Today’s Machining World Archive: July 2008, Vol. 4, Issue 07
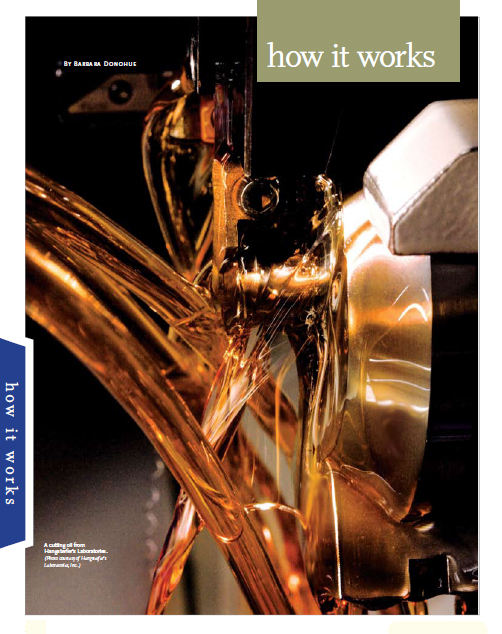
Unless you’re doing dry machining, you’ll use some kind of cutting oil or fluid in your machines. Cutting fluids and oils provide lubrication and cooling. They also help remove chips from the cutting area. Selecting from the hundreds of available cutting fluids can be a real challenge. Experts in the business offer some guidelines on selecting and maintaining this important part of the machining process. Usually, you’ll choose either a straight oil or a water-miscible (dilutable) fluid.
Straight oils
These are “mineral oils,” petroleum products made fromcrude oil. Straight oils offer the maximum amount of lubrication, and the least cooling capacity. Blended with additives to improve performance, these oils are often used in screw machines and in heavy cutting operations like broaching and gun drilling.
Vegetable oils can be used instead of, or in addition to, mineral oils in many applications. They tend to have better lubricating qualities, and higher flash point, which is the temperature at which their vapor will ignite. In one cutting oil product line, for example, the flash points range from 200F to over 460F, with the vegetable oils on the higher end.
Water-miscible fluids
In addition to straight oils, three kinds of water-miscible cutting fluids are widely used. They give good tool life and help to produce a good surface finish, said Randy Templin, vice president, Blaser Swisslube, Goshen, N.Y., a manufacturer of cutting oils and fluids. When properly mixed, the fluid is mostly water, with a few percent of the fluid concentrate, which is made up of oil and/or synthetics, plus additives.
- Soluble oil: This is oil dispersed in water, making a milky-looking mixture. It offers the greatest amount of lubrication among the water-miscible fluids. Emulsifiers and surfactants let the oil mix with the water and remain stable despite contamination from tramp oil, machining fines, and other materials that find their way into machine sumps, Templin said.
- Synthetics: These don’t contain oil. They are made up of various chemical compounds such as phosphate esters. Synthetics fully dissolve into water. They are often transparent and may look like water or have a colorant added. They tend to be the most stable of the water-miscible fluids, and are often used for applications such as fine grinding, where a fluid is needed to keep the wheel open and clean, according to Templin.
- Semi-synthetics: These blend oil and synthetics to give a combination of lubrication, stability and cooling performance. The concentrate usually contains 30 percent, or less, of mineral oil, Templin said.
Finding the right oil or fluid for your application
“We’re trying to change the [industry’s] view,” said Templin, “so people think of coolant or cutting oil as part of the cutting tool package, [something that] can improve the performance of any tool.”
There are so many products available and so many different applications that you will probably depend on your coolant supplier to help you select which fluid to use. Even if you are happy with your current cutting fluid, there may be room for improvement. In many shops, “If tool life is reasonable, they don’t know their coolant [isn’t] optimized,” said Joe Gentile, product manager at Hangsterfer’s Laboratories, Inc., Mantua, N.J.
“The first thing I ask is: what is the primary material that the shop runs? Then, what is the secondary material,” said Gentile. Most shops specialize and don’t realize it, he said. Which machining and other processes is the shop running? Heavy cutting? Grinding?
