Interviewed by Noah Graff
Today’s Machining World July 2008 Volume 04 Issue 07
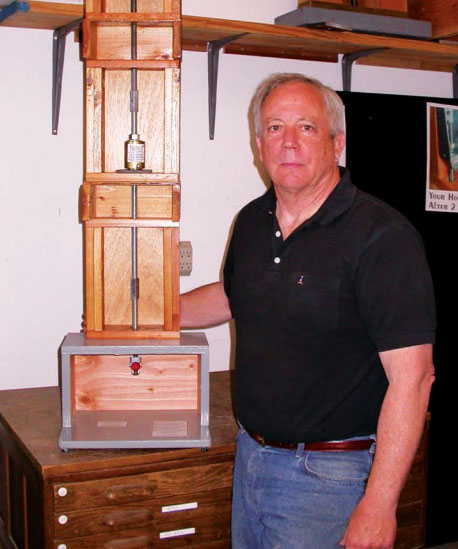
Al Commins, president of Commins Manufacturing Inc., invented the AutoTight Rod Holdown system to protect buildings from earthquakes and high winds. His patented system uses threaded rods (8-16 feet long) and steel plates to connect floors and ceilings. The AutoTight take-up system automatically expands as the building shrinks, and settles. This tightness keeps walls tight and helps prevent damage and collapse.
NG: Where have you installed AutoTight?
AC: Our market basically starts in British Columbia, Washington, Oregon, California, Nevada, and actually in New York. But primarily it’s West Coast earthquake region. It also is perfectly applicable to high winds, so if you’re in a tornado or hurricane region it’s quite appropriate.
NG: Do you see expanding your sales worldwide to China or other places with recent natural disasters?
AC: The way we build in the U.S. is typically quite different. Many parts of the world use masonry and there’s different ways to handle loads with masonry. Our primary market is wherever they build buildings out of wood; primarily retirement homes, apartments, condos, small hotels up to five stories, and mixed use buildings.
NG: Did the recent Chinese earthquake bring your company business?
AC: Anytime there’s an earthquake or a major disaster there’s a short-term, heightened interest for a couple years and then people tend to forget. The problem and the good news about earthquakes and high wind events is that for the most part, they are typically local and don’t happen very often. The last great earthquake in the State of California was in 1906 in San Francisco.
NG: If there is a very small chance a person will need your product, does it make it hard to sell?
AC: There’s probably a one percent chance, or at least a very low probability that you’ll need our product in any given year. But there’s a 100 percent probability given the right timeframe that a building is going to be shaken with a massive earthquake. The [building] code actually says you’ve got to tie your buildings down. But the number one thing is safety. That’s easy; we don’t want people to die. It’s hard to sell property preservation because we don’t know enough to prevent all the damage in buildings.
NG: How did you decide where to have the part produced?
AC: When I was first making it, I actually made the first one here in my own shop on a manual lathe. I talked to machine shops, who said “Oh no, no, you can’t do that.” I said, “Well of course you can.” Trying to get something made the first time is simple if you have a part in your hand. You can look at it and say, “Okay, now I understand.” But if you look at a piece of paper, it’s hard to explain to people exactly how it works. So I made some working prototypes and I went and visited some shops to get it made in a cost effective way. It’s amazing; people can’t read prints. The print said it’s a left-handed thread; it came back as a right-handed thread. They said, “Well, we can’t do this; we can’t do that.” I mean, these are shops with CNC machine tools that are serving aerospace stuff, making all sorts of fancy stuff. You look at my product and how simple it is, but they said they couldn’t make it.
NG: Why didn’t they think they could make the part?
AC: Originally it had four starts and I’ve gone to six starts. But the multi-start thread just sort of threw them. Today, we’ve progressed to the point where our threads are being rolled. After I went through a couple shops I finally found a shop that was willing to do it, and we’ve been with them for about eight years now.
NG: Thanks Al.