Today’s Machining World Archive: September 2008, Vol.4, Issue 09
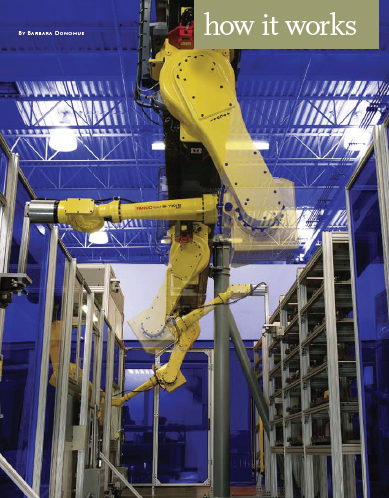
Untouched by Hands
Robot load/unload systems change parts quickly to help maximize spindle time.
With constant pressure from customers to reduce costs, and your own need to maintain profitability – and stay in business in the face of offshore competition – consider finding a way to cut overhead and increase spindle up-time.
Tending a machine automatically with a robot instead of a human operator can save a little time on each cycle. Over weeks and months, even a few seconds per cycle can add up to a significant increase in production. And, since one operator can supervise a number of robot-fed machines, your labor costs can go down, as well. The bottom line? More profit.
Tending a machine automatically with a robot instead of a human operator can save a little time on each cycle. Over weeks and months, even a few seconds per cycle can add up to a significant increase in production. And, since one operator can supervise a number of robot-fed machines, your labor costs can go down, as well. The bottom line? More profit.
Why a robot?
For every piece of a particular part, the loading-cutting-unloading process is the same. CNC machine tools automate the cutting process. Imagine how slow production would be if you still had to run a machine by hand. You can look at the load/unload process in a similar way. If it’s the same every time, why not get a machine to do it?
If you have a dedicated machine running the same or similar parts all the time, you could come up with a cost effective system to automatically feed, load and remove parts without a robot. If you’re running a variety of parts, a robot-based system will give you the adaptability needed to handle different geometries and operations.
A robot arm with a gripper on the end can reproduce many of the same movements as a human arm and hand. Sometimes it can do more– lift a heavy part, for example. The robot can “learn” where to get the raw parts, how to place them in the workholding device, and where to put the completed parts. Then it goes through the same motions every time for every part, with no errors, no breaks, no time off, no leaving for another job. And it can learn to do similar operations for other parts run on the same machine. Or it can be redeployed to another machine in your shop. Or it could tend multiple machines.
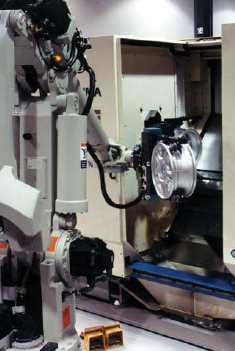
Where should you use a robot?
Installing a system for robotic loading/unloading makes sense in several different situations, said Harper, where you have
• a long run of a single part or a family of similar parts
• parts that can be fed to the machine in bulk – on trays, or from a feeder or conveyor
• heavy parts
• parts that can’t or shouldn’t be touched because they are hot, cold, sharp, radioactive or otherwise dangerous to handle.
Some applications may be more suitable to non-robotic solutions, such as automated feeding systems for small parts, or perhaps a manual or automatic pallet system. You’ll want to look at all your options before deciding on the one that makes the most sense for a particular part on a particular machine in your shop.
What’s in a robot cell?
“A machine tending system consists of the robot, robot tooling, the stand or other structure the robot is fastened to, part feeding and offload systems, and safety guarding,” Harper said. “You can also include mechanical gaging or machine vision inspection equipment, if you want.”
The machine tool will need to have automated chuck or other workholding device.
You’ll need a way to feed the raw parts to the robot. This is often a special tray that holds each part in the correct position for the robot to pick it up. Some machine vision systems enable the robot to “see” parts randomly oriented in a bin or on a conveyor, and correctly pick up each one.
In addition, the robot control will need to “talk to” the machine control so they can coordinate during the load-machine-unload cycle.
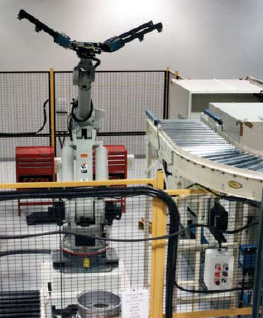
How do the robot and machine communicate?
“The [communications] interface to the machine will typically be the most difficult part of the integration,” said Eric Hershberger, senior engineer, Applied Manufacturing Technologies, Orion, Mich. in an e-mail interview. The degree of difficulty will mostly depend upon how old the machine is, what sort of interface it has, and what sort of control is possible.
