Better Than New: Retrofitting a centerless grinder with a new CNC and other components can make it better than it was when it was new.
A machine shop can benefit from retrofitting a manual or CNC centerless grinder with a new computer numerical control via increased accuracy or improved productivity for less than purchasing a new centerless grinder.
A retrofit may be worthwhile even if the grinder is slightly older but working well, because the machine shop will be able to avoid the headache of parts and service becoming less available as the grinder gets older.
A retrofit of a centerless grinder with a CNC, however, goes beyond the operator panel, the control cabinet and their wires.
CNC Retrofit: A Definition
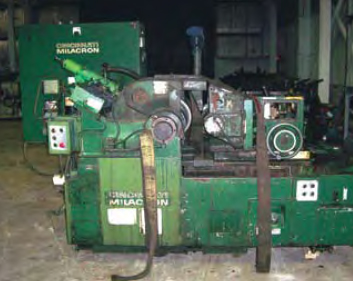
A retrofit is the refurbishing and updating of a machine to include a new CNC. The machine, in this case, a centerless grinder, may already have a CNC, but the control may be older and need updating so the machine can grind more precisely. Refurbishing replaces the machine’s components as needed, cleaning the machine, repainting and testing it.
A retrofit can also include the addition of automation, a robot, for loading and unloading workpieces.
The CNC
A new CNC can add new capabilities to a centerless grinder or improve its existing capabilities.
When retrofitting a manual grinder, an obvious new capability is dressing complex profiles, ones with multiple diameters, angles and radiuses, into grinding wheels without using cams. A manual grinder needs cams, each one manufactured with the shape of a profile or a segment of a profile so its dresser can follow a cam’s shape and thereby dress the shape into the grinding wheel.
In a retrofitted grinder, the CNC can be programmed so the dresser follows the path needed to create the specified profile in the grinding wheel. “On a CNC machine, the computer is cutting that wheel perfect,” said Frank Tarolla, president of the machine shop Aarstar Precision Grinding in Franklin Park, Ill., which had a manual grinder converted into a CNC one.
Replacing an older CNC with a new one can enhance a grinder’s capabilities, too. For example, a new control’s software may make it easier to take advantage of modern technology elsewhere in the machine, such as servo motors capable of motion control of fine resolution. According to Romas Juodvalkis, president of Allways Precision Inc., Plainfield, Ill., a rebuilder of centerless grinders, a CNC centerless grinder retrofitted with modern servo motors may have a motion-control resolution as small as 0.5 microns. New software aids the grinder in making such small moves. “It’s easier for the software to actually handle the motor,” Juodvalkis said.
Installing a new CNC involves replacing the operator panel, the control cabinet and the wiring between the cabinet and the grinder’s five motors and two pumps.
Rewiring ensures the new control can transmit its signals to the motors and pumps, which are connected to the grinder’s main assemblies. “You’re not going to take the chance that you have a damaged wire,” Juodvalkis said.
The motors consist of one connected to the grinding wheel, two connected to the grinding wheel’s dressing unit, a fourth connected to the regulating wheel and a fifth connected to the slide stack, which moves the regulating wheel into position. As for the pumps, one is connected to the hydraulic system and the other to the coolant system.
The Motors in the Machine
A grinder’s five motors will be inspected. They may be cleaned, tested and reinstalled if they’re in good order and sufficient for the machine shop’s purposes. If not in good order, they’ll be replaced.
Even if in good order, they would be replaced if they’re insufficient for a shop’s purposes. For example, the shop may want to grind parts that require more powerful motors, so a grinder’s 15-hp motors would have to be replaced with 30-hp motors.
Or the shop may want greater precision from its grinder, requiring the installation of new servo motors. Equipped with encoders, these DC motors are used for precise, repeatable positioning and are therefore beneficial when connected to the grinding wheel’s dressing unit or to the grinding wheel itself. Precise, repeatable positioning aids the grinder when it’s dressing a complex profile into a grinding wheel and when it’s moving to engage a workpiece.
A servo motor can also be useful when connected to the regulating wheel because it ensures the wheel will move smoothly.
The Spindles
The grinding wheel’s spindle will be disassembled and inspected. The spindle may need to be hand scraped to restore smooth rotation or be replaced if it’s too worn. Also, the spindle bearings may need to be adjusted or replaced.
The spindle, however, may need little work if it uses hydrodynamic wedge bearings. If manufactured and assembled well, the spindle and bearings avoid the metal-to-metal contact that results in wear. “When the spindle turns, it actually floats on a film of oil and never contacts the bearing shoe, so there really is no wear if it’s correctly adjusted and correctly scraped,” Juodvalkis said.
Work on the spindle would include grinding and scraping it. Also, Juodvalkis recommended the spindle be coated for greater wear resistance. The coating can be ceramic or carbide. “Carbide seems to last longer,” Juodvalkis said.
After the coated spindle is ground, the bearing shoes will also be scraped to fit the spindle for height and for contact points across the spindle.
The grinding wheel’s dressing unit will be removed and cleaned as well, with its gibs being ground, hand scraped and reinstalled before the unit is returned to the grinder.
Refurbishing the regulating wheel’s spindle is similar to refurbishing the grinding wheel’s spindle. If the spindle can be reused, it will be rescraped, reground and possibly recoated. The spindle’s bearing shoes will be checked and rescraped or replaced.
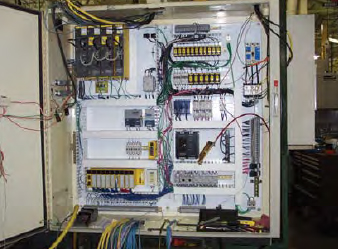
The regulating wheel also has a dressing unit. If it’s a manual dressing unit, the shop may want to leave it that way during a retrofit rather than replace it with a CNC unit. “Generally, you stay with manual because you don’t dress the reg wheel near as much as you do the grinding wheel,” said Steve Combs, president of Cincinnati Service Rebuilders Inc., Cincinnati., a rebuilder of centerless grinders.
