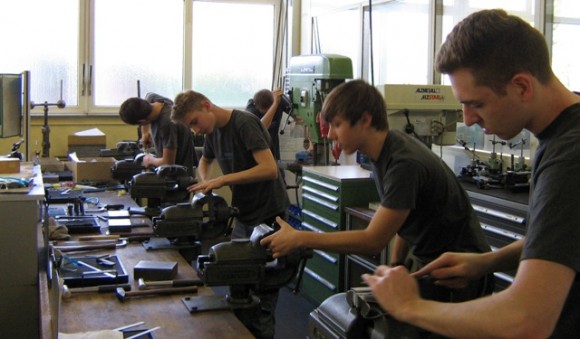
“The Davenport screw machine won World War II,” Massimo Bonaldo said to me, as we ate kebabs in a rural village 40 minutes from the center of Hannover, where I was to attend the EMO Machine Tool Show the following day. Massimo is the technical manager of Tajmac-MTM S.p.A., the Italian headquarters of ZPS, one of Europe’s top machine tool builders.
I had trekked throughout Germany the previous two weeks, visiting elite manufacturers and machine tools dealers. I had walked through state-of-the-art shops, packed with the latest INDEX MS machines, Hydromats and CNC machining centers. And now I found myself hanging out at midnight with three Italian ZPS technicians in middle-of-nowhere Germany, with one of the company’s top engineers giving me a history lesson on the good old noisy American Davenport. The reason the Davenport won World War II for the Allies, Massimo explained, was that the Germans were using European single-spindle machines to bang out ammunition, while the Americans spit out bullets like mad with 5-spindle Davenports. Times have changed since the days of American multi-spindle domination. Today Germany is the place to be to see tons of manufacturers full of the best multi-spindle screw machines on the market. That’s why Graff-Pinkert sent me there to find machines.
The first shop I visited on my trip was Brehm Präzisionstechnik GmbH & Co. KG, about 100 km southeast of Stuttgart. The shop was immaculate and packed with some of the best modern machine tools on the market. It was one of those places us machinery dealers like to say “is so nice, you can lick the floor.” I had barely met Thomas Brehm, the company’s owner, at a conference in Europe a year before. I emailed him prior to my trip to say I was coming to Germany and wanted to visit his shop, even if he didn’t have anything he wanted to buy or sell, and he graciously extended me the invitation. When I arrived, he took me to lunch at a local restaurant, where I ate some excellent veal with mushrooms. Brehm spent several hours showing me around the shop, which featured 20 beautiful INDEX MS 32 machines. He also gave me the inside scoop on running a manufacturing business in Germany.
Because of labor laws established long ago in Germany (similar to those in much of Europe), it is generally illegal to fire employees. Almost all of Brehm’s employees stay at the company 30 to 40 years, which is why he characterized employment at the company as a “marriage.” Brehm said that more than 50 16-year-olds compete for five apprenticeship spots each year at the company. To me, the idea of a 16-year-old signing up to a job for life is difficult to fathom. What if the kid no longer wants a factory job in five years? How can an employer know what type of person a 16-year-old adolescent will be five years, let alone 30? But who am I to judge, as German companies like Brehm appear to have lots of content, quality workers, while American companies repeatedly lament that they can’t find good talent.
Later in the trip, I visited some shops near the western border of Germany, not far from Cologne. One dealer had 10 old Gildemeisters in the basement of his home that doubles as his office. The machines belonged to his family’s production business, which existed prior to him becoming a dealer. I visited another job shop in that same region, high up in the mountains. I crawled up one-lane roads in the rain to get there. I asked the company’s owner, a fourth generation in the family business, why so many shops in Germany are located in such remote, crazy spots? He told me that his company was 122 years old, so in the old days the factory needed water power from the mountain streams.
I hadn’t heard of the shop in the mountains before that day. My visit to the shop had been arranged on the spur of the moment that morning when I got a tip that they may have had some equipment for sale. When the owner greeted me at the door, I was amazed as he handed me a crisp business card belonging to Rex Magagnotti, another salesman at Graff-Pinkert, who had traveled to the shop 16 years before. I suppose that a 16-year time lapse between our two visits was just a blip in the company’s 122-year lifespan.
Question: What career path did you envision for yourself when you were 16?
Noah Graff is a machine tools dealer at Graff-Pinkert & Co. and an editor at Today’s Machining World.
12 Comments
At 16 I thought I would pitch for the Chicago Cubs or be a columnist for The Chicago Daily News or Tribune, like the great Mike Royko.
I really enjoyed the article on your Germany trip. I’d love to do that someday. But what I really liked was seeing the picture of the apprentices learning how to use a file! This tells me that they are obviously starting with the basics which I believe is critical in becoming a good machinist. I could talk more on this issue but won’t take the time here to do that.