Gentile also determines what the shop’s tolerance is for residues on parts and machines. “Some shops want the machine to look like you could eat off it; some just want the tool lubricated,” he said. Also, medical and other critical parts shouldn’t accumulate any residue.
Your supplier will likely ask what kind of problems you’re having. Maybe you are not be getting the kind of tool life you expect. Maybe “the current product is going sour, having biostability problems, smoking, misting, leaving residues, or [making operators’] skin break out,” said Mark Goedtel, product manager at Valenite LLC, Madison Heights, Mich., a manufacturer of cutting fluids and tools.
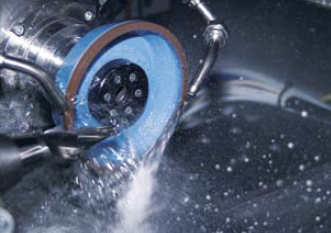
From this and other information, your supplier will select a fluid that meets the needs of your primary application, works effectively with secondary materials and operations, and is compatible with any post-machining processes.
Give it a try
Testing a new coolant is a big commitment. “An insert is easy to put in a machine and test,” said Gentile. “Coolant is a different story.” You have to empty and clean the machine, he said, and you’ll need to be running the same part with both fluids, so you can compare performance.
With a fluid better matched to your process, you stand to gain improved tool life, better surface finish, and reduced cycle times. You may even be able to reduce your per-tool cost, as well. “We’ve helped customers using a $100 drill go to a $20 drill with the same tool life,” Templin said. You can’t always go from carbide tools to high speed steel, he said, but the right cutting fluid in the
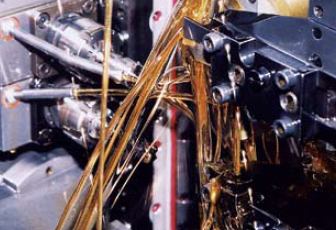
right situation can sometimes make this possible.
Goedtel told about a company that was bar peeling, a very aggressive machining process. However, the shop was using a full-synthetic water-miscible coolant, normally intended for lighter duty. This produced lots of steam and mist. Coolant usage was high – about one drum per day – and tool life was poor. To get acceptable performance with the full-synthetic, the shop was running it at 25 percent concentration instead of the usual 5 percent. Valenite provided a semi-synthetic that added lubrication, improved tool life and reduced misting, steam, and fluid loss.
When you change to a new cutting fluid, it needs be compatible with all of your machining processes, but don’t forget what happens after machining. Verify that your cleaning process works with it, and be sure to alert your plating or paint shop. The new fluid may leave different residues for them to deal with. For medical and other critical applications, alert your customers well in advance of the change, as they may need to obtain regulatory approval.
Mostly water
Since water-miscible fluids are mixed with about 95 percent water, you should have your tap water tested before selecting a new water-miscible fluid. The minerals in hard water can cause a problem with residues, and chemically softened water may tend to cause excessive foaming. Your cutting fluid supplier can advise you, and has different versions of product to alleviate some water-quality problems.
Keeping your cutting fluids on the job
As the price of crude oil goes up, and waste disposal rates rise, the lifetime cost of your cutting fluids goes up, as well. In the past, a shop may have routinely changed out the coolant every year or even every six months; now they’ll try to keep the fluid going as long as possible. This requires careful monitoring and maintenance, but can pay off in the long run.
“The cost of coolant [concentrate might be] $20 per gallon,” said Steven Friedman, president of Sanborn Technologies, Walpole, Mass., a manufacturer of separation equipment for industrial applications. Then you mix water and concentrate in a ratio of 20 to 1. Now, from one gallon of concentrate, you have 20 gallons of waste to dispose of. It may cost you 50 cents per gallon, he said, to have it hauled.
“Cutting fluids are much better today than in the past,” said Friedman. “They last longer and do more of what customers want.” But to keep them going, you need to do some housekeeping – remove solids and tramp oil, and monitor the concentration and pH of the fluid.
To get a feel for the condition of your cutting fluid, filling a small bottle with clean fluid from a machine sump, suggested Bill Cruey, problem solver with Knoll America, Madison Heights, Mich., a supplier of liquid coolant equipment. Let it stand a few days. The solids will settle to the bottom, and the tramp oil may float to the top. Cruey also suggests tying a magnet on a string and leaving it in the sump for a few hours. If you’ve been cutting magnetic materials, the magnet will come out with a fur of tiny metal fragments.
