Today’s Machining World Archive: February 2007 Vol. 3, Issue 02
Everybody in the business has used flooded coolant practically forever and knows that it works. They are probably also aware that it has its drawbacks, including:
• The cost of buying, maintaining and disposing of cutting fluid, which is estimated to account for 7 to 17 percent of the cost of machining parts.
• The need to clean parts after machining and to remove as much fluid as possible from chips before recycling
• Health problems from handling or working around conventional coolants include skin irritation or allergic reactions, asthma, bronchitis and other respiratory difficulties. It’s possible that long-term exposure to some coolant additives could lead to cancer.
Competitive cost pressures and increasingly stringent environmental and occupational health standards are inspiring some shops to seek ways to minimize or eliminate their use of cutting fluids. They are finding that dry machining, “minimum quantity lubrication” (MQL) and other techniques offer benefits far beyond simply reducing their cutting fluid costs.
Advanced cutting tool materials, coatings and designs, along with a variety of strategies for lubrication, cooling and chip removal, make it possible to achieve the same or better results with dry or MQL machining: shorter cycle times, better surface finish, longer tool life, and higher recycling value for clean chips.
Dry machining then and now
Some materials have always been machined dry – magnesium, for example. It reacts with water, so common coolants are incompatible with it. PGM-New England, a Manchester, NH, contract manufacturing and assembly company, machines many materials with flood coolant, but it dry machines magnesium for small-aircraft oil pans and other parts. “We’ve had very good success with [magnesium]. It machines very nicely,” said PGM general manager Nick Baldassara.
Dry cutting has also long been used with materials, such as cast iron where “what you create is a dust, not a chip,” said Jim Van Buskirk, applications manager at Methods Machine Tools Inc., Sudbury, MA. “You add coolant and it makes a sludge. [Graphite,] glass-filled materials, phenolics. . . you definitely want to cut dry.”
Graphite, OK. But dry-machining hardened steel? Yes, with the right tool, said Ron Field, vice president for applications at Cole Tooling Systems, Warren, MI. “Greater than 42 Rockwell, you can run it dry. Mold steels you can run dry.” Softer, gummier materials like stainless steel in the soft state won’t work dry, he said.
“After you figure out what kind of material you’re cutting, then it comes down to the cutting tool geometry and coating,” Field said. “[For example, for dry machining of] stainless steel at 50 Rockwell, what we would use is a fl at-top insert, with no chipbreaker, and an aluminum titanium nitride coating.” That type of coating works hot, he said, “which helps melt the material before the cutter, so it slides up the cutting flute. If you put on coolant, that doesn’t happen.”
With the right combination of work material and tool, Field said, you can “turn the coolant off, crank up the rpm, crank up the feed rate, reduce the depth of cut, and run like crazy.” Strange to say, some materials can be cut faster dry than with coolant. Companies and universities are conducting research to understand dry machining, including the behavior of materials at the tool/work interface, performance of the coatings, and the heat generated and how it affects surface finish and tool life.
Tests show that under the right conditions with the right tool, the same part can often be machined dry in a fraction of the time it takes wet. Or tool life may go up by 50 or 100 percent or more. Field visiteda customer where he demonstrated a new tool used dry, which allowed a particular part to be machined much faster, reducing machining time from six hours to 45 minutes.
Why can you cut so much faster dry? Tooling makes the difference. Tool materials, including improved grades of tungsten carbide, and new high-performance coatings contribute to the robustness of the tools. These tools like to be run fast, they tolerate the heat, and they don’t like the thermal shock of going from hot in the cut to cool in the cutting fluid. They prefer to be run dry.
“Cutting tools have come a long way in the last five years,” said Carl Pasciuto, president of Custom Machine Inc., Woburn MA, where they cut many different hard materials without coolant. “The coatings they have now are far beyond what was before. You can’t use conventional tooling to do what these new tools can do.”
One impressive new coating comes from the Fraunhofer Center for Coatings and Laser Applications (in partnership with Michigan State University), East Lansing, MI. “Diamor” is a super-hard, yet low-friction, amorphous carbon coating. MSU mechanical engineering associate professor Patrick Kwon explained that such a coating would be ideal for hard machining of non-ferrous metals. However, he cautioned, a carbon coating like that should not be used with ferrous metals, as the carbon has a strong affinity for iron and would “dissolve” in the chips and work piece material.