Thanks again for the article.
Dick Chamberlain
JD Norman (previously Len Industries)
I started my apprenticeship in England when I was 15yrs and 3 days! I’m still working on machines almost 52 yrs later!
At 16 years old I thought I would eventually head to Hollywood a become a stuntman.
At 16 I thought I would be designing Corvettes for GM. Then in College I learned I didn’t like designing as much as I liked solving manufacturing problems which changed my path a little. Then it looked like I was still on track for working in automotive but then September 11th happened 3 months before I graduated and I got the only job I could find in the same town as my fiance who was still in school. 12 years later I’m still here working at a captive job shop for a Gluing and Packaging equipment manufacturer. No Automotive for me. I still kind of wish I was in automotive because I don’t get into as much automation technology as I would like but a nice stable job is something to be happy with in this yo-yo economy.
My original intent was to be a draftsman. I got a chance to get into the GE Apprentice School in Fort Wayne at the start of my senior year of high school. I got little drafting assignments during my senior year of high school. As soon as I was18 I was placed out in the apprentice shop to get started on the required hands on tool shop training. Six weeks later I changed direction and elected to switch over to the Machinist Toolmaker Program. And over 45 years later, I’m still there.
At 16 I was starting into vocational school machine trades. 39 years after graduation I’m still in the trade.
At 16 I was 100% convinced I would be the principal french horn player of the Minneapolis Symphony.
Mom was a nurse and was pushing pretty hard to steer me into the medical profession at 16. Dad was a bit more practical and advised me to take some time to think about it after I graduated high school. I joined the Navy, signed on for Hospital Corps school and after completing advanced O/R Tech training found myself in a Marine rifle battalion in Southeast Asia in the early 60’s. That convinced me I did not want to do that for a living when I got out of the ‘service’. Caterpillar hired me into their 4-yr Manufacturing apprentice program a month after I mustered out at Camp Pendleton and I’m getting ready to retire now after an almost 50 year career as a Mfg. Engineer. This was a case of the job finding me, instead of vise-versa. I love taking the Design Engineer’s print and figuring out how we’re going to meet all the specifications with a competitive manufacturing process, even to turning down a couple of promotions just to stay in the ‘hands-on’ end of the business.
You and your father are truly gifted wordsmiths Noah…we manufacturing guys just don’t have the dna to communicate all that is fascinating and enjoyable about our industry…both of you adds color to a very gray world we live in and love.
I also appreciate another generation contributing to what I consider the backbone (I.e., machining) of the greatest county in earth.
I just about jumped out of my chair when reading about your late night discussion of the Davenports importance in the War.
It really resonates as I have invested the last year into starting a company focused on reshoring machined components from the third world using multiple spindle specials, Rotary Transfer & Trunnion machines integrated with robotics tooled up in small austere plants managed by men who will be given equity in their plant and will make all decisions themselves (after much mentoring). The core attribute to this business model is “simultaneous machining” as compared to single spindle linear machining (I.e. All Machining and and most Turning Centers).
When I was 16 I was working hard at becoming a professional motocross racer until a blown knee and a string of tough experimental reconstructions brought the dream to an end; however, I have always been able to find a similar exhilaration and gratification starting and building successful machining plants. Keep up the good work!
Nice article! Being German myself and looking back on 16 years of employment so far I can tell you that “…in much of Europe…generally illegal to fire employees” is a slightly over-enthusiastic way of describing what are simply good labour-protection laws. Of course people can and do get fired every day in Germany and Europe as a whole, it’s just that the employer needs good justifiable reason to do so.
The days were German 16-year olds “get married to a job for life” are also long-gone. In Germany as in most of Europe a typical modern career path will require experience working abroad and much like anywhere else it is far more common to change employment, especially at the beginning of a career, as one’s career develops, than it is to stay with one company for 30+ years.
By the way in case you don’t know the world’s leading online trade show for industrial manufacturers yet, you will be surpised at the information available on CNC machines: http://www.directindustry.com/tab/cnc.html
My apprenticeship experience was a turning point in my life. It was the best move I ever made. I also have a degree in education, but I am most proud of the journeyman certificates from the Department of Labor, Machinist Union and Washburne Trade School. Not many people can say that they are a journeyman tool and die maker. That said, the general public does not have a clear impression of what we do or can do. So many people think that the machine run by a computer or they can 3-D print a part for little or no cost. There is much more to the business and it is our job as skilled craftsmen to educate the masses. I don’t think that manufacturing will return to the old days, but sooner or later things will change, hopefully for the better.