Be particular
Many different kinds of filtration equipment are available for solids removal. Nowadays, it is common to filter out particles down to 30 microns (about 0.001”). However, as shops keep fluid in service longer, smaller particles, “micro fines” accumulate more. They can cause wear on the tool, and clog through-the-tool coolant passages. If you’re running a high-pressure coolant pump, it’s a good idea to filter down to 5 or 10 microns.
Tramp oil
Hydraulic oil and lubricant from the machine ways can end up in the cutting fluid. This can interfere with the fluid’s performance. “Even a couple of percent of tramp oil can make a big difference,” Templin said.
With synthetic water-miscible fluids, often the tramp oil will float to the top when the machine is idle over the weekend, and you can vacuum it up on Monday. A coalescing unit can also remove the tramp oil.
In soluble oil or semi-synthetic coolants, the tramp oil can be more difficult to separate, Friedman said, so you may need something like a centrifuge to do the job. His and other companies can evaluate a sample of your cutting fluid and determine how best to deal with tramp oil and other filtration issues.
Concentration
Water evaporates continually, so you’ll need to monitor the concentration of water-miscible fluids and keep them at their optimum concentration. You can check this yourself with a device called a refractometer, available from your supplier. Some suppliers will analyze samples for you. Goedtel says Valenite performs monthly analysis for customers as part of product support.
pH
Another part of maintenance is monitoring the pH. This is an indicator of the cutting fluid’s “health.” Fluid tends to go acidic when there is a problem. If the pH is out of range, you can run the sump low and add fluid to it, or if the coolant is old, you should probably change it out. In a central cutting fluid system, you might add a pH adjuster.
Microorganisms
Water-miscible cutting fluids offer a friendly environment to bacteria and fungi: warmth, moisture, nutrients. Overgrowth of the wrong microbes can make the fluid smell very bad.
Fluid manufacturers have a number of ways to prevent this. They can formulate the fluid so it provides very little nutrient material, reducing growth of the germs. Or they can add a biocide that kills any microbes present. This could eventually result in the microbes becoming resistant to the biocide.
Another approach is to provide conditions in the cutting fluid that allow friendly, harmless bacteria to thrive, which keep the “bad bugs” from growing out of control, Templin explained. His company’s Blasocut product line uses this method.
Filter, clean and recycle
You can use a movable filtration unit, which wheels up to the machine, such as the portable filtration cart available from Knoll America. This unit incorporates a bag filter and/or a magnetic filter, and can remove particulates down to 5 microns (about 0.00002”). It sells for about $7,500, according to Cruey. This type of unit draws fluid from the machine sump, filters it how it works
and returns it to the sump. Portable tramp oil removers are also available.
To clean the fluid even more thoroughly, you may want to invest in a self-contained recycling unit. These remove tramp oil and thoroughly filter the fluid. Such a unit might cost $100,000, Friedman said. “The important thing is: the fluid is expensive to use and expensive to dispose of, so buying a quality recycling system [can] save money in the long run.”
You need to remove the fluid from the machine, said Friedman, take it somewhere and clean it. At the same time, you can clean the sump. “The right way to do this is on a scheduled basis,” Friedman said, ideally once a month. Vacuum out the coolant from the machine tool sump and take it to your recycling system. Then you can immediately refill the sump with fresh or recycled fluid and start making parts again.
“The metalworking fluid in your facility is the only thing that touches every tool, every part, every person,” said Templin. You handle it. You breathe the mist. It affects every cut and every person who walks in the door, including your customers.
Experts consider the fluid to be as much a part of the machining process as the workpiece and the cutting tool. And the right fluid, properly maintained, can help keep your machines producing high quality parts, economically, with optimum cycle times.
1 Comment
Allied Electrical is the company manufactures and indirectly exports CP and CPM Coolant Pump, which are an immersion type Centrifugal Pumps. The primary objective of these pumps is dissipation of heat from the work piece and the cutting edges.