Today’s Machining World Archive: June 2007, Vol. 3, Issue 06
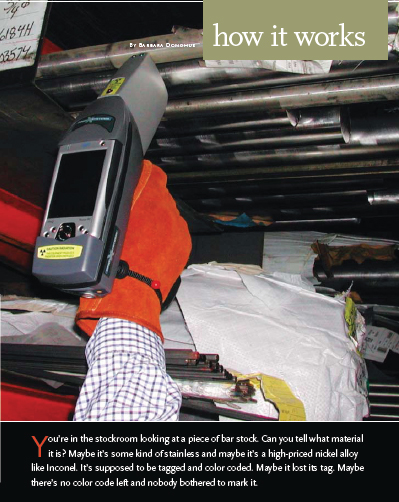
OK, it’s bar stock, but what is it really?
Do you have to scrap it? With the price of nickel up around $25 per pound, you could be making some scrap dealer very happy. So what do you do?
Fortunately, over the last century or so, a lot of very smart scientists have worked out how to analyze the chemical composition of many kinds of materials, including metals. The analytical instruments often used to do this are spectrometers.
Spec-what?
There are lots of different kinds of spectrometers. All of them take advantage of the innate characteristics of different atoms and molecules. Many measure how atoms or molecules affect the absorption, emission, or scattering behavior of electromagnetic radiation — infrared light or x-rays, for example — and use this data to determine the chemical composition of the material under test. Others, such as mass spectrometers, detect the behavior of the atoms or molecules themselves under the influence of magnetic field or other conditions.
So, you can cut off a sample of the mystery material and send it off to your local lab for analysis. They’ll likely use some kind spectrometer to do the job. In a day or two you’ll receive a report that tells you what the material is. The cost for the test will probably be $75 to $200, maybe more. And you can use the stock with confidence.
Historically, spectrometers were big and expensive and delicate, so they had to live in a laboratory. Nowadays, it seems, everything can be miniaturized and ruggedized, and that includes some kinds of spectrometers.
In your hand
X-ray fluorescence (XRF) spectrometers are now available in portable, hand-held and small benchtop analyzers you can use yourself in the stockroom, on the shop floor or in the QC department. XRF takes advantage of the fact that every element has a characteristic way it reacts to x-rays.
When x-rays strike an atom, it emits other x-rays — it “fluoresces.” Each chemical element emits x-rays at energy levels unique to that element. An XRF analyzer focuses a beam of x-rays onto a small area of the sample under test. The atoms in the sample fluoresce and the spectrometer detects and analyzes the energy levels and quantities of the resulting x-rays.
In a handheld unit, the x-rays come from either an x-ray tube, or from radioactive isotopes carefully shielded within the unit. You place the nose of the instrument on the part, press the trigger, and in less than a minute, the chemical composition and alloy designation appear on the unit’s display. You read the results there and can send them to your computer.
These small XRF analyzers aren’t cheap — expect to pay $30,000 or more, depending on options — but some shops have found they do pay for themselves. You can sometimes rent or lease them.
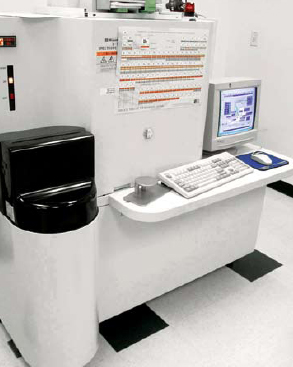
Consider your customers
DCI, Inc., St. Cloud, Minn., constructs tanks and storage vessels for dairy, food, pharmaceuticals and similar “sanitary” industries. They work in stainless steel and high-nickel alloys, said Brian Uhlenkamp, vice president of engineering and R&D. Material is absolutely critical to these industries. PMI — positive material identification — is what they’re looking for.
In 2004, the company acquired a handheld NITON XRF analyzer. “The material comes in and we add a lot of value to it—fabrication, machining. We [bought the analyzer] for liability [and] for our customers to know what they are getting.” Also, he adds, “to verify what we’re getting from our suppliers. We don’t put anything into stock without PMI-ing it.” Uhlenkamp said the analyzer paid for itself in about 18 months.
DCI has found material mismarked from distributors, and from mills, even when accompanied by certificates.
On one occasion, DCI needed to produce replacement parts in AL-6XN because the same parts in 316 stainless were failing due to corrosion. It was a good thing they checked the material, because the supposed AL-6XN stock they received turned out to be 316.
“Buyer beware,” said Uhlenkamp, “because you don’t know what you’re getting.” He said the company has been able to catch about 50 problems of this sort. “People assume bad material or wrong material comes from overseas. We’ve found it’s truly mismarking. We’ve seen things come in marked 304 and it’s really 316. [So] you know somebody isn’t trying to make a buck!”