The Slide Stack, The Ballscrew
A grinder’s regulating wheel is moved forward and backward by the machine’s slide stack and its ballscrew drive. The stack will be removed, disassembled and inspected. Its ways will be inspected and cleaned.
As with the grinder’s other moving assemblies, ways accumulate material over time from the machine’s grinding wheels and workpieces. “Movement is restricted and then you have problems with the accuracies on the machine,” said Sachin Shah, vice president of RSS Grinders & Automation Inc., a Lombard, Ill.-based rebuilder of centerless grinders. After being cleaned, the ways are ground and hand scraped, as needed.
The stack is lubricated with way oil supplied at high pressure. After the stack is reground and rescraped, its still mounted lubrication lines are checked. If they’re in good condition, they’ll be cleared of debris so they’re clean and open. If damaged, they’ll be replaced. The stack will then be reassembled and reinstalled.
The stack’s ballscrew drive will also be inspected and replaced, as needed. A shop may want the ballscrew drive replaced with a new one even if it doesn’t want to extend the machine’s capabilities. The new drive would be an improvement just because of its more advanced technology. “You get better stiffness,” Combs said. “You get better repeatability, less backlash.”
The Hydraulic, Coolant Systems
The hydraulic system supplies oil to the grinding wheel’s spindle, slides, dressing unit and the regulating wheel’s in feed unit.
During refurbishing, the system would be cleaned, its tubes and other fittings cleared of debris and its pump checked for volume and pressure, as well as for strange noise during operation. If the pump checked out, it’d be cleaned and reused; if not, it would be replaced.
The system stores its oil in an internal cavity in the machine base. This cavity should be painted with an oil-resistant paint to prevent oil absorption and rust.
The coolant system’s pump uses an electric motor, so it may need to have its windings checked and cleaned or replaced. The system’s impeller would also be checked. If not in good shape, it would be replaced.
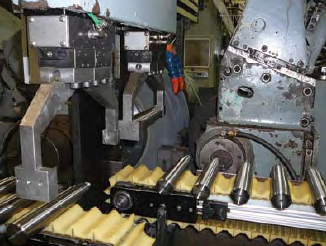
More Than Touching Up
Repainting a grinder does nothing except make it look nice again, unless the repainting is done wrong. Then it’ll hurt the grinder’s performance.
Repainting is more than touching up the old paint or putting a new coat on the old one. The problem is grime on the current coat. “You have a very thin layer of oil on the paint, which is very hard to remove with degreasers,” Shah said. Even if the oil is removed, a new coat of paint can peel off in chips and fall into the grinder’s work area.
Instead, the paint should be sandblasted off, stripping the grinder’s base down to its bare metal. A new coat of primer and a new coat of paint can then be applied, ensuring that the new paint is there to stay.
Testing
After being retrofitted, the grinder will be tested. An initial test will be done by the retrofitter at its location. It may be a standard test. That test allows the retrofitter to compare the grinder’s performance against the standard, which lays down tolerances for the grinder’s operation and the resulting workpieces.
A shop, however, may want its grinder tested via a runoff of a specific part at the retrofitter’s location, its own location or at both. According to Shah, a runoff at the shop’s location may take as little as 30 minutes if the shop only wants a representative of the retrofitter present when the grinder is first turned on and used to ensure it’s working properly.
Or the shop may want its operators trained on a new control, in which case the representative may be there for several days during the shop’s runoff.
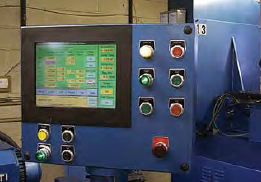
Automation Systems
A retrofit may include adding an automation system to increase the grinder’s productivity.
The type of system for loading and unloading a part or a family of parts depends on the parts themselves and may be a bowl feeder, a pick-and-place system, a conveyor system or a gravity-fed magazine loader.
Combs cautioned that the system shouldn’t reduce access to a grinder’s components, like the regulating wheel’s dresser. “You put a bunch of automation around a grinder and it makes it hard for a guy to even reach it,” he said.
An automation system can be part of a grinder’s electrical cabinet or be controlled separately by a programmable logic controller or a second electrical cabinet.
However, John Blume, operations manager of machine shop V-S Industries Inc., Wheeling, Ill., advised against two separate controls because their communication with each other can breakdown. “The benefit of having one control to control the machine and automation is less communication issues,” he said.
Blume spoke from experience. V-S Industries retrofitted one of its centerless grinders with a new custom-made automation system in 2006. The grinder’s previous system had its own control.
Possible issues include a system loading a part in the grinder when another part is still in the work area. When two workpieces collide during grinding, the result seems inevitable. “They’re scrap,” Blume said.
An automation system equipped with a sensor can also reduce the number of workpiece collisions. Aarstar uses a sensor with a system retrofitted to a centerless grinder that makes more than 18,000 parts per month. The sensor detects a workpiece passing by as it exits the grinder’s work area. If the sensor doesn’t detect a part passing by, the system won’t load another part into the work area. “There are no crashes,” Aarstar’s Tarolla said.
It Takes Time
As described, a retrofit can be comprehensive and may take up to 20 weeks, depending on the availability of components. If a machine shop can’t afford to lose its grinder for an extended period, it could look for a rebuilder that can give it another grinder to use in the meantime.
The time needed for a retrofit, however, ultimately depends on a shop’s intended use of its centerless grinder. “It’s application driven,” Combs said. “You have to look at the process.”