Today’s Machining World Archive: February 2008, Vol. 4, Issue 02
High-speed spindles crank up the RPM and cut machining time.
What do you do when there’s a step in a machining process that slows you way, way down? That tiny hole in a fuel system part, for instance, or that very long, very narrow groove on an arthroscopic surgery instrument. They can take what seems like forever at the normal speed of your screw machine’s live tooling or even on your machining center, if it’s not the latest, greatest and fastest. And for sure you don’t want to go to a secondary operation – let go of that part and there goes your accuracy, never mind the additional time, handling and cost.
But there is a solution. You can install a high speed spindle to solve these problems, cut your processing time, and eliminate the need for that secondary operation.
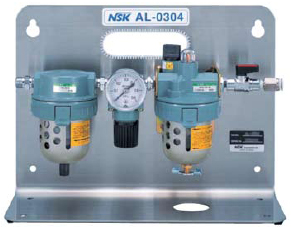
High speed spindles come in small sizes suitable for your screw machine and large sizes suitable for replacing the main spindle on your machining center, and everything in between. They are powered by compressed air or electricity.
High speed spindles are used in many applications, including creating intricate wood inlay work on musical instruments and pool cues, or making detailed molds for jewelry manufacture. They can be installed on the end of a robot arm to do drilling, milling or grinding. Handheld versions can be used for hand-deburring that requires a minimum of effort on the operator’s part. In the Swiss-type screw machine business, medical and aerospace/defense parts are the big applications for high speed spindles, said Greg Nottoli, product manager, NSK America Corp., Schaumburg, Ill., manufacturer of both electric and air-powered spindles.
Suppose your live tooling in your screw machine is limited to 10,000 RPM, maximum, said Bill Popoli, president, IBAG North America, North Haven, Conn.,. “If you can go to 60,000 RPM, theoretically [you can go at] six times the feed,” reducing cycle time. “The tool doesn’t know the difference,” he said.
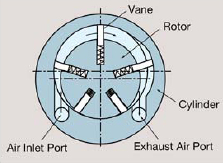
With tools over 3 mm (about 1/8″) diameter, you’ll probably be using the standard live tooling that came with your machine. If you are using smaller tools, less than 3 mm diameter, you’ll probably want a high-speed spindle. And when you use tiny tools, under a millimeter or two, you really do need to run them at high RPM.
Air power
One supplier offers air-powered spindles up to 1.4 HP and speeds ranging from 20,000 RPM to 65,000 RPM. Air-powered spindles can be designed to run at extremely high speeds, some 200,000 RPM or higher. Think dentistry; the hand piece of a dental drill is actually a very high speed spindle.
Air-powered spindles can be quite small in diameter; NSK America offers air spindles down to 17 mm (0.67″) in diameter, for example.
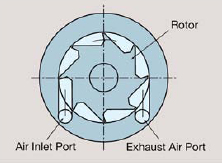
Air spindles are often longer than the same diameter electric spindle, which may be an issue where space is limited, inside screw machines, for example.
Air-driven spindles run best at their design speed. Controlling them means simply turning them on and off using M codes. But all they need to run is a supply of clean, lubricated, regulated compressed air, typically at 90 PSI. NSK America offers an air line kit, which filters, lubricates and regulates the air supply for a spindle.
For lower speed, higher torque applications, the air spindle will likely be powered by an air motor. This has a rotor located off-center in a cavity, with spring-loaded vanes that seal between the rotor and the cavity wall. The pressure of the compressed air turns the rotor. To achieve even higher torque, but at lower speed, some spindles have an internal planetary gear set that reduces the speed and increases the torque. Higher speed air spindles are powered by air turbines, in which air impinging on the rotor blades turns the rotor.
Electric
Electric-powered spindles are available in a huge range of sizes with power ranging from a fraction of a horsepower to more than one hundred; IBAG offers spindles from 20 mm to 350 mm (0.79″ to 13.78″) in diameter.
These spindles require a controller, a variable frequency drive to adjust the speed. You can control it from the CNC with an S code.
To select either type of spindle, electric or air, you’ll need to consider the space available for the spindle, the RPM, power and torque required, the tool size and the material being cut. Application engineers at your spindle supplier will be able to advise you.
What price productivity?
At this point, you may be wondering how much this is likely to cost. You could install a high speed spindle on a screw machine for well under $10,000, one source said. The cost of the spindle would account for probably half of that, and the rest would be the control, wiring, etc.
If you are installing multiple electric spindles in the same machine, you can get a sort of switch box that allows one control to operate two or four spindles. For larger spindle systems, such as an auxiliary spindle mounted on a machining center (see below), the spindle will likely account for about one-third of the cost.
You can easily calculate your return on investment by figuring out how many seconds or minutes you will save when machining the parts you will run.
Life in the high speed lane
Most high speed spindles are now built with hybrid ceramic bearings – the bearing races are steel, and the balls are made of a ceramic material, typically silicon nitride. The ceramic balls don’t fatigue like steel does, and they are lighter in weight. Back in the early 1990s, hybrid ceramic bearings cost several times as much as all-steel, said Popoli, but the price has come down so that now they only cost about 50 percent more than all steel. Increased bearing life makes the extra cost worthwhile, and now hybrid ceramic bearings are commonly used.