A few months ago, DCI purchased another XRF analyzer, so they could have one in the plant and one in the field.
“We do random inspections on the shop floor. . . and final inspection on key components. Customers want the final report that says ‘that’s what this is,’” said Uhlenkamp. One customer even wants to watch in person when they do final testing with the XRF unit.
Getting out of a jam
Whether it’s raw material or completed parts, it’s got to be the right stuff.
Witco, Inc., an Avoca, Mich., machine shop, bought a NITON handheld XRF unit a few months ago. It’s been very handy in the stockroom for identifying stock. “We’ve had some where one end is one color and the other end is another color,” said, general manager Kevin Witt. “Now, we’re able to probe and verify [what it is].”
Once a material analyzer shows up in the shop, folks get creative about how to use it. Witt said his shop has used its XRF analyzer to help “reverse engineer” a broken machine part so they could produce their own replacement. “OK, it’s 4140, check the Rockwell hardness, and [we] made up our own,” he said.
Kevin Pelletier, sales and marketing manager at Massachusetts Materials Research, Inc., a lab in West Boylston, Mass., told about a shop that had machined 1800 parts out of different bar stock — grades of stainless and Inconel — and the parts got mixed. The customer received the parts and said “Something is wrong.” The shop tried unsuccessfully to sort the parts, and finally called Pelletier’s lab. An affiliate lab dispatched a technician to the shop where he used a portable XRF analyzer to separate out the different materials.
A shop had been running stock that it really liked, but was coming to the end of its inventory, and wasn’t exactly sure what the material was, said Michael Porfilio, quality management director at Anderson Laboratories, Inc., Greendale, Wisc. The shop owner sent a sample of the material for analysis, and the lab was not only able to identify it (a leaded steel), it told him what supplier to go to for more.
“A machine shop called and said, ‘We’ve been making this part for years and now I put it on the lathe and it’s tearing up my tools,’” said Jim Scannell, executive vice president, Dickson Testing Company, Inc., South Gate, Calif., a lab that deals mainly with forgings and castings destined for the aerospace industry. The shop sent over a sample and the lab tested it to find out what was different.
Scannell also told about a shop that was machining parts for an aircraft company and got parts from two heats (batches) of material mixed up. “You need traceability on aircraft parts,” he said. His lab was able to find small differences in composition between the two heats, so the shop was able to maintain material identity traceability. “It costs, but it’s cheaper than having to scrap out the parts,” he said.
Even after the machining is over and the parts shipped, an XRF analyzer can help you get the most for your scrap. A barrel of unknown chips might bring one price, while a barrel of Inconel chips, verified by a report from your analyzer, might bring a lot more.
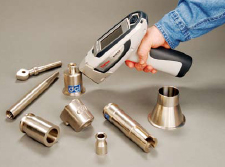
Handheld XRF can’t do everything
The standard XRF units cannot “read” the lightest metals, those with lower atomic numbers (magnesium, for example). “Argon in the air interferes with measurements of materials with lower atomic numbers, such as aluminum,” explained Tom Anderson, NITON marketing manager with Thermo Fisher Scientific, Bend, Ore.
NITON handheld XRF products offer a helium-purge option; the handheld units from Innov-X Systems, Inc., Woburn, Mass., offer a vacuum option. Both remove air from the interior of the unit, so they identify the lighter metals. In practice, if you know you have an aluminum alloy, you may be able to use a standard unit, without the options, to look at the other elements present and then use this information to determine which alloy it is.
For very small parts, you might consider a benchtop XRF unit, like those available from Matrix Metrologies, Inc., Holbrook, N.Y. They can analyze parts down to 2 mils in size, said Frank Reilly, company president.
Your XRF unit can do a lot, but for some analytical tasks, you’ll still have to go to the lab. To determine carbon content in steel or detect infiltrated hydrogen in titanium, specialized instrumentation is necessary. It’s probably a good idea to get acquainted with nearby laboratories, so when you need them, you’ll know their capabilities. Many will welcome you for a visit and give you a tour.
Maintaining identity
PMI: positive material identification – you’ll be hearing about it more and more.
“Aerospace and medical. . . Those two industries require stringent testing,” said Pelletier. “Others are all over the map. But one way I look at it is [you’re doing your] due diligence.” What would happen to your shop’s reputation if something went wrong, even if it was somebody else’s fault?
When you know about material identity and traceability, and how to use material analysis resources, whether in laboratories or with in-house analyzers, you can ensure that your customers get what they need, and your business gets the most out of your raw materials, the value you add, and even your scrap.