So many different tools and coatings are out there that the tricky part of doing the job can be to figure out which combination of tool, coating and machining parameters will work best. The wrong tool under the wrong conditions will fail. Your tooling suppliers know what’s available and what will work best with your job. Based on what material you are cutting and the job’s requirements for surface finish, etc., a supplier can recommend a tool and specify speed, feed and whether you should run it dry or wet.
Just enough lubricant
If you can’t run completely dry, you may still be able to run without resorting to flood coolant. Minimum quantity lubrication (MQL) systems apply a very light spray of an oil/air mixture to the cutting area. This lubricates the tool as it cuts. The heat of machining burns off or evaporates much of the oil, leaving a nearly dry part and nearly dry chips. In MQL, also called “near-dry,” a nozzle or aerosol generator disperses the oil into fine droplets in air, producing an aerosol or mist. This oil/air mixture is delivered to the work either externally or internally through the spindle and via coolant holes in the tool. –Program codes control coolant delivery. The amount of oil varies, depending on the MQL system used and the machining process it is lubricating. A machining center might use 20 to 50 ml (0.67 to 1.67 ounces) per hour.
The oil used for MQL is often vegetable based. “A good vegetable oil does the job,” said Wally Boelkins, president, Unist, Inc., Grand Rapids, MI, a longtime MQL supplier. Unist uses a refined version of rape seed (canola) oil. It has a high fl ash point, around 400 to 450 degrees F, Boelkins said, while a petroleum oil might burn at 250 degrees F. “Reduction of friction is the primary thing,” he said, and the vegetable oil reduces the coefficient of friction about twice as well as a petroleum oil does.
A number of different companies, including Unist, ITW Accu-Lube and Vogel Lubrication, Inc., offer MQL systems to retrofit onto existing machines. Some machine tool manufacturers, such as Horkos Corp. and Ex-Cell-O (MAG Powertrain), offer integrated MQL built into their machining centers. “Ex-Cell-O seems to have the most experience and the most machines in the fi eld for MQL,” observed Mike Hafke, national sales manager – automotive/OEM at Guhring Inc., Brookfield, WI, a supplier of tools and toolholders for MQL.
Many of the MQL setups are intended for machining centers. However, options are available specifically for turning. Vogel Lubrication, Inc., Newport News, VA, offers a delivery nozzle that fits on a turning tool holder, which directs the flow of oil mist toward the cutting edge. The Mircona MQL system, primarily sold in Europe (Mircona AB, Gävle, Sweden), but available in the US, provides toolholders with built-in nozzles to deliver the oil/air mixture to the cutting area.
Other systems for applying lubricant are available, such as the Minimum Oil Machining (MOM) option from Haas Automation. MOM squirts a small amount of oil toward the tool at programmed intervals, dispensing as little as one drop at a time. The MOM system is standard equipment on one of the Haas gantry routers and is available as an option on machining centers. It is especially effective for tapping, said Dave Hayes, product manager at Haas in Oxnard, CA. Depending on the settings, the MOM system may apply four or five times more oil than a typical MQL mist system, according to Robert Myers, business unit manager, ITW Accu-Lube, Glenview, IL, a supplier of MQL systems and lubricants.
What can an MQL system do for you? “We do see longer tool life, particularly on deep drilling,” said Hafke. The air/oil mist is compressed passing through the coolant channels in the drill. “As it escapes, it expands and blows the chips out with a very high velocity.” In one test of deep hole drilling in crankshafts, drills with MQL lasted 90 – 100 meters, while those running wet lasted only about 60.
Hafke gave these examples of where MQL is being used in the automotive sector:
• Ford Motor Company, 6-speed transmissions, Livonia and VanDyke plants in
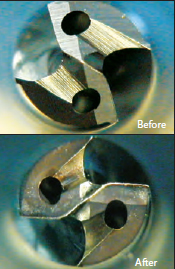
Michigan
• General Motors, crankshafts, Flint (MI) South plant
• DaimlerChrysler, crankshafts, World Engine Plant in Dundee, MI
• Albon Engineering and Manufacturing, connecting rods, Norman, OK
• American Axle & Manufacturing, differential carriers, MI
Cooling, but without traditional coolant
“It’s speculation,” said MSU’s Kwon, “but it has been estimated that 80 percent of heat [in machining] comes from material deformation and the other 20 percent comes from friction.” Lubrication or low-friction coatings can reduce the friction and frictional heating, but the material is still being cut, so the rest of that heat is still going to be generated. Some goes into the chips and some stays in the workpiece. When you drill a lot of holes close together in a workpiece, either dry or with minimal lubricant, so much heat may build up in the part that it expands enough to impair accuracy. If this turns out to be a problem, you can drill a few holes in one area, then drill in a different area while the fi rst section cools down, Hafke recommends. Workpiece expansion due to heat can also pose a problem with fi xturing, he said.
