The following story was written by longtime TMW reader Peter Frow, Founder of FAS Machine Tools and Renfield Machine Tools. Peter has also been a guest on the Swarfcast podcast twice, on EP 94 and again on EP 199.
The search for my “Holy Grail” began in the 1990s in my home country of South Africa. Prior to this, I had completed a degree in Mechanical Engineering at Durban University South Africa and worked for the national power producer ESKOM for seven years, eventually attaining the position of Senior Engineer in the Johannesburg head office.
Desiring to move back to my home city, I resigned my job and set about finding work in Durban. In the interim, my father offered me a position in his small factory which was running a few screw machines. This resulted in a career change as I became interested in manufacturing and stayed on for nine years, initially as Production Manager and later CEO. During this time the company expanded greatly, operating both single-spindle and multi-spindle screw machines, as well as a host of second-operation machines. With a staff of 70 we were making OE (original equipment) parts for Toyota, as well as replacement components for Mercedes Benz trucks and replacement valve guides for all makes of cars. Then I left the business for a seven-year spell doing church ministry and various community upliftment projects.
In 1991, I started up my own business. This time, rather than operating the machines that made the widgets, I decided to supply machines and leave the widget-making to others.
So commenced a season in which we would recondition single-spindles and multi-spindles, and turnkey them for customers. Over the next few years, we supplied a wide variety of different makes of machines to customers throughout South Africa.
CNC lathes were of course making strong inroads into the market at this time and were replacing cam-operated machines because of their ease of operation.
The downside of CNC lathes, apart from their high capital cost, was that they often had slower cycle times than cam-operated machines, mainly because they only applied one tool to the workpiece at any one time. The cam machines on the other hand, could readily have several tools working simultaneously but were not user-friendly, requiring job-specific cams to be made and a skilled tool setter to make them work efficiently.
It became apparent that for longer production runs, the market needed a lathe with the following:
- The user-friendliness of a CNC lathe
- The fast cycle times of a cam-operated machine
- An affordable price tag
The last two decades of my life have been spent pursuing this “Holy Grail”.
The FASLathe
A screw machine configuration with servo-operated slides would satisfy the first two criteria, but because such a machine would ideally require six axes and each axis carried a high price tag, this tended to drive the price up so that the third criterion was not satisfied.
We set out to produce an extremely user-friendly cam-operated machine that included a number of innovative features, which enabled changeovers between completely different components in under 30 minutes. This capability even applied to threaded components. The main trick was to use the multi-spindle practice of driving the camshafts off the spindle instead of with their own gear train. Slides were operated by means of a quadrant-setting arrangement for varying feed rates.
The machine was furnished with universal cams having enough throw for the largest job, and unused portions were passed over by means of an accelerator. The machine was synchronous in that once set, the spindle speed could be altered without affecting feed-rates and event timings, even when threading. We called the machine the FASLathe. A number were produced, and some are still in operation to this day.
However, it was clear that the market for cam-operated lathes, even user-friendly ones, was shrinking.
A line by Danny De Vito from the movie Other People’s Money struck me:
“You know, at one time there must’ve been dozens of companies making buggy whips. And I’ll bet the last company around was the one that made the best goddamn buggy whip you ever saw.”
FAS Synchroturn
Clearly, what was needed was a CNC version of a single-spindle screw machine.
We proceeded to license a company in India to manufacture the FASLathe, as the country had lower manufacturing costs and still had a ready market for cam-operated lathes.
We used the proceeds of this deal to help finance the design and development of the Synchroturn 6-axis CNC Lathe.
This machine uses some of the design philosophy of the FASLathe in that all slide elements, including the turret, were cantilevered off the headstock, eliminating an expensive base casting.
The machine has the following features:
- 3 cross slides one of which moves in 2 axes
- An 8-station Turret which moves in 2 axes
- Electromechanical chucking & Indexing
The ability to have four tools working simultaneously on the workpiece together with rapid chucking and indexing times produces cycle times significantly quicker than conventional CNC Lathes. The machine is available in spindle sizes of 60 mm and 42 mm.
FAS Synchronette
However, it was apparent that the main need was for spindle sizes under 42 mm with the ability to do back-working, milling and other operations.
To meet this need, we built the Synchronette 7-Axis CNC Lathe—available in 26 mm and 36 mm spindle sizes.
It has the same slide configuration as the Synchroturn but can also be equipped with live turret tooling, a rotating pickup head and a rear-mounted gang-tool arrangement allowing back-working, cross-drilling and other second operations.
https://faslathe.com/wp-content/uploads/2021/01/FAS-Synchronette-S-3626.mp4
These features allow the machine to produce complex components without the need for further operations. The machine has a compact footprint and can be equipped with a variety of different bar-feeders.
The Bell Demo for the Synchronette
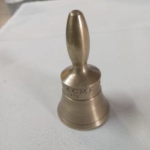
As we considered how to promote the Synchronette, I recalled a machine tool exhibition in 1970, in which a bell was produced on an Acme-Gridley multi-spindle. The clapper was made on a separate machine and magazine-fed into the multi-spindle where it was swaged to make the clapper captive.
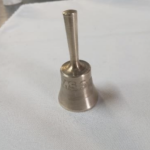
It occurred to us that if we could figure out a way to make the clapper out of the material inside the skirt then this would be a pretty neat way to demonstrate the capabilities of the Synchronette. With some head-scratching we managed to figure out a way to do this. The result was this bell:
This is how it is done: https://youtu.be/VTxP7S1XXnc
Here are the two bells together:
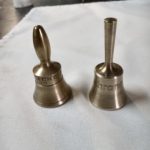
The Ex Works price of the entry level Synchronette is under $70,000 despite having a healthy margin.
As this is less than half the cost of equivalent machines, the “affordable price tag” requirement may be reckoned as accomplished.
So, with the hard yards of design and development behind us and the object of our search achieved, we now wish to pass on our screw machine “Holy Grail” to those who will exploit its potential. We are offering a controlling interest in FAS Machine Tools to interested parties.
The company’s assets include valuable Intellectual Property in the form of complete manufacturing drawings for the FAS range of products as well as foundry patterns, jigs and fixtures.
There are a number of machines in the field and the company is poised to expand its order book.
Peter Frow can be contacted at faslathe@iafrica.com, +27844012674
Questions:
What is your Holy Grail machine?
What inventions have you come up with?
1 Comment
My holy grail machine is the old legacy Hydromats. Thank you Bud Pohlman, Bruno Schmitter, Jim Otten & others.
I’ve paid for 5 patents and started 46 companies / most of them stillborn.
In my view marketing seems to be the holy grail. How do you profitably sell what ever it is you are producing or inventing.
My invention of the week is gun suppressors. Very crowded market. 100’s of patents. Lots of marketing fluff with little proof one suppressor is any better than the other. We can produce your components or private label complete assemblies. Hydromats and CNC multi’s are more cost effective than slow CNC single spindles. Send RFQ’s to john@griner.com
Thanks Lloyd/ Noah / Rex for the billboard..