Today’s Machining World Archive: October 2007, Vol. 3, Issue 10
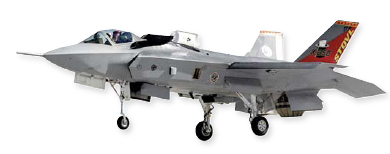
2017—Your business over the next decade
As someone working in the machining industry, you’ve experienced competition with other shops within the U.S. and the threat of your work going offshore. Your customers want greater precision and lower costs, and, oh, by the way, more frequent delivery of smaller quantities. And on top of that, you can’t find staff to run your machines. Squeezed from all directions, what do you need to do to stay competitive and stay in business?
Here are some other perspectives on the future of machining from people in both academia and industry.
Same objectives
Your goals will be the same as they have always been: increase production, decrease cost, increase precision, decrease defects.
Among machine tools, the progression will continue toward faster, more precise machines, incorporating more machining capabilities. Turn-mill machines will become more and more popular (see September TMW). Machine tool manufacturers will increasingly analyze stresses and track temperature rise to achieve just that little bit more precision. More rigid machines will allow increased cutting speeds without sacrificing accuracy.
Faster setup, faster changeover, faster cutting. Larger capacity tool magazines. More pallet systems. Auto-load/ unload. Machine monitoring. Unattended operation. Automated measurement. Many steps toward taking labor cost out of the product.
Which, as it turns out, is a good thing for American shops. It helps cope with the lack of experienced machinists and operators, and also makes it more possible to compete with shops in low-wage foreign countries.
Large companies that used to do all their own machining will increasingly outsource the work. This can be good news for you, since “out” could be to your shop, and not necessarily to China. New computer-based systems are becoming available that help make outsourcing work.
You will see many new products and technologies, of course. And some that are in limited use now will become commonplace over the next several years.
Tooling catches up
As spindle speeds go up and cutting speeds get higher and higher, tools will need to keep pace, said William Endres, associate professor of mechanical engineering, Michigan Technological University (MTU), Houghton, Mich. His research at MTU and in his business, Endres Machining Innovations, includes investigating cooling, chip breaking and new coatings to increase tool life. New coatings will not just be more layers, he said, but will be substantially different. One cooling technique he is investigating uses ordinary tap water flowing through micro passages within the cutting insert.
In addition to incremental improvements in cutting tools, look for radical new designs, like the rotating-insert tools that are now available from Rotary Technologies Corp. These tools have round inserts that rotate during cutting; this reduces machining forces and can extend tool life.
Besides upgrades of the machines and tools, many of the upcoming changes will involve machine and part data and the software to make use of it.
Making connections
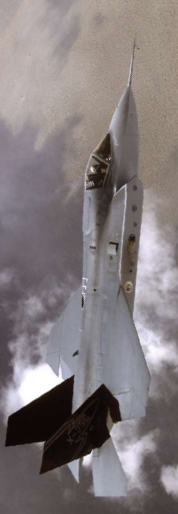
Today, every manufacturer, whether of machine tools or measurement instruments, seems to have its own proprietary electronic communications format. It would make life in the machining world much easier – and potentially more profitable – if all the different devices could “talk” t each other.
To fill this need, the Association for Manufacturing Technology (AMT), working with technical experts at University of California, Berkeley, is developing an open software standard for passing data among the machines, instruments and other devices likely to turn up in the machine shop, according to Paul Warndorf, vice president for technology at AMT, McLean, Va. The new standard, MTConnect, will be an open, freely accessible way to get data out of the machine. Your CAM package or other software on your network can use the information available from the shop floor, such as spindle time, temperature rise, and cycle times.
“Where MTConnect fits in: a lot of companies have a lot of interest in characterizing how their process is working on the shop floor,” said David Dornfeld, professor of mechanical engineering at UC Berkeley, who is working on the project.
In the future, machine tools will be network compatible, said Daniel Frayssinet, CEO, Esprit/DP Technology Corp., Camarillo, Calif. “Plug into your LAN [local area network] and your machine will connect itself to the network.” Think back 15 years, he said. Remember what it was like to connect a printer to your computer? You had to load a special printer driver. Then along came USB (universal serial bus), and “Now, you buy a printer and plug it in,” Frayssinet said. In a similar fashion, machine tools will use a similar open communications standard, so all your machines and all your sensors can communicate easily over your computer network.
Will it fit? Verifying parts remotely
As large manufacturers outsource more and more parts to more and more locations across the country or even around the world, a key to making this work will be control of dimensions so that when parts come in, they’re right the first time and fit together properly.