Compressed air may be used directly for cooling. Air is less effective for cooling than liquid coolant, but it also won’t thermally shock hot tools the way a liquid coolant does. Also, air can be used to remove chips. To enhance air cooling, consider using a vortex tube, a device that uses compressed air to generate a low-temperature air stream, down to –30 degrees F, for spot cooling. Available from ITW Vortec, Cincinnati, OH, vortex tubes have no moving parts and essentially separate ordinary compressed air into a hot stream and a cold stream.
More exotic and much colder options are also available. The ICEFLY technology from Air Products and Chemicals, Inc., Allentown, PA, directs a stream of liquid nitrogen toward the cutting edge. Liquid nitrogen, at –320 degrees F, keeps the tool and the work very cool indeed, good for faster machining or increased tool life.
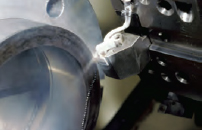
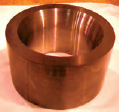
Mike Epting, business manager for ICEFLY, related a unique application: liquid nitrogen cooling made it possible to reshape tungsten carbide punches and dies by turning instead of grinding, greatly reducing the amount of time required. For example, turning one die took only 15 minutes; removing the same amount of material by grinding normally would take several hours. ICEFLY cooling technology is available from Air Products as a retrofi t, and also is being offered as an option on machining centers from Hardinge, Elmira, NY.
Let the chips fall
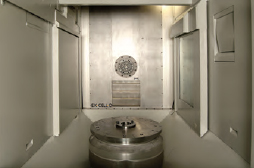
Without pressurized flood coolant, the chips don’t get washed away. With both dry machining and MQL you need to make sure the chips clear from the cutting area. In most machines, you will use an air blast to do the job.
Machines designed specifically for dry machining incorporate chip-handling into their design, providing a free, open path for chips to drop into the collection area. Some machines include a vacuum chip-removal system. Horkos Corp., Canton, MI, takes advantage of gravity for chip removal with its fixture-inverting system. The workpiece is loaded upright on the fixturing table, and then the table is inverted, so the work is machined from below, and the chips simply fall away.
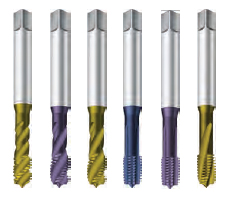
Tapping
“For cutting tools such as end mills, it’s not uncommon to run dry,” said Alan Shepherd, technical director at Emuge Corp., West Boylston, MA. “In taps, people get heartburn over [it]. Usually when you tap holes, you’ve already done a lot of machining and have a lot of money into the product. If you spoil a thread you spoil the product,” he explained. Emuge offers the ÖKO line of taps designed for dry or MQL tapping, as well as tool holders that include a small tube for applying oil mist exactly where it is needed.
When tapping dry or with MQL, it’s important to have a means for removing the hot chips, Shepherd pointed out. Often, an air blast is used to remove them, or for through holes, the fixture can be designed to allow chips to exit from the bottom of the holes.
Cranking up your business
Dry machining and MQL open up many opportunities to save money and reduce machining time. Is dry machining in your future? If you’re machining hard materials, it could be well worth your time to talk with your tooling suppliers and find out what specialized tools might make it possible to crank up your machines. . . and your profits.
2 Comments
Dear sir,
I have read the article. it’s informative and educative.It will be appreciated
if you can mail us this.We are intrested to know more about near dry machining.
Best regards
k.j.sastry
We are starting to use air instead of coolant to keep our cutters cool on the Haas mill. Do we need a certain amount of air pressure placed on the tool? Right now we are using the air line that is in the shop for our air coolant system in the Haas machines VF5 and VF2.