Today’s Machining World Archive: April 2006 Vol. 2, Issue 04
Stereolitography turns computer files into parts
A small spot of purple light scampers over the surface of the clear fluid in the tank of the machine. In about 15 seconds, the spot of light outlines a pistol shape. The perforated metal platform just below the surface dips a little deeper into the liquid resin. The platform rises again. A bar sweeps across the surface. Then the purple spot dances again. This process repeats again and again. Finally, the platform rises above the surface and the liquid drains away, revealing the two halves of a toy gun formed in translucent plastic. The magic happens every day here at San- Tech in Peabody, MA. It’s called stereolithography (SLA). It uses a special liquid resin that solidifies when exposed to ultraviolet (UV) light, similar to the dental filling material that is applied as a paste and then hardened with intense UV light.
Developed in the 1980s, SLA is one of several processes used to build mechanical parts directly from 3-dimensional computer drawings. Building parts by these methods is called rapid prototyping, a process used by more and more companies to help evaluate designs, especially for items that would be difficult or impossible to machine, such as molded plastic or cast metal parts. The technology is also finding additional uses in other areas. In medicine, for example, SLA helps doctors visualize surgical plans and makes it possible to create a customized implant for patching up a hole in a patient’s skull.
Some large companies have their own SLA machines, but many businesses find it more cost-effective to send out rapid prototyping work to a company that specializes in it. One such company is San-Tech, a Peabody, MA, division of Res-Tech, Inc., a Clinton, MA, plastics molding company. San-Tech’s four employees provide SLA prototyping and other product development technologies to a wide range of industries, including medical devices, transportation, electronics, sporting goods, appliances and toys.
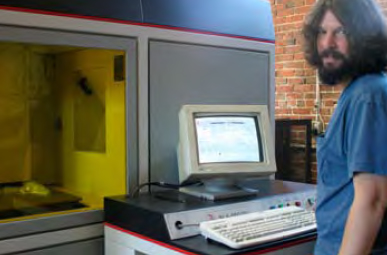
From computer file to reality
To build a part with SLA, the process begins with a special computer file, an .STL file, which can be created by any 3-D drafting program, explains San-Tech operations manager Carrie Denley. When a customer sends San-Tech the file, usually by e-mail, Denley quotes the job based on the dimensions of the part and the volume of material to be used. She says a typical prototype made by SLA might cost a few hundred dollars. Normal turnaround time is three to five days, but San-Tech can turn parts around as quickly as two days if needed, Denley says.
SLA manager, David Caron, loads the customer’s .STL file into a specialized SLA program, which adds the support structures that will attach the part to the perforated metal platform and support any thin-walled sections while the part is being built. The San-Tech SLA machine builds parts in layers 0.006″ thick, so the program needs to “slice” the part and its supports into 0.006″ layers. Other SLA machines can lay down layers as thin as 0.002″. Caron checks the part/support scheme for problem areas, such as sharp edges on the bottom of the part that might need extra support. Then he sends the sliced file to the SLA machine.
Layers and laser light
The heart of the SLA process, a solid-state UV laser, is mounted in the base of the SLA machine. The laser light first passes through optic elements that focus it into a consistent, round beam 0.012″ in diameter.
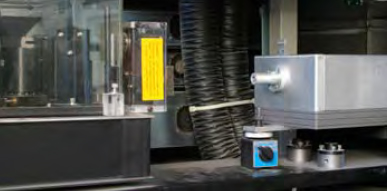
The beam then reflects from the surfaces of two small mirrors that are attached to small servomotors. The SLA machine’s computer controls the servomotors, which tilt the mirrors this way and that. This moves the beam so it can trace the shape of each slice. After the small mirrors, the beam reflects off a fixed mirror at the top of the SLA machine, which directs it at the surface of the liquid resin. There, the beam, moving at about 200″/second, “draws” a slice of the part being made. Wherever the laser shines on the surface, the liquid resin solidifies into plastic.
After each slice is drawn and solidified, the “elevator” that holds the platform moves down, submerging the part, to allow the liquid resin to flow on top of the area just solidified. Then the elevator places the platform 0.006″ below the previous location. Some of the resin, which is the consistency of molasses, stays heaped up on top of the part. The “doctor bar” moves across the surface of the tank, leveling the resin on the surface of the part to a thickness of 0.006″. Then the laser traces another slice. Once the machine is started, it can run unattended, Caron says.