The Advanced Integrated Mathematical System (AIMS) software improves communications and collaboration between an OEM (original equipment manufacturer) and its suppliers to help make global sourcing work, said Troy Niehaus, vice president, AIMS business unit, Metronor, Inc., Seattle Wash. AIMS was developed by the Boeing Company in the U.S. and the Metronor Group, Norway.
It’s a challenge to exchange measurements and other data with suppliers, who are all working in different places with different hardware and software systems, Niehaus said. However, AIMS is “hardware and software independent and helps to insure integrity throughout the entire dimensional management process.”
Eighty-five percent of metrology companies offer AIMS-compatible software upgrades, Niehaus said, so manufacturers can use their existing measurement equipment to communicate the data in a standard AIMS format.
Starting with the CAD files, AIMS allows the OEM to specify critical dimensions and set up inspection procedures. This information goes to the suppliers, who perform the needed measurements at their sites. The measurement data is incorporated into the file and transmitted over the Internet back to the OEM, who can then verify the parts before they ship.
AIMS is already being used by Lockheed Martin on the JSF F-35 fighter aircraft project and in a number of projects at Boeing, Niehaus said. Look for software tools like AIMS to come into widespread use over the next decade.
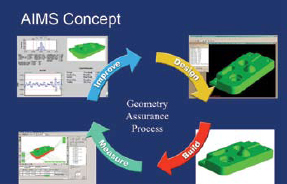
Learning on the job
With the retirement of many machinists and loss of technical school training programs, staffing shortages will continue to plague the US machining industry.
In addition, “there’s a technology gap,” said Rod Jones, chief learning officer at Mori Seiki University (MSU), Rolling Meadows Ill. New staff needs to learn how to operate the machines, of course. But even experienced operators, programmers and maintenance techs may not know the latest and greatest features of a new machine, so they can’t take advantage of all its capabilities. This could mean the machine won’t be as productive as it could be.
Mori Seiki University is developing interactive online training classes for basic and intermediate learning, both specific to Mori Seiki machines, and general subjects such as print reading. MSU has just introduced its first “Education-On-Demand” online learning module for a Mori Seiki machine, with more to follow, Jones said. Online training is available round the clock, Jones said, and employees can work through the short modules at their own pace. It is an effective way to provide the ongoing training required by ISO 9000 and other standards, he said.
Your company can have its own customized computer-based training created by companies such as Oxygen Education, Indianapolis, Ind. In the next few years, companies are likely to depend more and more on this type of training to keep employees’ skills up to date.
Help on the machine
Another way to help make the most of available staff is computer-based help to guide them in their work space.
Mechanical engineering students at Worcester Polytechnic Institute (WPI), Worcester, Mass., create designs and then machine all the parts themselves, said Torbjorn Bergstrom, operations manager of the manufacturing laboratories and an adjunct professor at WPI. A semester or more may elapse between when students take their machining class and when they’re making parts, he said, so the machining lab has a quick guide on computer available at each machine to help them get up and running.
Bergstrom expects that approach to become standard in the industry. He can see a computer next to each machine offering guidance through setup, as well as operation and troubleshooting assistance, with instructions and visual information. “If the surface of the part looks like this, turn this knob.” Less experienced operators will be able to more safely run the machine and turn out good parts.
Look for this type of on-location help system to become commonplace. What else are you likely to see on the training front in the next few years? “Virtual reality,” said Jones of Mori Seiki University. You’ll be able to put on virtual reality goggles and see the machine in front of you in three dimensions, and to interact with it,” he said.
Software that thinks
Expect smarter software that can read the machine and part conditions, anticipate problems and then instruct the operator what to do.
Since cutting tools wear and break, ordinary statistical process control (SPC) methods don’t apply well to the machining process, according to Stephen Birman, president, High Tech Research, Inc., Deerfield, Ill. His company’s Micronite software provides machining process control, including real-time data analysis and decision-making capability. Specifically designed for the machining process, Micronite analyzes part dimensions, and machine and tooling data, then determines whether there is, or soon will be, a problem. If so, it tells the operator what to do – make an adjustment or change a tool, for example. Much of what will keep you competitive in the future are the same good business practices you’ve used in the past. In addition, you will be able to count on new technologies in machines, tools and especially software to help keep the orders coming in and the parts going out.
Much of what will keep you competitive in the future are the same good business practices you’ve used in the past. In addition, you will be able to count on new technologies in machines, tools and especially software to help keep the orders coming in and the parts going out.