Interviewed by Noah Graff
Today’s Machining World Archive: December 2008 Volume 4 Issue 12
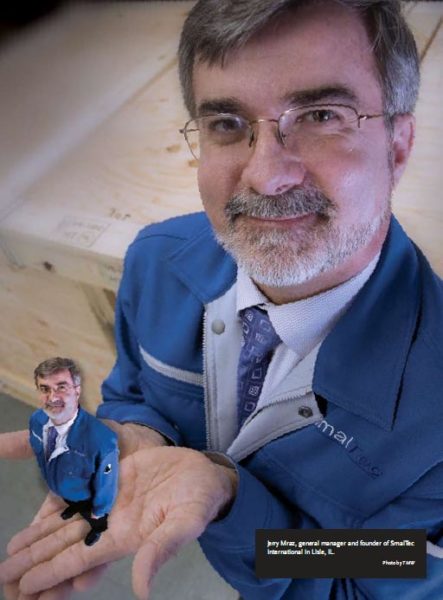
Jerry Mraz is general manager and founder of SmalTec International, a leading high-tech manufacturer of micro-technology products. SmalTec is both a builder of micromachining equipment and a job shop which produces micro parts for the medical, aerospace and optical communications industries.
Do you classify the machines you sell as micro-EDM?
JM: Micro-EDM is the primary function of the platform, but they also have micro-milling, micro-drilling, micro-grinding and polishing capabilities as well. It depends what process you need. That’s why I prefer to say “micro-technology,” because we’re not really just one process in the micro-technology world, we kind of cover them all.
What can a job shop do to break into the medical sector?
JM: The primary way we find leads in the medical device industry is by visiting or exhibiting at tradeshows. There are probably 15 different tradeshows around the U.S. that focus on the [medical] market. It’s a matter of getting an introduction to that customer base. These shows attract a lot of medical device design manufacturers who are looking for solutions to manufacture their components.
What’s your biggest challenge as both a job shop and a machine tool producer?
JM: I think the biggest challenge for everybody manufacturing these medical devices is how to make them smaller. [SmallTec] has specific or specialized machine tools that can go beyond [the capability] of what’s [currently] being designed. I think our biggest challenge and our customers’ biggest challenge is to educate designers and medical device manufacturers that things can be done better, smaller, and with tighter tolerances, using new technologies or current technologies that are available.
What is the main drive for continuing to make parts smaller and smaller?
JM: We made some tweezers with a pad that was probably about a millimeter by a millimeter, and on that pad were about 100 little grippers. It’s very small but a very effective gripping tool. It enables you to pull the skin with very little pressure while still having a very small incision. It gives you less chance of infection. That’s really the big drive for these small tools in surgery. How do we get into the body without making a large incision that has to heal and opens the body to more possible infections? To make a small incision you need to have small tools. To get in and use that small incision you need even smaller tools.
Tell me about one really exciting medical device you predict will be available 10 years from now?
JM: There’s a lot of development going into what’s called “lab on a chip.” You will take a fluid, and this little chip mechanism that’s the size of a credit card will decide what’s in the fluid, analyze the different antigen and protein that are in there and be able to detect different types of harmful things. In 10 years time I could see these micro-fluidic devices being available in doctors’ offices, and 10 years after that being available on the shelf as a self-test kit. Imagine going to the drugstore and saying “I think I’ll pick up that cancer test for early detection” — not necessarily a true test but like a pregnancy test. If it comes up positive then you go to the doctor to make sure.
If you could be any machine what would you be?
JM: Well, obviously my machine, but I don’t think we’re the best at everything and I don’t think there’s one machine that is the best at everything. Things are getting so small you need to have different processes on one machine. That’s one of the biggest challenges: How do you get one part located and do everything you can before you take it off? It’s so small that once you take it off you’re not going to be able to put it back and find the right location.
Swiss turning, CNCs, multiple axis machines — those are all great for certain things, but the parts are going to be too small to put on those platforms. Evolutionarily, the machine has to change.