Today’s Machining World Archive: March 2007, Vol. 3, Issue 03
A drill breaks and then the reamer tries to do its job, and it breaks, too. On a machine running unattended, a tool wears prematurely and creates thousands of bad parts. A large, high-priced indexable tool hits a misaligned part and destroys itself.
Shops commonly change out tools on a schedule conservatively based on experience. But tool breakage and wear can be unpredictable. What if a machine could sense exactly when a tool breaks or wears beyond usefulness, then shut itself down, or even load a new tool?
Many different technologies offer tool and machine monitoring, from detecting whether an intact tool is present to measuring a tool’s profile. Some can even measure the power consumed by the spindle motor and use that information to control the feed rate and minimize machining time. Here are a few of the many options available for keeping track of the condition of your tools.
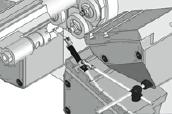
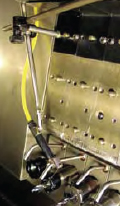
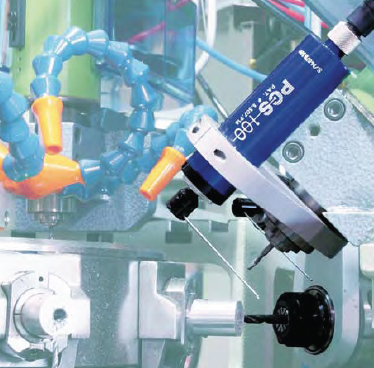
Detecting broken or absent tools
Small, simple tool detectors check for the presence of a drill or other cylindrical-shaft tool. Their small size and simple operation adapt them well for many environments, including machining centers, screw machines and transfer machines.
A small cylindrical housing contains an electric or pneumatic actuator which rotates the detector wire (or “needle” or “wand”) through an arc. Mount the detector so the wire will touch the tool and stop if a tool is present and undamaged, and swing right by if the tool is broken. Only the head of the detector device, containing the actuator and the wire, is located inside the machining area. It can be positioned on fixing rods, with magnets or by drilling and mounting, said Joel Rutzen, manager of service/ customer support at SPC Innovations, Inc., Stevensville, Md.
When the detector is actuated and the tool is intact, the wire touches the tool, rests briefly, and then returns to its original position. If the tool is broken or absent, the wire sweeps past where the tool should be, and an external switch or control unit sends a signal to the machine control to stop the machine.
“Generally, a tool monitor [is] best compared to an air bag,” said Dean Bentzien, CEO at TPS International, Sussex, Wis. “It won’t prevent a tool breaking, [but] it will minimize the damage done after it has broken.” For example, if a drill breaks, the machine can be stopped in time to prevent damage to the tap used in the next operation.
This type of direct-contact tool detector is available in many different styles and typically costs in the neighborhood of $1000. For example, SPC Innovations offers two models of air-actuated Detector broken tool sensors, type 101 and type 202, both with $895 price tags. TPS International’s Positive Contact sensors, PCS 100 and 250, are electrically actuated, and can be installed for “under $1000,” according to Bentzien.
In a study performed by TPS International, customers found that contact tool monitors paid for themselves in under a year, sometimes in as short a period as one week, and one customer said the payback period was one day.
Power monitoring
Directly monitoring the power consumed by the spindle motor allows you to understand exactly what is happening with the tool. A new, sharp tool requires less power to cut than a worn, dull tool. Power monitoring systems are available that take their data directly from the motor controller; others measure with transducers on the wiring to the motor.
“We call what we do ‘sensory perception’ for machines,” said John Maher, director of business development at ARTIS Systems Inc., Livonia, Mich. “[The system obtains] information that would not otherwise be detectable and notifies the operator as soon as possible when there is a problem.”
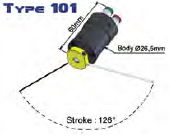
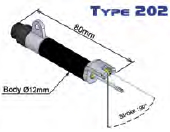
When first setting up a job, you run a “learn” cycle with new, sharp tools, during which the power monitor takes data, which it “remembers” for future reference. The monitor sets a range of “normal” operating levels, or you can manually set the limits you want.
Then, when you’re running production, the monitor notices when the power goes beyond one
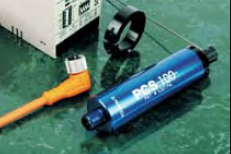
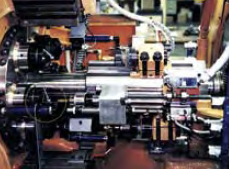
of the limits for the particular tool that is running. If the power goes up suddenly, that may mean a crash or a broken tool, and the monitor sends a stop signal to the machine control. Also, as the tool wears, the power it requires goes up gradually. You can set the monitor to send a stop to the machine control when the power has risen to a certain level due to wear. If the power is much less than expected, this may indicate that the tool is missing or is not contacting metal.
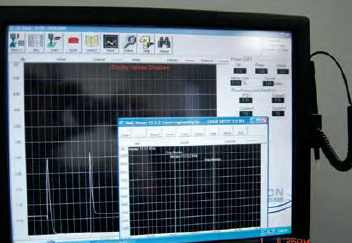
These systems are not inexpensive, but they can pay for themselves over time, sometimes quickly, especially if one is using expensive indexable tooling. “One customer was blowing multiple drill bodies per day,” said Rob Caron, president of Caron Engineering Inc., Wells, Maine. The monitoring system “paid for itself in about two weeks,” he said.
“Another big piece is unattended operation—one guy operating nine machines,” Caron said. “Monitoring allows them to do that.”
Wear monitoring can help make lights-out machining feasible. “We have customers who go home at night, often running $300 to $500 tools,” Caron said. When the power monitor detects excessive wear, it can signal the machine control to initiate a change to a fresh tool from one of the spares provided in the tool carousel, and keep on cutting.
