Interview by Noah Graff
Today’s Machining World Archives June 2008 Volume 04 Issue 06
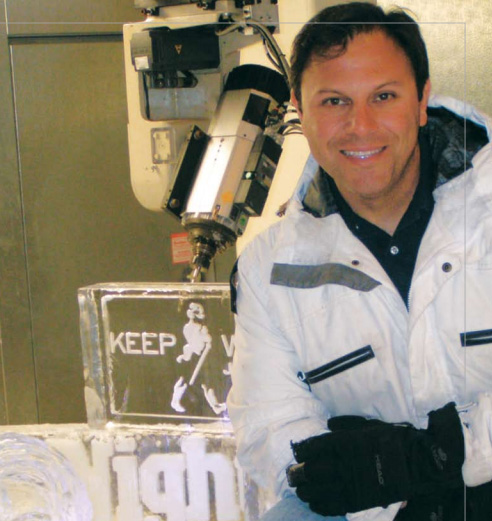
Ice sculptor Roland Hernandez is CEO and founder of Carving Ice, an ice sculpting company that provides pieces for events including weddings, parties, and corporate gatherings. Eight years ago he began using CNC routers to compliment his traditional sculpting methods.
NG: How did you get into the ice sculpting business?
RH: Right out of high school I managed to get into an apprenticeship program under a master chef at the Century Plaza Hotel in L.A. The chefs there are required there to teach you as much as they can, and I saw a gentlemen cutting ice and said, “I think I can do that.” As means to support my way through [college], I started [doing ice sculpture] as a business on the side. Six months into college I was so busy I decided just to do that.
NG: How do you use the ArtCAM software? How does today’s ice sculpting process work compared to what it used to be?
RH: We take our blocks of ice and we put them onto our deck. We’ll freeze them down to the deck so we don’t have to actually use any type of clamping system. Then, once the design is created in ArtCAM, you see what vectors and spindle feed rate and actual bits that you’re going to be using. You input it into ArtCAM and then upload the file and press start. The machine does the rest. Imagine a CNC that cuts wood or plastic or aluminum. It’s just put in the freezer.
NG: Does the sculpture you do by hand look as good as the one from the machine?
RH: Sometimes you can’t tell which is which. The amazing thing is that hands-down the CNC will beat me on any kind of logo work or anything that looks mechanical – anything that has straight edges. What it comes down to are three-dimensional pieces. The machine can’t really replace me too much when I’ve got to cut a lion and I use taps, certain muscle texture and movement within a reasonable amount of time.
NG: Do you have any favorite projects you’ve done?
RH: Usually my favorite projects are when I’m able to take pieces off the machine and incorporate it into designs that I’ll do. Two days ago, we did a 12-foot long sail ship that was actually an ice bar for one of the liquor companies. The machine routed out most of the ship for me. The front helm had the sea mariner, the women with the bust on the front of the ship. A silhouette of the image was cut onto the block of ice for me off the machine. Then I finished it, sculpting it by hand.
NG: What project was really difficult for you?
RH: The daughter of one of our big clients was getting married. She told me, “Roland, I don’t want to make this complicated. All I’m looking for is an oak tree that I can actually get my drinks out of.” So what wound up happening is again we did a 50/50 combo. I told everybody, “Okay, let’s just build it, get the blocks set up and then let me have at it with the chainsaw.” The elements that needed detail with the leaves and branches we did on the CNC machine. We made a 12-foot wide sculpture, but the tree was almost 8-feet tall and about 9-feet wide. In the end, the bar looked great.
NG: What is the price range for ice sculptures?
RH: They’ll range from as little as $85 for a piece that’s in a box, to a nice big bar or ice lounge for anywhere from $5,000 to $10,000.
NG: How do you keep the stuff from melting?
RH: You would think here in California we would use freezer trucks, but we actually just use mover padded blankets and dry ice.
NG: How do you keep warm when you’re in the freezer?
RH: It looks like we’re going skiing all year long.
NG: Thanks Roland.