“The whole handling system is brought together through the robot programming,” Harper said. Typically, the robot program is completely separate from the machine tool program, and the two systems communicate through ‘signal handshaking.’
Harper described the process: “The machine tool tells the robot ‘I am done machining this piece.’ The robot then tells the machine tool it is swapping parts. When the robot grips the part in the chuck, it tells the machine to release the part and signal [when] the release has happened. This back-and-forth continues until the part swap is complete. Then the machining process begins again.”
Install the robot yourself or hire it done?
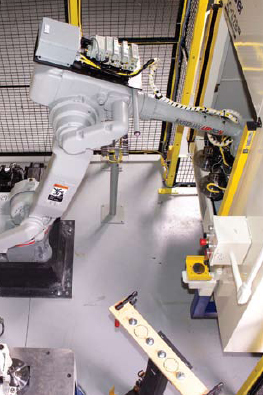
Is it feasible for a shop to design and install its own robot system? “Depending upon the electrical and mechanical skills available, you may want to buy a used robot and integrate it in-house,” Hershberger said. A large engineering consulting company like his could provide assistance as needed.
“A tech-savvy shop could do a robot integration, with some effort invested in training and research of robot cell designs,” said Harper. However, this could take two or three times as long on the calendar as using an experienced systems integrator. “If the shop is honest about the real cost of design and integration hours,” he said, “then the cost savings will typically amount to 10 or 15 percent of the cost of using an integrator.”
“If you decide to go with a professional systems integrator, ask robot companies for recommendations,” Harper said. “If several robots are under consideration, then look at several integrators. Proposals should be broken down to show capital equipment (robot), fabricated parts (guarding, stand, tooling), and engineering costs,” he said.
“If an integrator looks at you and says ‘Yes we can do that, no problem,’” then be hesitant, Hershberger said. A good integrator will do the research up front and make recommendations in the quote about the hardware/software systems. “And be sure to check references,” he said.
“A typical system will probably run $50,000 – $100,000,” Hershberger said, “depending upon options.” To help keep your costs down, consider buying a used robot. “There are hundreds of used quality robots available for purchase,” said Hershberger. “I have bought robots for $5,000 that will run for five years with no problems.” The older the robot the fewer options or spare parts might be available. If the robot is several years old, buy two or three for spare parts, he suggested.
Safety is a major consideration in robot installations. “The entire work envelope must be protected by a safety system,” Harper said. This could be a combination of safety fencing, light curtains, and safety mats. Any point within the robot’s reach must be guarded against human entry, as specified by the Robot Industries Association standard RIA 15.06
What can a robot do?
Two applications featured on the Web site of Motoman, Inc., West Carrollton, Ohio, show how robots can operate in the shop.
In one work cell, two lathes turn aluminum automobile wheels 14 to 17 diameter, and in five different widths, which weigh 40 to 45 pounds. One lathe turns the back edge of the wheel, the other the front edge. A Motoman SK120 robot removes a wheel from the in feed conveyor, loads it into the first lathe. When machining is complete, the robot places the wheel on an out feed conveyor. When changing from one wheel size to another, all the operator has to do manually is change the chucks in the lathes and some locating pins.
In another work cell, a Motoman UP50N robot automatically loads and unloads ten-pound wheel hubs in two machining centers. It also tries the hubs on a gauging fixture and places bad parts in a reject chute. The robot tool holds two raw parts and two finished parts simultaneously.
Is there a robot in your future?
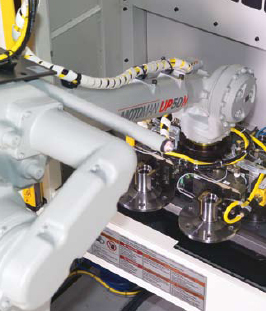
“Robots for loading and unloading bring with them additional benefits besides minimizing the time the spindle must stop at part change,” Harper pointed out.
A properly programmed and equipped robot will handle parts predictably and won’t often drop them.
Robots do not need to take a lunch break, a vacation, or any time off at all, other than a minimal amount of time for maintenance. Do you need to run machines around the clock?
Ask a robot to help
On the negative side, there is the initial cost, $100,000 to $250,000 for a robot work cell, according to Harper. And the robot does require maintenance, which a person would not.
A robot may have a hard time handling parts that vary a great deal in size or are out of tolerance.
Finally, the robot won’t do the quick visual inspection a person can do when unloading parts. “You can make up for this, to some degree, by incorporating a machine vision inspection system into the robot cell, for $15,000 to $50,000.” Harper said.
Is it worth installing a robot? You’ll have to make the calculations yourself. And you may find that a robot load/unload system will pay for itself in a year or two, by providing shorter cycle times, extended hours of machine operation, and a reduction in labor costs.