Adaptation
Not only can power-monitoring units detect broken or worn tools, but with an “adaptive control” option, you can use them to control the feed rate, reducing machining time, yet extending tool life by keeping the tool load constant and well under maximum stress.
Under adaptive control, the monitor tells the machine control to increase the feed rate when the tool load is low, when the tool is new and sharp, for example and reduce the feed rate when the tool load goes high, as when the tool gets worn and dull. Versions of adaptive control are offered as options on the ARTIS and Caron systems. Within adaptive control, you can also manually set limits to the range of feed rates at which you want the machine to run.
“Machining times can routinely be reduced by 7 to 20 percent, sometimes as much as 40 percent” by using adaptive control, Maher said.
Caron related comments from two adaptive control users. At one customer, the monitor would shut down a machine before the tools broke, so they could be reground and re-used. “The tooling budget went down so much that the procurement guy [got curious and] asked why they weren’t buying.” A customer that makes aircraft parts told Caron that on machines with adaptive control, they hadn’t broken a tool in five years.
An ARTIS CTM system including setup and training ranges from $7,000 to $12,000, depending on features included, such as adaptive control. A Caron TMAC 7 system lists at $12,000 including board, installation, software and training. Integrating adaptive control with the TMAC 7 system adds $1100. Coolant monitoring is also available, with transducers from $1500 to $3200, depending on pressure and maximum flow rate.
Laser focus
A laser tool monitoring system, such as the LaserControl NT from Blum LMT, Erlanger, Ky., can measure the length of the tool, its diameter and its form, on the machine.
When a tool interrupts the laser, the instrument produces a trigger signal to read measurements based on the axis position. A laser unit can monitor single-edged tools and can also monitor multiple-edged tools as they rotate. Tools can be measured while rotating at speed, so you can make a runout measurement. Also, the laser can be used to measure changes due to thermal expansion and mechanical effects. And, said Paul Meinhardt, general manager at Blum, “We can feed the measured value for [actual] offset compared to the programmed value, to correct it in the [CNC] program.”
Some laser systems from Blum (pronounced “bloom”) use a U-shaped transmitter/receiver housing like the one shown, which is often mounted to the table in an out-of-the-way location. If there is no convenient mounting position in your machine for this type housing, a configuration with separate transmitter and receiver units is also available. During machining, the optics are protected by a pneumatically operated mechanical shutter, and, during measurement, an air blast prevents contamination of the optics.
Blum laser systems are often installed by the machine tool manufacturer or rebuilder, but they are also available as retrofits. The cost for a Blum system is around $12,000 to $15,000, including installation, said John Sherrick, manager of system integration at Blum.
Tapping monitor
Always a challenge, tapping is frequently the last process performed, so a lot of machining and labor hours may already be invested in the part. Sensitive torque monitoring during tapping can detect tool wear and damaged threads, so the monitor can call for a machine stop within milliseconds of sensing a problem.
The DDU4 noncontact sensor from ARTIS Systems has piezoelectric sensors that install on the toolholder. A stator unit receives the data from the sensors. The DDU4 can be installed as a standalone unit or integrated with the machine control through an ARTIS CTM card system. The DDU4 senses both clockwise and counterclockwise torque, and both positive and negative feed force. With CTM integration, it can detect deviations in core hole diameter and thread depth. A standalone DDU4 system is priced at $4000 to $5000. DDU4 with CTM card integration is in the $8,000 to $10,000 range, said John Maher of ARTIS.
Force
Monitoring cutting force is especially useful for some processes. Force measurement is often made indirectly, by placing a sensor on the machine in an area that experiences strain proportional to the force you want to measure.
Srinivasa Prasad, national sales manager at Montronix, Inc., Ann Arbor, Mich., gave an example. “On a CNC lathe what we do is embed a 3-axis load cell beneath the turret. This gives the machining forces in the x-y-z [axes, from measuring] the bending moments on the turret.”
“Cutting tool degeneration is not predictable,” said Prasad. “By monitoring in real time, we have an idea what is happening in the machine, so we can optimize tool change frequency.” Machining centers, CNC lathes, drilling and reaming processes are ideal applications for force monitoring, he said.
As with other monitoring techniques, force measurement can tell you about the condition of the tool and also signal the machine to stop when there is a major problem such as a misloaded part. You can monitor the mini-collisions and crashes, and minimize the damage, so you can have the machine backin operation quickly, Prasad said, “breaking the tool instead of breaking the machine.”
Listening to small tools
Very small tools, 2mm or less in diameter, can be difficult to monitor using force, torque or power. For this situation, ARTIS Systems offers an acoustic monitoring technique. A small acoustic sensor is installed in a location where it can “hear” differences due to breakage or wear. The monitoring system learns the sound/vibration characteristics of normal machining, and sends an alert or stop signal when it detects a deviation outside the normal range. The standalone version is $3,000 to $4000; integrated with the ARTIS CTM card, it is $7,000 to $8,000.
Is tool monitoring for you?
tool monitoring for you? Tool monitoring offers solutions to many machining challenges.“By monitoring in real time we have an idea what is happening in the machine,” said Prasad. He offered the following guidelines for deciding whether you should consider tool monitoring on your equipment.
• If you are using very expensive tools or making very expensive parts If your tooling costs are abnormally high
• If you have had a series of wrecks on a machine and are not able to control the amount of downtime and maintenance• If you want to reduce cycle time• If you want to reduce cycle time
When you run into everyday frustrating problems – an end mill breaking mid-cut, a worn tool producing bad parts – consider the benefits and investment value of tool monitoring. A monitoring system may pay for itself in a fairly short time. And from day one it could save you from some of the headaches that seem to be part of the machining business.