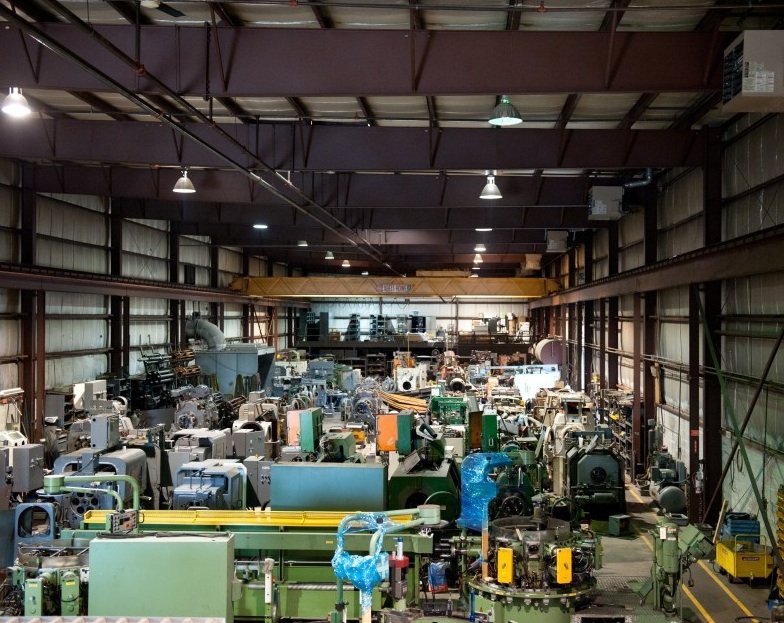
“What goes around, comes around.” It’s a dumb cliché, but it’s what I am seeing in the screw machine business today.
The cyclicality of business is playing out as the auto industry in North America pushes toward the magical 16 million units a year mark. Thank god for the F-150, now the “best selling car or truck in America.” Tradesmen are buying, businesses are buying, even Aunt Millie is buying a vehicle today, and most of them are put together in North America with millions of perfectly turned components also made here.
Add a revival in home building and all those unleaded brass fittings needed and it means a lot of spindles turning, after the up and down gutting of the traditional turned parts world over the last 15 years.
My guess is that one third of the shops that ran multi-spindle automatics have gone away since the wholesale outsourcing trend to China began in the late 1990s.
The decline and the current revival were masked by the countercyclical growth in mining and Chinese infrastructure, which has made up for some of the huge decline in cars and homes over the last decade. Now weakness at Caterpillar and in the hydraulics industry is hurting some of the firms that prospered during the widespread decline. The shale boom in the U.S. has boosted that area, but it cannot make up for the China slowdown, which could last a few years, and the parallel mining weakness.
The recent relocation edict by Beijing to bring 100 million people from the countryside to cities will limit the correction, I think.
I am heartened to see veterans of the turned parts world starting to reinvest. Recently several clients of Graff-Pinkert have told me, “I thought I’d never buy a multi-spindle again, but I’m so busy in that area now, I need to reassess.”
I see this as the beginning of an upgrading cycle in turned parts manufacturing here. Mindsets change slowly, but necessity can force a pivot. I think we are near that pivot point, at least in North America. Many of the younger people who have gravitated to the industry over the last decade have seen mostly declining volumes, which has made multi-spindle turning look obsolete. But today, with well-financed incumbents few and far between, the survivors in a depleted environment should thrive for the next five years.
Question: What equipment would you invest in for your business today?
Lloyd Graff is the owner and chief space filler of both Today’s Machining World and Graff-Pinkert & Co, a reseller of used screw machines, Hydromats, and CNCs.
3 Comments
The first investment any company makes, that is involved with multi-spindle screw machines, should be training! This is where the biggest issue is. Quality set up personnel and operators are very hard to come by. The fact that 30% of these types of shops have gone away does help this issue. However, most screw machine personalities today seem to be in their 50’s or better. (Notice I say “better”) We’re not getting any younger; I wish more younger people would get interested. It is a skilled trade and as Lloyd points out, a reliable future.
Loyd,
You hit the nail right on the head so to speek.
We have sold several larger capacity Acme’s to Companies that were totally CNC, with quantities increasing. They are finding out there is a lot on time & money saved to blank on an Acme & finish on the CNC. One Company is tell us they are saving over $1.59 on each piece they make!! Talk about saving!!! They reported the machine payed for it’s self in 8 months, let’s see any CNC do that? I am not bad mouthing CNC,s as they most surely have there place in “American” manufacturing today,”Thank God”!!!!!!!!
Equipment that is able to run in an unattended automated manufacturing environment. This isn’t for everyone and isn’t right for everything that is being manufactured, it is right for me.