in the parts, close the door, hit the button and walk away,” Brouchoud said. Conveyorized systems, often custom-designed, allow parts to be placed on a belt or fixture at one end and come out at the other end, cleaned and perhaps rinsed and/or dried.
CNC cleans: high-pressure clean/deburr
“We typically sell our machines as deburring and cleaning machines,” said Rich Bertsche, president of Bertsche Engineering Corp., Buffalo Grove, Ill. While typical spray washing systems use pressures of 100 to 2,000 psi, systems from Bertsche use targeted jets of liquid at 10,000 psi or higher, impinging on the part’s surfaces to not only clean, but also deburr difficult-to-reach locations. A CNC-driven ram holds the part and moves it to deburring stations where nozzles direct high-pressure spray at the features to be deburred. Each nozzle is designed to deburr a particular kind of feature, such as a countersink or the intersection of two holes.
Jet Clean Centers from Sugino Corp. also use a high-pressure flow to clean and deburr in a 4-axis CNC configuration. Available in three models providing a range of pressures up to 10,000 psi, Jet Clean Centers also have a 600 rpm spindle that can operate brushes, reamers or other deburring tools for auxiliary deburring. Typical applications include high-precision/high-complexity parts, Sugino sales manager David Becker said, such as cylinder heads, fuel system components, valve bodies for antilock brake systems, or hydraulic valve blocks.
Environmentally friendly solvent cleaning
If the parts you make require solvent cleaning, you could use an environmentally friendly, self-contained washing system. These systems seal the solvent inside, clean it by distillation, and can reuse the same solvent indefinitely. For example, the iFP vacuum parts washers from Gosiger Import, Dayton, Ohio, can operate with hydrocarbon or modified alcohol solvents. You place the parts to be cleaned in a basket and load it into the parts washer system. First, the system removes air from the cleaning chamber. Then, the parts washer introduces the solvent. Ultrasound and/or mechanical oscillation or rotation of the parts enhances the solvent’s cleaning action. You can choose to have a rust inhibitor applied after cleaning and select a heated or unheated drying cycle.
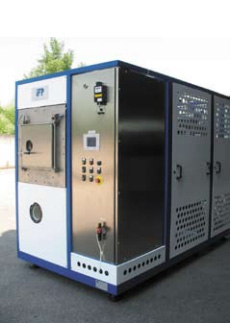
The iFP vacuum parts washer systems come preprogrammed with fifteen preset washing cycles, said Mike Moore, product manager for the iFP unit at Gosiger Import. You can easily program a system to run different cycles if needed. The KP-12 Micro system handles batch sizes up to 25 pounds, and the KP-200, 65 pounds.
A self-contained solvent washing system reuses the sol-vent, but generally requires adding some makeup solvent to replace what is lost in normal operation. “We see about one gallon every 30 days,” Moore said. Using conventional sol-vent cleaning, a shop might expect to buy 150 to 500 gallons of solvent per year, at a cost of $12 to $22/gallon, he said, and then have to pay for removal of the waste solvent.
The right equipment for the job
To get the cleaning results you want, you’ll need the right equipment, the right chemistry, the right temperature, the right cycle times, and the right ultrasonic frequency or frequencies if you are using an ultrasonic system Omegasonics’, Pedefous said.
If you have new or ongoing challenges in cleaning or parts handling, if you run high volumes, or are making parts for which you need to maintain lot integrity, you may want to investigate different systems to see if they can meet your needs more effectively.
When you contact cleaning equipment manufacturers, they’ll ask you to describe the parts—material, geometry, size—and what needs to be cleaned. They also need to know production volume, cleanliness specs, any problems you’ve been having, and other issues you need to deal with, such as lot integrity requirements. Ask the company to run some sample parts through the process, so you can see the results before you buy. To correctly size the machine you’ll need to take into account the size of the parts and also the size of any lots you need to keep together.
Cleaning as part of your overall process
The process flow in your shop may influence the design of the cleaning system. If you want to use a conveyor-type system but need the parts to return to the operator who loaded them, you could use an Almco system that carries parts on a fat stainless steel belt that travels in a U-shaped path, so the parts come back next to where they were loaded. In some cases, robot loading and/or unloading could help streamline your process.
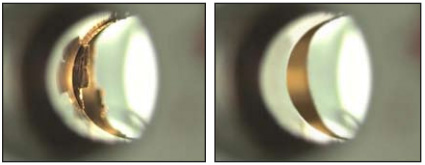
Even if your current cleaning system is working well enough, you may be able to improve it by fine tuning the chemistry, or adjusting the cycle time or temperature. Talk to the system manufacturer or to the company that supplies your cleaning solutions. “It is a good exercise,” Larkin said, “to examine a cleaning process and make improvements to it.”