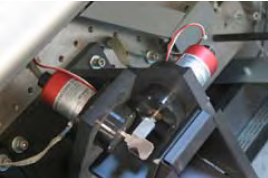
Layer by thin layer, the part is built up. The toy gun parts shown here took about six hours to complete. While the parts are being built, they remain beneath the surface of the liquid, so they are not visible until the process is complete and the elevator raises the platform above the surface.
When the parts are complete, the platform is removed from the machine and the parts cut off by hand. They are washed in alcohol or a chemical bath to remove excess liquid resin. The base support and any internal supports are removed by hand. The parts spend a couple of hours on the turntable in the post-processing apparatus, a sort of super tanning bed that shines intense UV light on the parts to cure any remaining liquid resin. Uncured liquid resin would make the parts sticky.
The parts are then hand sanded to smooth the layer lines and blasted with glass beads to further smooth the surface. The completed parts may be dyed or painted, according to the customer’s needs, or may be used to make a mold that can produce dozens of additional parts.
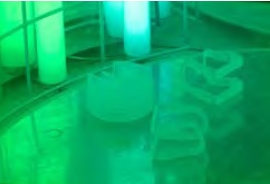
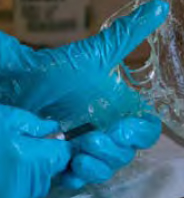
Many parts from one part
To create a mold, the SLA part is placed in a wooden box, rods are placed to create holes in the mold for filling and venting, and the blue silicone material is poured around the part. When the silicone hardens, the mold is opened up. The SLA part is removed, and the mold is ready to produce two dozen or more replicas of the original part. If the part is simple and doesn’t have a lot of fine detail, the mold might be good for making 50 parts.
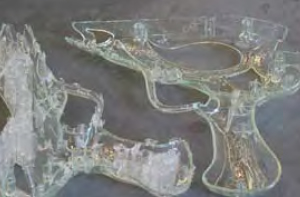
A two-part urethane material is mixed and quickly forced into the mold. Then the mold is placed in a pressure chamber until the new part is set. Clear and colored urethanes are available. The molded parts are tougher and more stable than the original SLA prototype.
Any size or shape that fits
A part can be built as large as the vat of liquid resin in the SLA machine. Denley says that the vat in San-Tech’s machine is 18″ by 19″ in area, and the company usually uses a “half-vat” that is 11″ deep. For larger parts, a full vat can be used. She points to a prototype transmission casing for a delivery truck that took up nearly the whole volume of a full vat. That prototype took five days to build in the SLA machine, Denley says, and turnaround for the job was just one week. “[You] couldn’t get that built in six weeks at a pattern shop,” she comments.
When making smaller parts, it is possible to build multiple parts at the same time, Denley explains. The SLA software can automatically multiply a single part and locate dozens of parts on the platform.
San-Tech uses one type of liquid resin, DSM Somos 11120. This produces a fairly hard part that is good for making molds. Many other UV-curable SLA resins are available that produce parts with different mechanical properties, such as flexibility or resistance to high-temperatures.
Hold it in your hand
“In today’s world, everybody wants it yesterday,” says Brian Driscoll, operations manager at Precision Tool & Die, Derry, NH, a company that uses San-Tech’s services. Many of his customers start out with just a concept or general idea what they want. Precision’s engineering staff turns the idea into drawings. “[Then we] ship the drawings to Carrie [at San-Tech],” Driscoll says. “In three to five days, you can hold it in your hand.”
Driscoll says many of Precision’s customers are seeking funding to develop and manufacture their product ideas. An SLA prototype, nicely finished, gives potential investors something to look at, handle and envision as a real product. This can be much more persuasive than a set of drawings.
Driscoll tells about one customer, a golf course maintenance superintendent, who had an idea for a new tool to help with greens keeping. He came to Precision just a few days before a big trade show. With an SLA prototype prepared and painted to look like the real product, he received orders for the tool at the show, even though he had yet to manufacture any.
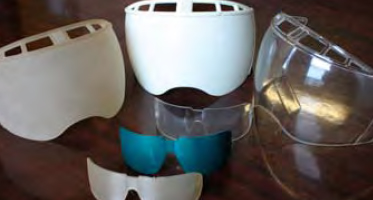
The wide world of SLA
The San-Tech division was created in 2002, but the four staff members worked for the predecessor company and have between nine and twenty-nine years of experience. Denley says she started out in accounting but now knows the whole business, from running the SLA machine to keeping the books. It is clear that she and the others enjoy the work. “We get new stuff all the time. It’s never boring,” she says, indicating with a sweep of her hand a display of SLA-built prototypes that includes a bottle for antacid tablets, an electronics housing, appliance parts, safety goggles, fasteners and an assortment of parts for toys and games.