by Barbara Donohue
Today’s Machining World Archives September 2006 Volume 02 Issue 09
Everything wears out eventually, and the spindles in machine tools are no exception. Though many shops could theoretically rebuild or repair their own spindles, many choose to send them out—back to the manufacturer, or to a company that specializes in rebuilding and repairing them.
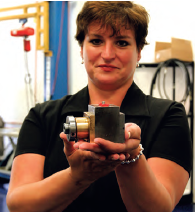
One such company is GTI Spindle Technology, Inc., in Manchester, NH (see sidebar). GTI Spindle repairs and rebuilds a wide variety of spindles from over 300 manufacturers. They rebuild tiny spindles used in machines that wind light bulb fi laments; large spindles used in enormous machining centers; spindles in machines that grind the titanium parts for artifi cial hip joints, cut and polish granite countertops, saw and rout wood for assemble-it-yourself furniture, hone razor blades and even curl the hair on dolls.
First Look
At GTI Spindle, when a spindle arrives at the plant, it is logged into the tracking system. Information about each spindle is available online for customers to track their spindles through the process.
Next, the spindle is evaluated. If it isn’t broken in any obvious way, it is run on a test stand and a vibration profile is taken. A sensor (an accelerometer) is attached to the spindle housing. As the spindle rotates at different speeds, the sensor detects how much it is vibrating. A vibration analyzer takes in the signal from the sensor and prints out a graph showing how severely the spindle vibrates at different frequencies. The vibration signature can help diagnose problems, including out-of-balance conditions and bearings that are failing.
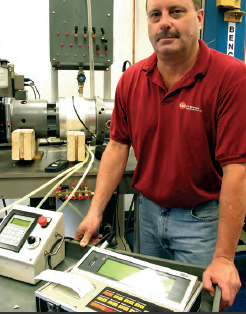
Vibration testing can also help determine there is no problem. Quite often, GTI Spindle receives perfectly good spindles that have been sent out for rebuilding. “One in twenty doesn’t need repair,” according to GTI Spindle president Thomas Hoenig. In these cases, sometimes a little detective work is needed to diagnose the trouble.
Hoenig recalled the case where every fourth part from a customer’s machine was bad. The spindle came in for repair, but there was nothing wrong with it. The customer, helped on-site by a GTI Spindle technician, eventually discovered that the problem was a hydraulic pump mounted to the bed of the machine without benefi t of an isolation pad. When the pump turned on, the vibration disturbed the machining process. In another case, vibration from a compressor in the next room actually interfered with machining.
Looking inside
After vibration analysis, the spindle is carefully measured for runout and other parameters. Then, the technician disassembles it, looking for signs of wear, fracture or other modes of failure.
“Eighty percent [of spindles] fail from contamination in the bearings,” Hoenig says. “Contaminants migrate from the coolant or from air/oil lubrication.”
As the disassembly process continues, the parts are cleaned, examined, measured and sometimes photographed. By the time disassembly is complete, the technician has a pretty good idea what is wrong with the spindle. Each spindle’s components and paperwork are stored in a plastic bin. At this point, the customer receives a diagnosis and a quote for the repair.
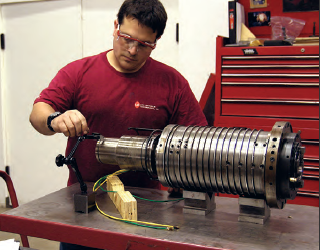
Putting it back together
When GTI Spindle gets the go-ahead from the customer, the repair process commences. Parts are repaired or replaced, as appropriate. Parts damaged in a crash might be resurfaced, welded back together or replaced with new parts machined in GTI Spindle’s machine shop, says Hoenig. Bearings are replaced. Tapers and other surfaces might be reground or could be resurfaced through a process called grind-plate-grind, in which they are ground, sent out for replating and then ground to resize.
A well-balanced spindle
Near-perfect balance is critical in high-speed rotating parts such as spindles, to keep them from vibrating and affecting the accuracy of the machine in which they are installed. At GTI Spindle, individual rotating components are first balanced, then after the spindle is reassembled, the entire spindle assembly is balanced.
The balancing operation is similar to dynamically balancing an automobile wheel with a tire mounted on it. The part is rotated on a balancing machine that indicates where the imbalance is. On a car wheel, weights are added to offset heavy spots.
On most spindles, material is removed opposite lighter spots that could be due to voids in a casting or other causes. An occasional spindle will allow for adding material, such as the large Makino spindle (see below), to which you might add weight by installing setscrews into threaded holes in the shaft, provided for this purpose. Large spindles that are too big to fi t on a balancing machine can be balanced using a vibration sensor and a strobe lamp.
After the spindles are rebuilt, GTI Spindle operates them for at least eight hours to run in the bearings and make sure everything is working properly. Specially designed test stands hold the spindles, power or drive them, provide lubrication, compressed air for air bearings; whatever the spindle needs to run properly.