Spindles with the hybrid ceramic bearings can be expected to last 4,000 to 5,000 hours in normal service, Popoli said. The failure mode is often breakage of the ball retainers. And by that time, when you take the bearing apart you can see that the races are going bad, too, he said. Some shops try to anticipate failure by measuring the runout on the spindle. When it’s new, the runout might be a few microns. When the runout exceeds, say, 10 microns, this means the bearings are showing wear.
Some users keep a replacement spindle on hand. Rebuilding a spindle can take a week or more. You can calculate the cost of shutting down the machine for that time, and decide whether it is worth the expense of buying a spare.
Your machining center on speed
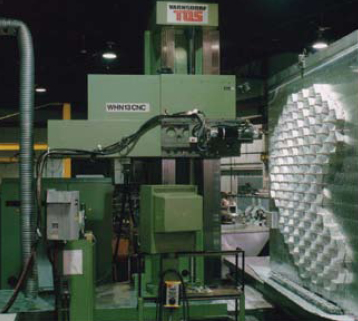
If your machining center doesn’t have high-speed capability, but you need it, you have a number of options:
• You can use a high-speed spindle that mounts into the tool holder, so the main spindle doesn’t rotate, it just acts as a holder for the high-speed spindle. Some high-speed air-driven spindles can be loaded and unloaded by the tool changer as if they were ordinary tools.
• You can have an auxiliary spindle mounted next to the main spindle on the head. This can work well when you need both “normal” and high speeds on the same machine. For example, when machining a mold, you can rough and semi-finish with the regular spindle and do a final finish cut at high speed. When using the auxiliary spindle, you just input the necessary offsets into the CNC control t correctly locate the auxiliary spindle, and machine as usual. (Though this seems as if it should be an economical alternative, by the time you get the auxiliary spindle installed and integrated, it may cost only 10 to 20 percent less than replacing the main spindle, below).
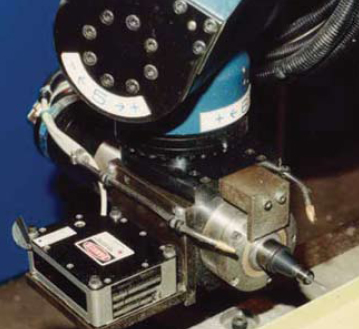
• You could replace the main spindle in the machine with a new, higher-speed version.
If you’re thinking about replacing the machine’s main spindle, start out by looking at a new machine that will give you the speed you require, recommended Paul Frederickson, sales applications engineer at Fischer Precise USA, Racine, WI, a spindle manufacturer. The cost of a new machine might be, say, $250,000, while installing a new high-speed spindle on your old machine could easily total $70,000 to $100,000. Besides buying and installing the new spindle and its control, you will quite likely need to use a different tool retention method for high speed operation, and tool geometries are different for high speed cutting, which would mean updating the tools, tool holders, tool changer, etc.
Evaluate your existing machining center with a critical eye, with regard to accuracy and rigidity. Is it worthy of making a $70,000 to $100,000 upgrade? Also make sure that the machining center and the CNC are capable of accurately producing the higher feed rates that you will need in order to take advantage of higher spindle speeds.
If you decide to install a replacement high-speed spindle, a good starting point is talking to spindle manufacturers, said Frederickson. “The technology is changing all the time.”
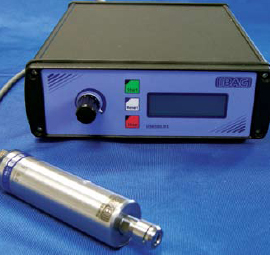
High-speed surprises
There are some things to watch out for when changing over to high-speed machining, said Frederickson. “You may never have had to deal with balanced tooling [before]. Be sure all tooling is balanced and well made. Six thousand RPM is one thing, but at 60,000, you may run into forces and issues you never thought of.” The balance of the tooling is critical at high speed. Small imbalances that you never noticed at 6,000 RPM can make for major vibrations at 60,000.
Also, the resonant frequency of tooling can be an issue, particularly with longer tools. As you run an extended-length tool at higher and higher speed, it may reach its resonant frequency, sometimes with shocking results. John Easley, vice president of sales and marketing at Fischer Precise, recalled one situation in which the customer was milling Styrofoam, basically a no-load application, yet he experienced tool breakage. Because he was cutting with extended-length tooling, at high RPM, the tool reached its natural resonant frequency. And broke. In general, for accuracy and to prevent resonance problems, the tooling for high speed machining should be as short and as rigid as possible.
Most spindle manufacturers will be able to do a pre-analysis for you and forewarn you of any such problems.
High speed spindles available as accessories or retrofits can help you obtain the many benefits of running tools at high RPM, so you can reduce cycle time and eliminate secondary operations without having to buy a whole new machine. Select the spindle according to your process requirements. And then don’t be afraid to use it, even at those super-fast speeds.