Dear Shop Doc,
We are trying to run a variety of very small parts on a 20 mm gang tool CNC Swiss and are having trouble with deflection when cross drilling and milling. Is there a way to get the live tools closer to the guide bushing?
Bent in Benton Harbor
Dear Bent,
There is no way to bring the tool closer to the guide bushing face. You can bring the guide bushing face closer to the bar by ordering an extended nose guide bushing.
An ER16 live tool spindle is usually between 14-16 mm away from the face of the guide bushing. You can decrease that distance by using an extended nose guide bushing to take up most of that space. However there are several issues to consider.
The fixed position of the live spindle is set so that the spindle has adequate clearance for the collet nut on the live tool attachment. Simply extending the nose of the bushing out means that the nut will now interfere with the face of the guide bushing, so you must do one of two things:
1) Extend the spindle by chucking on a smaller capacity ER8 or ER11 collet chuck. You can buy an ER8 or ER11 with a 10 mm shank and a mini nut. Mount the drill chuck in the live spindle and chuck the tool in the smaller capacity drill chuck. Stick the small drill chuck out far enough so that the ER16 chuck nut doesn’t hit the bushing face.
2) Order the extended nose to be turned to a smaller diameter. You could for example have the extension made to a 3/8” diameter by 0.300” long. Then keep the ER16 chuck nut above that diameter while cross drilling.
You will also need to shim out all of your turning tools by the same amount of the extension, as well as set your drills back by the same amount. Your machine tool builder might offer blocks that will shim the whole gang slide out by a set distance.
One final solution that might work depending on your situation is to use larger diameter bar stock. A larger bar can provide extra rigidity if you turn up to the live tool feature, machine it, then turn. In order to work, the bar diameter must be at least 1/3 of the distance from the face of the bushing to the center of your live spindle or larger.
Dan Murphy is a regional sales manager for REM Sales LLC., a U.S. Tsugami importer. He can be reached at dmurphy@remsales.com.
Have a technical question of your own? Email us and we’ll find a Shop Doc to answer it. Or, if you know a Shop Doc or are a Shop Doc contact us to contribute. emily@todaysmachiningworld.com, 708-535-2237
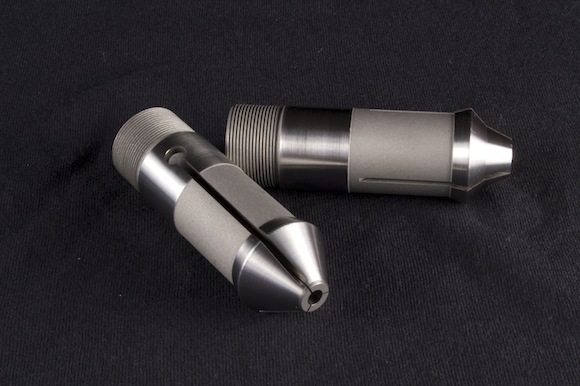
1 Comment
Another solution I have used is to bring the sub-spindle in and use it as a support, this is dependent on where you have allowed to pick up from in the first place but can be very useful when turning simple shafts which require many cross holes.
Best regards
Gerald Balk