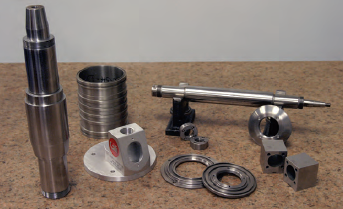
Special stand
Some spindles are especially demanding in what they need to run properly. Makino spindles, such as the one shown above, which is from a vertical machining center, contain passages through the shaft and bearings for oil that lubricates and also cools. This type of spindle cannot be run at speed “on the bench” without its oil supply.
GTI Spindle spent a year and a half and footed the considerable expense to develop a special Makino spindle run-in stand that includes pumps, coolers, vacuum oil recovery and other features. Now, at GTI Spindle, these units can be properly exercised and tested before being shipped back to their owners.
Sending them home
Finally, after the reassembled spindles have been run in, measured, tested and found good, they are painted, if appropriate, and packed in wooden crates for shipping, cushioned by conforming foam. Along with the spindle, GTI Spindle sends the customer the spindle’s records, failure analysis report, if any, and all parts that were replaced. Spindle maintenance, repair and rebuilding can represent a large expense for even a moderately-sized plant. “Customers who spend $50,000 to $ 1 million a year can save 30, 40 or 50 percent, of new replacement cost” says Hoenig. Signifi cant savings can come from maximizing spindle life through proper maintenance and correcting the problems that cause failures. Preventive maintenance, including scheduled rebuilds, can also keep unexpected downtime to a minimum, keeping machine hours and revenue up.
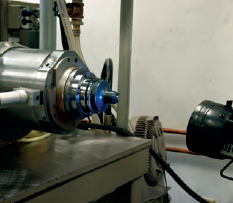
Even though you can depend on spindles to fail eventually, there are ways to plan for failure and minimize its effect on your business.
“We’re the new kids on the block,” says Lisa Bailey-Beavers, national sales manager for GTI Spindle Technology, Inc., a spindle repair and rebuilding company in Manchester, NH. GTI Spindle opened in 1997 with a handful of employees. It now employs more than 50 people in four locations, and since 2002, has doubled revenue and then doubled it again, according to company president Thomas Hoenig. You might not think of spindle rebuilding as a likely business for a successful startup these days. But GTI’s founders saw a need that was going unfulfi lled. And they fi lled it.
“Everybody offered to repair spindles, but nobody offered to partner with the customer to fi gure out why they were breaking in the fi rst place,” says Bailey-Beavers. GTI Spindle includes failure analysis as part of the rebuild process and even tells the customer the diagnosis—right away if it’s a problem like lack of lubrication that could cause the replacement spindle to fail. Then, GTI Spindle works with the customer to solve the problem and prevent future failures. And the customers really appreciate this level of technical support. It saves downtime, and that saves them money.
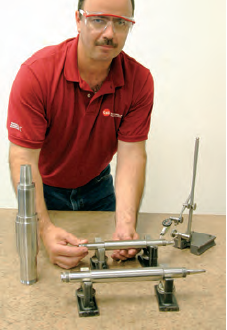
In addition to repairing spindles, GTI Spindle also works with customers to re-engineer their spindles. For example, GTI has designed custom labyrinth rings to prevent contamination, and the company often recommends using ball bearings with lightweight, rigid, long-lived ceramic balls instead of steel. Hoenig says about 70 % of customers have made the switch.
A different spin
Besides sharing information and engineering aid, the company goes even further. “We’re training our competitors,” says Hoenig with a bit of a smile. Indeed, if a customer decides to do its own repairs, GTI Spindle would lose that business. But, if that customer wants training on how to repair spindles, GTI Spindle will happily provide training. Of course, once a customer fi nds out what is involved in rebuilding spindles, he or she may decide to continue letting GTI Spindle do the job.
On one Thursday in July, representatives of two major corporations were visiting the Manchester plant. The head of the spindle repair lab at a well known aerospace company was training on how to rebuild Makino spindles.
Two plant engineering staff from he state of the art Hyundai factory in Montgomery, AL, watched as GTI technicians rebuilt spindles from their plant. Hyundai engineer Nick Harsanyi said he and maintenance technician Ricky Speaks were “training, learning and evaluating [GTI’s] services.” Their department is responsible for over 150 spindles in the CNC cell that manufactures heads and engines for the Sonata and Santa Fe vehicles, Harsanyi said.
Besides GTI Spindle’s headquarters in New Hampshire, the company has facilities in Bloomington, IL, Romulus, MI, and a spindle and machine tool repair shop onsite at Caterpillar Fuel Systems in Pontiac,IL. For more information, visit the company’s web site, www.gtispindle.com.
1 Comment
We have in the past. Give us a call at 603-669-5993.
Tim
GTI Spindle Technology